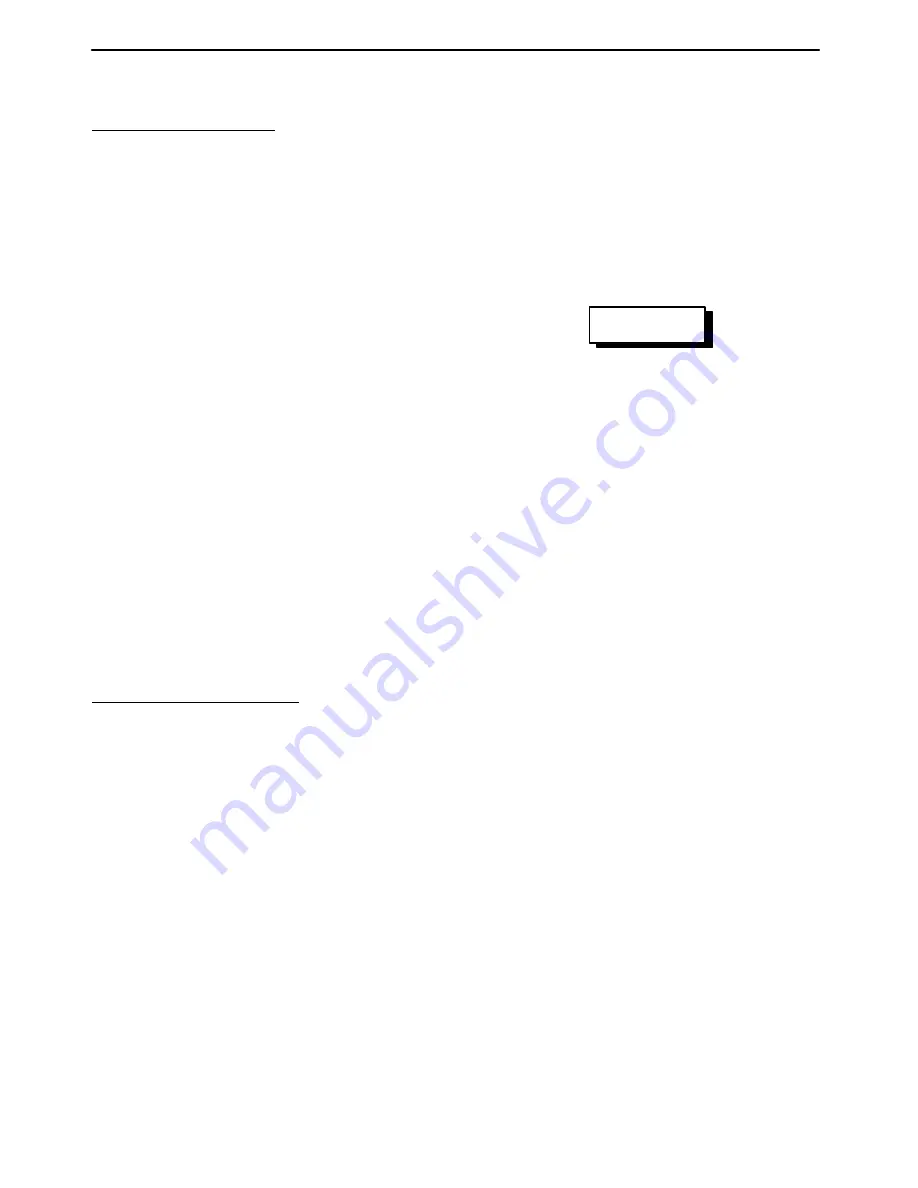
42
( )
Book 54722160 (8/02)
SECTION 7 -- LUBRICATION
GENERAL INFORMATION
Lubrication is an essential part of preventive mainte-
nance, affecting to a great extent the useful life of the
unit. Different lubricants are needed and some compo-
nents in the unit require more frequent lubrication than
others. Therefore, it is important that the instructions
regarding types of lubricants and the frequency of their
application be explicitly followed. Periodic lubrication
of the moving parts reduces to a minimum the possibil-
ity of mechanical failures.
The Preventive Maintenance Schedule shows those
items requiring regular service and the interval in
which they should be performed. A regular service
program should be developed to include all items and
fluids.
These intervals are based on average
operating conditions. In the event of extremely severe
(hot, cold, dusty or wet) operating conditions, more
frequent lubrication than specified may be necessary.
Details concerning lubrication of the running gear are
in Maintenance Section.
All filters and filter elements for air and compressor lu-
bricant must be obtained through Ingersoll--Rand to
assure the proper size and filtration for the compres-
sor.
COMPRESSOR OIL CHANGE
These units are normally furnished with an initial sup-
ply of oil sufficient to allow operation of the unit for ap-
proximately 6 months or 1000 hours, whichever
comes first. If a unit has been completely drained of all
oil, it must be refilled with new oil before it is placed in
operation. Refer to specifications in Lubrication Table.
NOTICE
Some oil types are incompatible when mixed and re-
sult in the formation of varnishes, shellacs, or lacquers
which may be insoluble. Such deposits can cause se-
rious troubles including clogging of the filters. Where
possible, do NOT mix oils of different types and avoid
mixing different brands. A type or brand change is best
made at the time of a complete oil drain and refill.
If the unit has been operated for the time/ hours men-
tioned above, it should be completely drained of oil. If
the unit has been operated under adverse conditions,
or after long periods in storage, an earlier change peri-
od may be necessary as oil deteriorates with time as
well as by operating conditions.
WARNING
High pressure air can cause severe injury or death
from hot oil and flying parts. Always relieve pres-
sure before removing caps, plugs, covers or other
parts from pressurized air system. Ensure the fol-
lowing conditions are met:
-- Discharge air pressure gauge reads zero (0).
-- No air discharging from an “open” manual blow-
down valve.
An oil change is good insurance against the accumula-
tion of dirt, sludge, or oxidized oil products.
Completely drain the receiver-- separator, piping, and
oil cooler. If the oil is drained immediately after the unit
has been run for some time, most of the sediment will
be in suspension and, therefore, will drain more readi-
ly. However, the fluid will be hot and care must be taken
to avoid contact with the skin or eyes.
After the unit has been completely drained of all old oil,
close the drain valve. Add oil in the specified quantity
at the filler plug. Tighten the filler plug and run the ma-
chine to circulate the oil. Check the oil level WHEN
RUNNING AT FULL LOAD. If not near the middle of
the sight tube, stop the unit and make corrections. DO
NOT OVERFILL.
NOTICE
Ingersoll--Rand provides compressor oil specifically
formulated for Portable Compressors and requires the
use of these fluids in order to obtain extended limited
airend warranty.