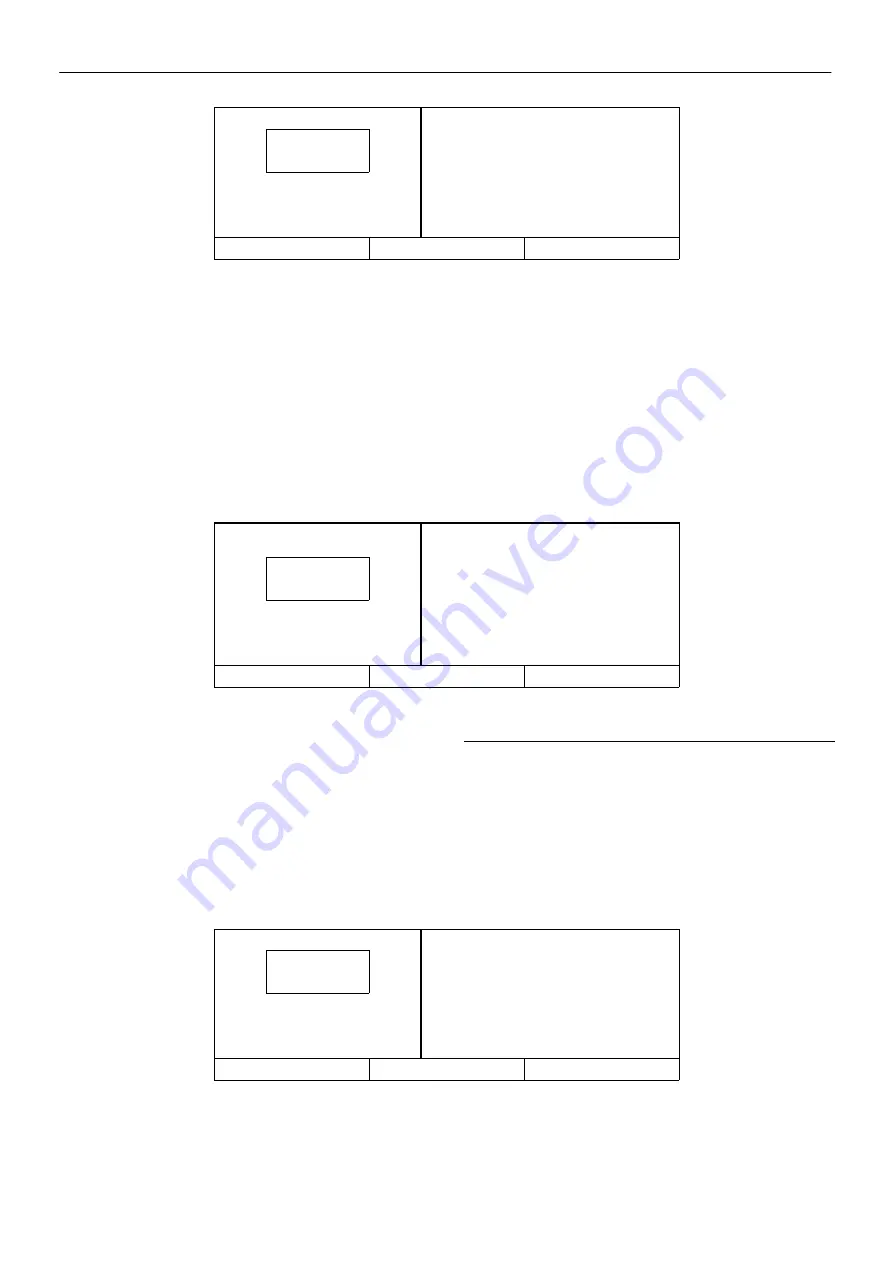
OPERATING INSTRUCTIONS
29
M200–LV M250–LV
–CURRENT STATUS–
barg
7,5
barg
PACKAGE DISCHARGE TEMP
39,4
_
C
RUNNING UNLOADED
AIREND DISCHARGE TEMP
MODE: MOD/ACS
89,4
_
C
WARNING
MAIN MENU
Pressing the WARNING button will return the display to the
WARNING screen and the RESET button.
A Warning needs to be reset by the operator by pressing the RESET
button twice.
The possible Warning messages are as follows;
AIREND DISCHARGE TEMP – This will occur if the Airend Discharge
(2ATT) exceeds 97% of the alarm limit, 228
_
F (109
_
C) and is not
adjustable.
CHANGE COOLANT FILTER – This warning will occur if the high side
pressure is 20 psig (1,4 bar) greater than the low side pressure of 1
DPS and the Injected Coolant temperature (2CTT) is greater than
120
_
F (49
_
C).
CHANGE INLET FILTER – This will occur if the Inlet Vacuum (1AVPT)
is greater than 0,7 psig (0,05 bar) and the machine is fully loaded (inlet
valve is completely open).
CHANGE SEPR ELEMENT – This warning will occur if the pressure
on the Separator (3APT) is 15 psig (1,0 bar) greater than the pressure
at the Package Discharge (4APT) and the machine is fully loaded.
ALARM
barg
7,5
barg
HIGH AIREND DISCH TEMP
109,4
_
C
STOPPED BY ALARM
MODE: MOD/ACS
PRESS RESET TWICE
STATUS
MAIN MENU
RESET
HIGH DISCHARGE PRESS – This can occur if the machine’s loading
function is being controlled by a host device such as a sequencer or an
ISC. This warning will occur when the package discharge pressure is
above the maximum offline pressure (rated pressure plus 3 psig (0,2
bar)) for more than 3 seconds. This warning will cause the compressor
to unload. The host device will not be able to load the compressor until
the package discharge pressure falls to the rated pressure of the
machine.
SENSOR FAILURE 4ATT – This will occur if the Package Discharge
Temperature Sensor (4ATT) is missing or broken.
ALARMS
When an Alarm occurs, the word ALARM will flash on the display
screen and appear in large letters as shown above. The display
message will indicate what caused the Alarm.
Pressing the STATUS button will display the STATUS screen. The
presence of the ALARM button indicates that an Alarm condition still
exists. Alarm Status is the list of machine operating conditions that
existed at the time of the Alarm.
–ALARM STATUS–
barg
7,5
barg
PACKAGE DISCH PRESSURE
7,5 barg
STOPPED BY ALARM
PACKAGE DISCHARGE TEMP
MODE: MOD/ACS
39,4
_
C
ALARM
MAIN MENU
The name and value of each of the items listed can be seen by
moving the list up and down using the arrow buttons. Pressing the
ALARM button will return the display to the Alarm screen and the
RESET button.
The Alarm needs to be reset by the operator by pressing the RESET
button twice. Any exceptions to this are explained in the alarm
descriptions.
The possible Alarm messages are as follows;
CHECK INLET CONTROL – This will occur if the machine is unloaded
and the inlet vacuum is less than 3 psig (0,2 bar).