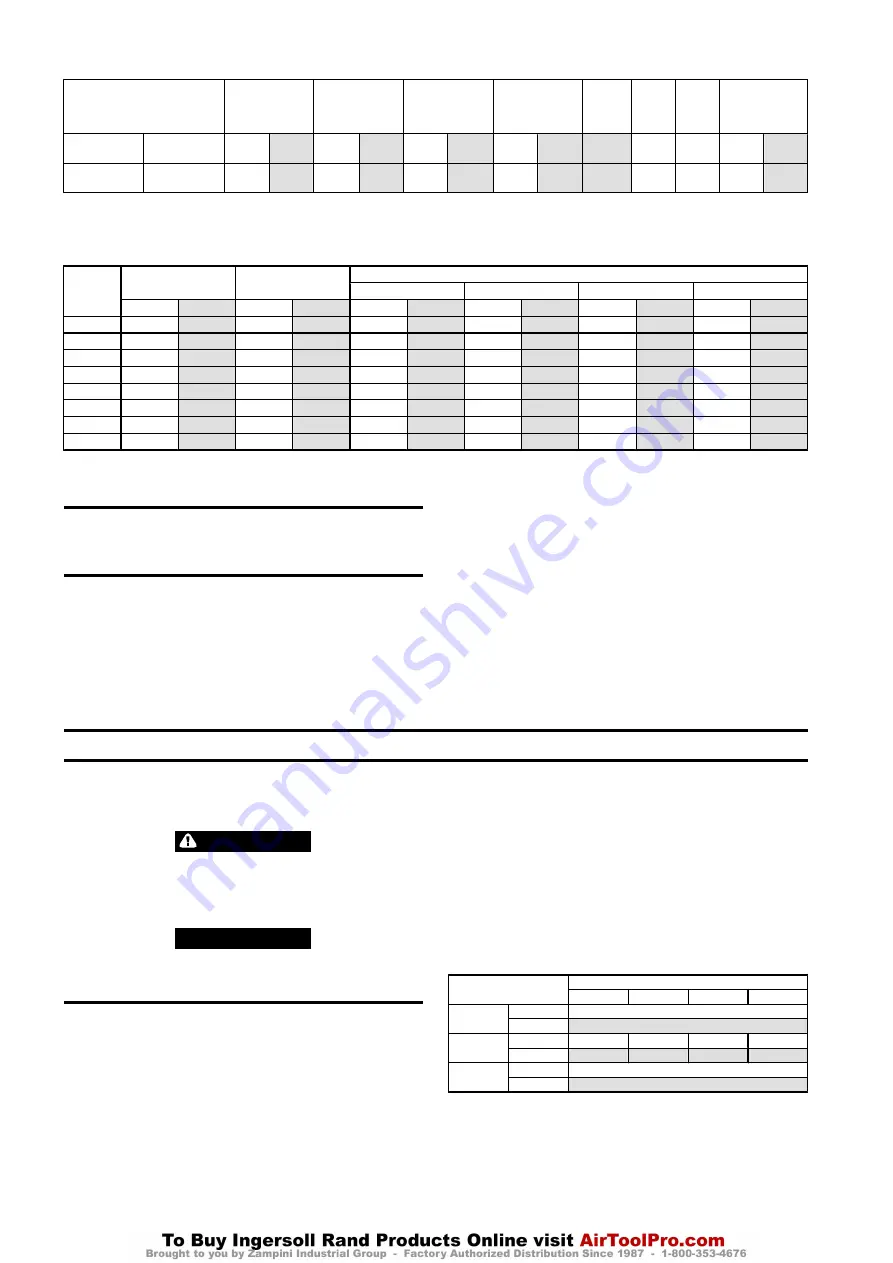
Table 2: General Specifications
Air
System
Air Motor Pipe
Inlet Size
Minimum Air
System
Hose Size (inside
diameter)
Drum
Barrel
Diameter
Drum
Flange Diameter
Recomm-
ended
Wire Rope
Size
Sound
Pressure
Level
(2, 3)
Sound
Power
Level
(2)
Maximum
Foundation Anchor
Shear Force at One
Capscrew (4)
Rated Operating
Pressure
Air Consumption
(at rated load)
inch
mm
inch
mm
inch
mm
inch
mm
mm
dBA
dBA
lbs
N
90 psig (6.3 bar)
62 scfm (1.75
cu.m/min)
1.25 NPT
32
0.75
19
10.75
273
19
483
10
85
96
75
334
1. Performance based on 6.3 bar/630 kPa (90 psig) operating pressure.
2. Sound measurements have been made in accordance with ISO 11201, ISO 3744-3746 and ISO 4871 test specifications for sound from pneumatic equipment. Readings shown
are based on the average noise level of each winch configuration, proportionate to the utilized time in a regular cycle.
3. Lpc (Peak Sound Pressure) does not exceed 130 dB.
4. Occurs when wire rope take-off from drum equals zero degree angle of inclination. Values based on wire rope at third layer and rated line pull.
Layer
Line Speed @ 150 kg
(330 lb) Load
Minimum Load for
Emergency Lowering
Wire Rope Storage Capacity **
8 inch (203 mm) Drum 12 inch (305 mm) Drum 16 inch (406 mm) Drum 24 inch (610 mm) Drum
fpm
mpm
lb
kg
ft
m
ft
m
ft
m
ft
m
1
82
25
200
91
56
17
86
26
116
35
175
53
2
85
26
187
85
116
35
178
54
239
73
361
110
3
87
26.5
176
80
180
55
275
84
370
113
560
717
4
89
27
166
75
248
76
378
115
509
155
770
235
5
91
27.7
158
72
319
97
487
148
655
200
991
302
6
93
28.3
150
68
395
120
602
183
810
247
1,225
373
7
94
28.6
140
64
474
144
723
220
972
296
1,470
448
8 (1)
95
29
136
62
556
169
849
259
1,142
348
1,727
526
** Wire rope storage capacity based on DNV and NMD standards of 2.5 times wire rope diameter below drum flange. Wire rope storage capacities listed may vary from figures
stated elsewhere.
1. Full drum at rated operating pressure and line speed.
n
Capacity Information
FA150KGi Man Rider
™ winches are designed for lifting with a 5:1 minimum safety
factor at rated load.
n
Traceability
Load bearing parts are documented to provide traceability. Documentation includes
chemical and physical properties of raw material, heat treating, hardening, tensile
and charpy tests as required for the part.
Units with
M1
,
M2
or
M3
in the model code have traceable load bearing components.
M1
– Material Traceability certificates according to EN 10204 (Ex DIN 50049) 2.2 on
load bearing parts. Conformity documents affirm (by the manufacturer) that parts are
in compliance with requirements of the order, based on non-specific inspection and
testing (i.e. results are typical material properties for these parts).
M2
– Material Traceability certificates according to EN 10204 (Ex DIN 50049) 3.1b on
load bearing parts. Conformity documents affirm (by a department independent of
the manufacturing department) that actual parts are in compliance with requirements
of the order, based on specific inspection and testing (i.e. results are actual material
properties for these parts).
M3
– Material Traceability certificates according to EN 10204 (Ex DIN 50049) 3.1b on
load bearing parts. Conformity documents affirm (by a department independent of
the manufacturing department) that the actual parts used in the product are in
compliance with the order, based on specific inspection and testing (i.e. results are
actual material properties for these parts in a finished, as delivered condition).
Components with part numbers ending in CH are charpy parts for use under extreme
cold conditions. Traceability requirements must be stated when reordering these parts
for continued certification.
INSTALLATION
Winch gearbox and disc brake are supplied fully lubricated from factory. Check oil
levels and adjust as necessary before operating winch.
Refer to “LUBRICATION” section on page 9 for recommended oils. Prior to
installing winch, carefully inspect it for possible shipping damage.
CAUTION
• Owners and users are advised to examine specific, local or other regulations,
including American Society of Mechanical Engineers (ASME) and/or OSHA
Regulations which may apply to a particular type of use of this product before
installing or putting product to use.
NOTICE
• Prior to installation refer to Product Safety Information Manual for all
sections of installation.
n
Mounting
Care must be taken when moving, positioning or mounting winch. Winch has lifting
lugs bolted to both uprights to assist in moving the unit. Attach hooks or a suitable
sling to these lugs when moving winch. Refer to “SPECIFICATIONS” section
on page 3 to determine winch weight.
Mount winch so drum axis is horizontal and motor control valve pad is not more than
15 degrees off top vertical center. If winch is to be mounted in an inverted position,
the motor case must be rotated to position control valve pad at the top and adequate
clearance must be provided for control valve operation. Position winch to provide
unrestricted access to winch control valve. Do not mount winch in a vertical position,
with motor up or down. Reduction gear box lubrication is not designed for this type
of installation.
1. Winch mounting surface must be flat and of sufficient strength to handle rated
load plus the weight of the winch and attached equipment. An inadequate
foundation may cause distortion or twisting of the winch uprights and side rails
resulting in winch damage.
2. Make sure mounting surface is flat to within 1/16 inch (1.6 mm). Shim if
necessary.
3. Mounting bolts must be 5/8 inch NC (16 mm) Grade 8 or better. Use self-locking
nuts or nuts with lockwashers. Refer to Table 3 ‘Mounting Bolt Hole
4. Tighten mounting bolts evenly. Refer to “Torque Chart” in Product Maintenance
Information Manual for proper tightening values.
5. Maintain a fleet angle between lead sheave and winch of no more than 1-1/2
degrees. The lead sheave must be on a center line with the drum and, for every
inch (25 mm) of drum length, be at least 1.6 ft (0.5 m) from the drum. Refer to
Product Safety Information Manual.
Refer to Dwg. MHP2288 on page 11,
A.
Drum.
Table 3: Mounting Bolt Hole Dimensions
Dimension
Drum Length (inches)
8
12
16
24
“A”
inch
20
mm
508
“B”
inch
7
9
7.5 *
10 *
mm
178
229
190 *
254 *
“C”
inch
0.69
mm
18
* 4 mounting bolt holes in each side.
4
Form MHD56314 Edition 4
Содержание FORCE 5i Man Rider FA Series
Страница 14: ...SERVICE NOTES 14 Form MHD56314 Edition 4...
Страница 16: ...www ingersollrandproducts com...