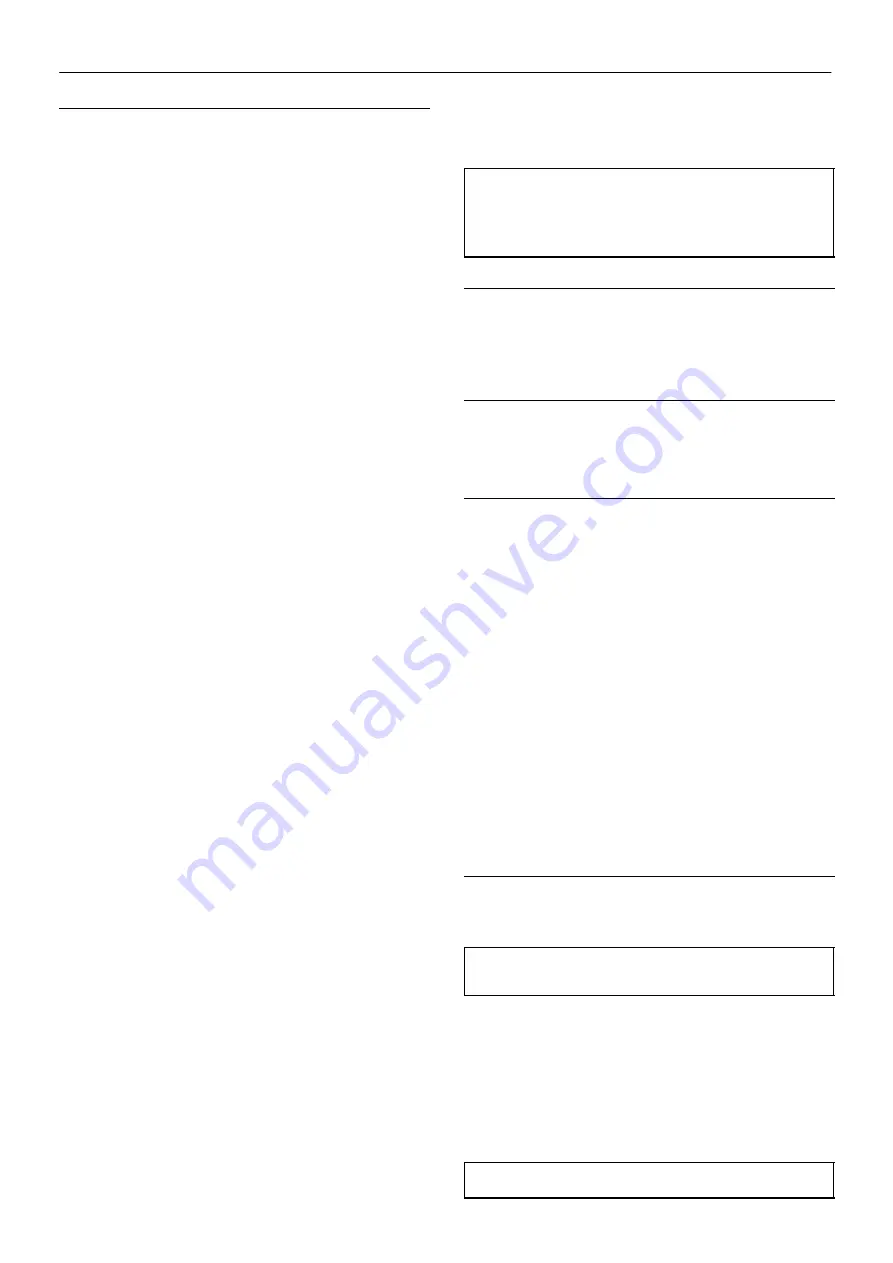
MAINTENANCE
34
M200–LV M250–LV
ROUTINE MAINTENANCE
This section refers to the various components which require
periodic maintenance and replacement.
The SERVICE/MAINTENANCE CHART indicates the various
components’ descriptions and the intervals when maintenance has to
take place. Coolant capacities, etc., can be found in the GENERAL
INFORMATION section of this manual.
Compressed air can be dangerous if incorrectly handled. Before
doing any work on the unit, ensure that all pressure is vented from the
system and that the machine cannot be started accidentally.
Ensure that maintenance personnel are adequately trained,
competent and have read the Maintenance Manuals.
Prior to attempting any maintenance work, ensure that:–
.
all air pressure is fully discharged and isolated from the system. If
the automatic blowdown valve is used for this purpose, then allow
enough time for it to complete the operation.
. the machine cannot be started accidentally or otherwise, by posting
warning signs and/or fitting appropriate anti–start devices.
.
all residual electrical power sources (mains and battery) are
isolated.
Prior to opening or removing panels or covers to work inside
a machine, ensure that:–
.
anyone entering the machine is aware of the reduced level of
protection and the additional hazards, including hot surfaces and
intermittently moving parts.
. the machine cannot be started accidentally or otherwise, by posting
warning signs and/or fitting appropriate anti–start devices.
Prior to attempting any maintenance work on a running
machine, ensure that:–
.
the work carried out is limited to only those tasks which require the
machine to run.
.
the work carried out with safety protection devices disabled or
removed is limited to only those tasks which require the machine to be
running with safety protection devices disabled or removed.
.
all hazards present are known (e.g. pressurised components,
electrically live components, removed panels, covers and guards,
extreme temperatures, inflow and outflow of air, intermittently moving
parts, safety valve discharge etc.).
.
appropriate personal protective equipment is worn.
.
loose clothing, jewellery, long hair etc. is made safe.
.
warning signs indicating that Maintenance Work is in Progress are
posted in a position that can be clearly seen.
Upon completion of maintenance tasks and prior to returning
the machine into service, ensure that:–
.
the machine is suitably tested.
.
all guards and safety protection devices are refitted.
.
all panels are replaced, canopy and doors closed.
.
hazardous materials are effectively contained and disposed of.
WARNING
Do not under any circumstances open any drain valve or remove
components from the compressor without first ensuring that the
compressor is FULLY SHUT– DOWN, power isolated and all air
pressure relieved from the system.
COOLANT LEVEL CHECKING PROCEDURE
The coolant level should be checked daily. Located on the side of
the separator is a coolant level sight tube/glass. Whilst the compressor
is running under load and the coolant is at normal operating
temperature, the coolant level should be between the middle and the
top of the sight glass.
COOLERS
Once a month, the coolers should be checked for coolant and dirt
accumulation on the exterior surfaces. Clean the coolers by directing
compressed air carrying, if possible, a non–flammable safety solvent
through the core of the cooler.
COOLANT FILTER CHANGE PROCEDURE
.
Loosen filter element with the correct tool.
.
Remove the element from the housing.
.
Place the old element in a sealed bag and dispose of in a safe way.
.
Clean the mating face of the housing.
.
Remove the new Ingersoll–Rand replacement element from its
protective package.
.
Apply a small amount of lubricant to the element seal.
.
Screw the new element down until the seal makes contact with the
housing, then hand tighten a further half turn.
Check the coolant level, refilling if necessary.
.
Start the compressor and check for leaks.
COOLANT CHANGE PROCEDURE
It is better to drain the coolant immediately after the compressor has
been operating as the liquid will drain more easily and any contaminant
will still be in suspension.
WARNING:
Extreme care should be taken when draining hot lubricant.
To enable the coolant to be drained, a valve is located under the
separator tank. This in turn feeds a flexible hose to enable direct
discharge to suitable containers for coolant removal.
Open the valve and completely drain the coolant into a suitable
container.
Close the valve and refill the compressor.
CAUTION – DO NOT MIX OILS WITH SSR ULTRA COOLANT.