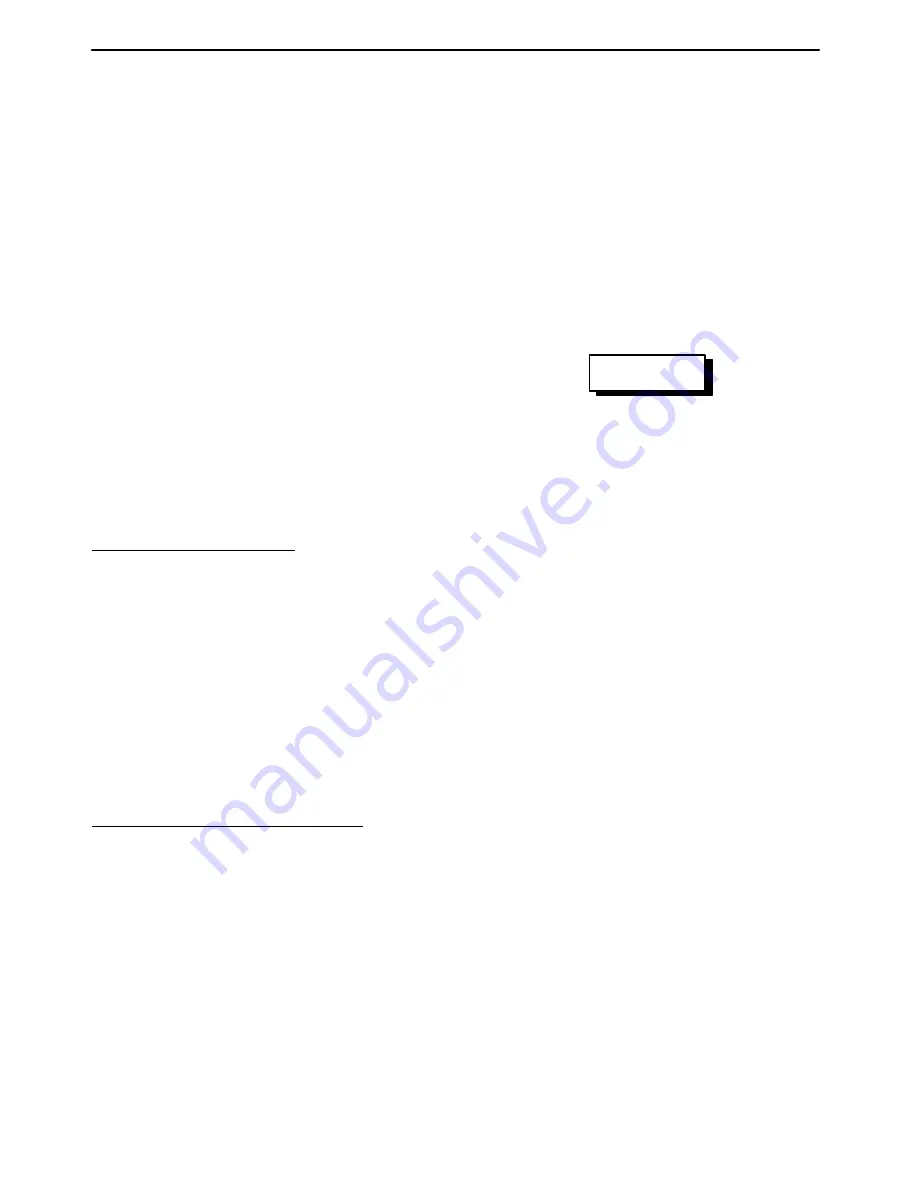
35
( )
Book 54722160 (8/02)
NOTICE
Piping systems operating at less than 150 psi
(1050 kPa) may use a special nylon tubing. The as-
sociated fittings are also of a special “push--in”
design. If so, features are as follows:
Pulling on the tubing will cause the inner sleeve to with-
draw and compress, thus tightening the connection.
The tubing can be withdrawn only while holding the
sleeve against the fitting. The tubing can be removed
and replaced numerous times without losing its seal-
ing ability.
To install the nylon tubing, make a mark (with tape or
grease pencil) approximately 7/8 inch from the end of
the tubing. Insert the tubing into the sleeve and “push--
in” past the first resistance to the bottom. The mark
should be approximately 1/16 inch from the sleeve, for
the 3/8 inch O.D. tubing; 1/8 inch for the 0.25 inch O.D.
tubing. This will ensure that the tubing is fully engaged
in the sealing mechanism.
COMPRESSOR OIL FILTERS
The compressor lubrication and cooling oil system in-
cludes dual spin--on, throw away type oil filters, each
with an internal bypass valve. With a clean, new filter
element, all of the oil flows through the full element
area, from the outside/inside. As each element be-
comes contaminated with dirt, a pressure differential is
created in the filter housing between the oil inlet and
outlet ports. As this differential approaches 25 psi (175
kPa), the bypass valve starts to open, thus permitting a
small quantity of oil to bypass the filter. As the contami-
nants continue to build up, more and more of the oil by-
passes the filter media itself.
This bypass does not provide any filtration but does al-
low a maximum flow of compressor lubricating and
cooling oil to preclude any possible damage from loss
of oil. Also the design of the filter prevents any wa-
shing--off of any dirt during oil bypassing.
NOTICE
The oil filter must be replaced every 500 hours of
operation. On new or overhauled units, replace
the element after the first 50 and 150 hours of oper-
ation; thereafter, service the oil filter every 500
hours.
To service the oil filters it will first be necessary to shut
the unit down. Wipe off any external dirt and oil from
the exterior of the filter to minimize any contamination
from entering the lubrication system. Proceed as fol-
lows:
WARNING
High pressure air can cause severe injury or death
from hot oil and flying parts. Always relieve
pressure before removing caps, plugs, covers or
other parts from pressurized air system.
1. Open the service air valve(s) to ensure that
system is relieved of all pressure. Close the valve(s).
2. Turn the spin--on filter element counterclockwise
to remove it from the filter housing. Inspect the filter
element and then discard.
Note:
If there is any indication of formation of
varnishes, shellacs or lacquers on the oil filter
element, it is a warning the compressor lubricating oil
has improper characteristics and should be
immediately changed.
3. Inspect the oil filter head to be sure the gasket was
removed with the oil filter element. Clean the gasket
seal area on the oil filter head.
Installing a new oil filter element when the old gasket
remains on the oil filter head will cause an oil leak and
can cause property damage.
4. Lubricate the new filter gasket with the same oil
being used in the machine.
5. Install new filter by turning element clockwise until
gasket makes initial contact. Tighten an additional 1/2
to 3/4 turn.
6. Start unit and allow to build up to rated pressure.
Check for leaks before placing unit back into service.