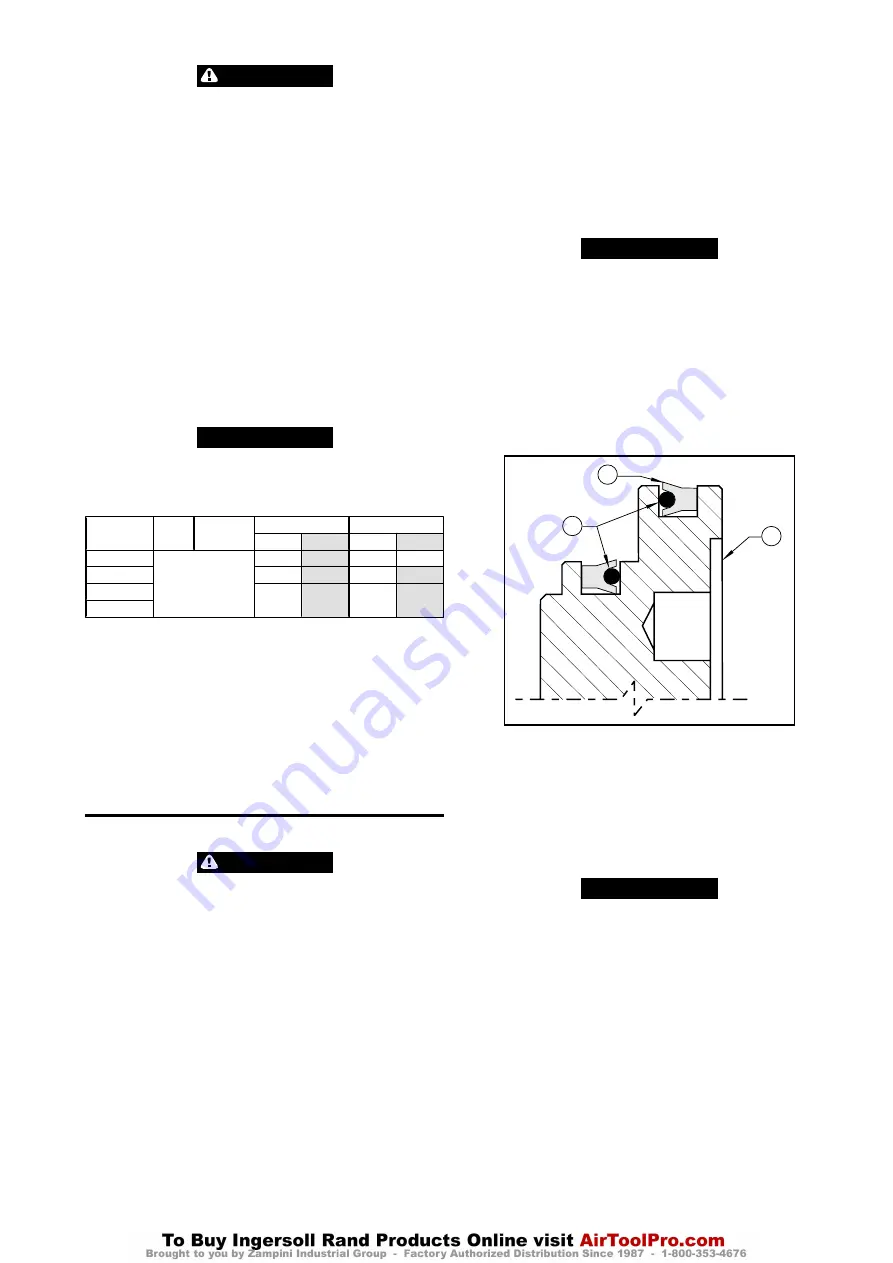
CAUTION
•
Bearings that are loose, worn or rotate in the housing must be replaced.
Failure to observe this precaution will result in additional component
damage.
•
Do not use trichloroethylene to clean parts.
•
If trolley suspension yoke bushings are loose or worn they must be
replaced. Failure to observe this precaution will result in additional
component damage.
n
Inspection
All disassembled parts should be inspected to determine their fitness for continued
use. Pay particular attention to the following:
1. Inspect all gears for worn, cracked, or broken teeth.
2. Inspect all bushings for wear, scoring, or galling.
3. Inspect shafts for ridges caused by wear. If ridges caused by wear are apparent
on shafts, replace the shaft.
4. Inspect all threaded items and replace those having damaged threads.
5. Measure the thickness of the friction discs (112). If the friction discs are less than
0.072 in. (1.83 mm) or if oil groove pattern is not clearly visible replace the friction
discs (112).
6. Check mufflers (173) and (176) for damage or excessive dirt.
7. Inspect trolley yoke bushings for wear, scoring, or galling. If wear exceeds discard
dimensions in Table 9 replace bushings.
8. Check bearings for ease of rotation and wear. Replace bearings if rotation is
rough or bearings are excessively worn.
9. Check the sprag clutch assembly for wear, flat spots on the sprags or damage. If
any of these conditions exist, replace parts.
10. Inspect sprag clutch wear area on brake hub (103) and on brake shaft (102) for
ridges or galling. If either condition exists replace parts.
NOTICE
•
If brake hub (103), sprag clutch (105) or brake shaft (102) require
replacement, it is recommended that all three parts be replaced at the same
time.
Table 3: Bushing Inspection Specifications
Hoist Model
Item
No.
Bushing
Part No.
Original Bore Size Discard Bore Size
in.
mm
in.
mm
HA3-025
Contact Factory
3.253
82.6
3.315
84.2
HA3-050
3.437
87.3
3.500
89
HA3-075
4.50
114.3
4.562
116
HA3-100
n
Repair
Actual repairs are limited to the removal of small burrs and other minor surface
imperfections from gears and shafts. Use a fine stone or emery cloth for this work.
1. Worn or damaged parts must be replaced. Refer to the applicable parts listing
for specific replacement parts information.
2. Inspect all remaining parts for evidence of damage. Replace or repair any part
which is in questionable condition. The cost of the part is often minor in
comparison with the cost of redoing the job.
3. Smooth out all nicks, burrs, or galled spots on shafts, bores, pins, or bushings.
4. Examine all gear teeth carefully, and remove nicks or burrs.
5. Polish the edges of all shaft shoulders to remove small nicks which may have
been caused during handling.
6. Remove all nicks and burrs caused by lockwashers.
7. Replace all seals, 'O' rings and gaskets.
n
Assembly Instructions
CAUTION
•
Use extreme care when performing any maintenance on hoist. Hoist weight
may exceed 7,400 lbs (3357 kg) use appropriately rated equipment for
moving.
Refer to Product Parts Information Manual for assembly drawings and parts lists.
n
Powerhead Assembly
Refer to Dwg. MHP2343.
1. Place motor end frame in a vertical position with motor side down, for
procedures 2 through 14.
2. Lubricate and install ‘O’ rings (163) and (164) and bearings (157) to idler sheave
(156).
3. Install idler sheave assembly (156) in motor end frame (152) and install a short
length of chain. Refer to ‘Load Chain Weld Placement’ and Dwg. MHP0042 in
“MAINTENANCE” section ‘’ on page 5.
4. If vertical stripper (160) was removed during disassembly, install and secure
using capscrews (167) to center frame (153).
5. Install pins (165) if removed during disassembly.
6. Align pins (165) in motor end frame (152) with center frame (153) and carefully
lower center frame onto motor end frame using appropriately rated equipment.
7. Install capscrews (161) and torque to approximately 909 to 1030 ft lbs (1299 to
1471 Nm).
8. Install wear pads (158) with capscrews (166) in reduction gear end frame (154)
and center frame (153). Apply a small amount of Loctite® 242 to threads.
9. Lubricate and install ‘O’ rings (163), (164) and bearings (157) on both sides of
drive sheave (155).
10. Install dowel pins (165) and (168) if removed during disassembly.
11. Install drive sheave assembly (155) and lead stripper (159) together. Align dowel
pins (168) in lead stripper with holes in center frame (153).
12. Install a short length of chain around drive sheave (155) and lead stripper (159).
Refer to ‘Load Chain Weld Placement’ and Dwg. MHP0042 in “MAINTENANCE”
13. Install reduction gear end frame (154) onto center frame (153) being careful to
align dowel pins (165) and (168).
14. Install capscrews (161) and (152) in reduction gear frame and torque to
approximately 909 to 1030 ft lbs (1299 to 1471 Nm).
15. Using holes on both sides frames, rotate powerhead assembly so reduction gear
frame (154) side is down for easier installation of brake.
16. Lubricate and install ‘O’ ring (123). Align capscrew holes and position brake
housing (110) on motor end frame (152).
NOTICE
•
If hub (103) and sprag clutch (105) were removed from brake shaft (102) be
sure to install this assembly so teeth of hub (103) are pointing toward motor
end frame (152).
17. Clean brake shaft assembly and inspect parts for wear before assembling brake.
18. Install on brake shaft (102), hub assembly (103) and thrust washer (107) secure
with retainer ring (108).
19. Inspect and install drive discs (111) and friction discs (112) on hub (103). Alternate
discs, starting with friction disc (112) followed by a drive disc (111).
20. Lubricate and install seals (113) and (114) in brake piston (104) grooves so seal
lips face each other. Do not overstretch seals during this procedure. Refer to
21. Install brake shaft assembly (102) and piston assembly (104) in brake housing
(110).
22. Install brake piston assembly in brake housing so stepped side enters first. Gently
tap into position using a soft mallet until seated. Refer to Dwg. MHP0139, A. Seal
Lip; B. Seal; C. Brake Piston.
Seal Lip
Seal
Brake
Piston
A
B
C
(Dwg. MHP0139)
23. Install springs (117), ‘O’ ring (116) and reaction ring (101) on brake shaft (102).
24. Install motor adapter (53) to brake housing (110) and secure with capscrews
(109). Torque to approximately 106 to 121 ft lbs (151 to 173 Nm).
25. Using side holes in frames of hoist rotate hoist assembly vertically so motor end
frame (152) is down. Place blocks along either side of motor end frame (152) to
protect brake shaft (102) from damage.
26. Install drive shaft (151) and bushing (169) through reduction gear end frame side
so it engages with brake shaft. Use care when installing so no damage will occur
to either shaft.
27. Rotate drive shaft (151) clockwise and check for brake shaft (102) to rotate. If
brake shaft does not move, gently rotate drive shaft (151) until teeth engage
brake shaft. Continue this step until brake shaft (102) rotates with drive shaft.
NOTICE
•
Use care when installing reduction gear assembly (200) to powerhead
assembly. Damage or distortion to drive shaft (151) may occur if not
properly supported while installing reduction gear assembly.
28. Install reduction gear assembly (200) to reduction gear end frame (154) and
secure with capscrews (202) and lockwashers (702), apply a small amount of
Loctite® 242 to threads of capscrews. Torque to 80 to 90 ft lbs (114 to 129 Nm).
29. Using holes on both sides of frames, rotate powerhead assembly horizontally,
providing blocks on either side for support.
30. Install motor assembly (700) to motor end frame (152) and secure with capscrews
(703) and lockwashers (702), apply a small amount of Loctite® 242 to threads of
capscrews. Torque to 80 to 90 ft lbs (114 to 129 Nm).
31. After chain has been reeved, install cotter pin (170) in lead stripper (159) and
secure with retainer ring (171). Refer to Dwg. MHP2341 on page 27.
n
Hoist Motor Assembly
Refer to Dwg. MHP2348.
1. Assemble pilot control valve assembly (621) and manifold (750) to rotary valve
housing (739) using four capscrews (747) and lockwashers (749). Install two
capscrews (747) and lockwashers (749) that attach exhaust flange (744) to
throttle valve housing.
Form MHD56243 Edition 4
9
Содержание HA3-075
Страница 12: ...R www ingersollrandproducts com...