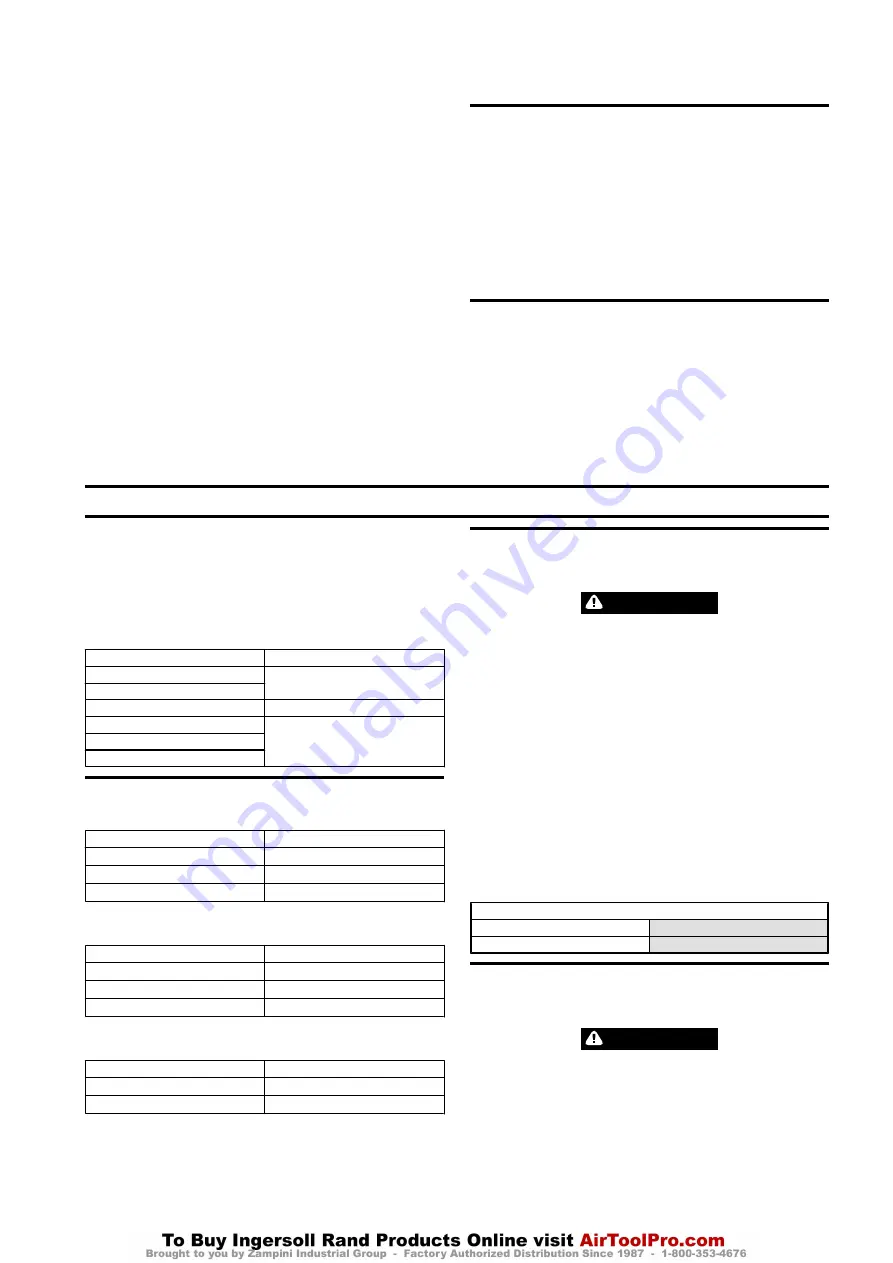
2.
Rigging:
-
Correct size wire rope is being used. 10 mm minimum
-
Wire rope take-off angle is within design limits
3.
Visual Integrity:
-
All Components - Inspect for wear, damage, distortion, deformation and
cleanliness. If external evidence indicates damage, contact
Ingersoll Rand
Service Technician to disassemble as required to conduct a detailed
inspection
-
No part of the winch has been welded onto
-
Fasteners - Check external retainer rings, split pins, capscrews, nuts and other
fasteners on winch, including mounting bolts
-
Drum and Sheaves - Check for cracks, wear or damage
-
Press Roller - Inspect rollers for wear and grooves. Ensure rollers freely rotate.
Replace rollers if worn or grooved. Replace bearings if rotation is rough or
stiff
-
Slack Line Detector - Inspect rollers for wear and grooves. Ensure rollers freely
rotate
-
Ensure drum guard is capable of adequately guarding personnel
-
No modifications have been performed on the winch
-
Check motor, gearbox and disc brake for oil leakage
4.
Labeling / Marking:
-
Data (name) plate is attached and legible
-
Warning tags and labels are attached, legible and in correct places on winch
5.
Wire Rope Spooling:
-
A minimum of 3 dead wraps remain on drum in fully paid-out position
-
Proper freeboard is maintained at full haul-in position (minimum 1 inch (26
mm) for 10 mm wire rope)
-
Wire rope is properly lubricated
6.
Operational Checks:
-
Manual Band Brake: Connect auxiliary air supply to emergency brake release
system, disengage manual band brake, lift load a short distance, and depress
emergency brake release valve. Load should begin to drift downward. Apply
manual band brake with emergency brake release valve still depressed. Load
should stop
-
Limit Switches - Operate winch in the haul-in direction until limit switch
engages. Ensure winch stops running in haul-in direction, and operate in
payout. Operate winch in payout direction until limit switch engages. Ensure
winch stops operating in payout direction, and will operate in haul-in
direction
-
Line Speed - Raise and lower (5 ft. min. distance) a 485 lbs (220 kg) load at
first layer to verify line speed. Line speed to be 60 fpm (18 m/min). Line
speed to be recorded after warm-up
n
Winches Not in Regular Use
1. Equipment which has been idle for a period of one month or more, but less than
six months, shall be given an inspection conforming to the requirements of
‘Frequent Inspection’ on page 8 before being placed in service.
2. Equipment which has been idle for a period of over six months shall be given a
complete inspection conforming with requirements of ‘Periodic Inspection’ in
maintenance manual before being placed in service. Refer to Product Maintenance
Information Manual.
3. Standby equipment shall be inspected at least semiannually in accordance with
requirements of ‘Frequent Inspection’ on page 8. In abnormal operating
conditions equipment should be inspected at shorter intervals.
4. All oils must be drained and replaced with new, and all grease cavities shall be
packed to the prescribed limit. Refer to “LUBRICATION” section on page 9.
Product must be operated for at least 15 seconds in both directions with well
lubricated, dry air.
n
Storing The Winch
1. Always store the winch in a no load condition.
2. Wipe off all dirt and water.
3. Oil the wire rope.
4. Place in a dry location.
5. Before returning winch to service, follow instructions for ‘Winches Not In Regular
Use’ in the “INSPECTION” section on page 8.
6.
Mufflers and Breathers.
All mufflers and breathers must be removed and replaced
with threaded plugs to prevent dust and moisture from entering motor and valve
assemblies.
7.
Rotary Limit Switch.
Product equipped with a rotary limit switch must be stored
with the limit switch not activated.
LUBRICATION
To ensure continued satisfactory operation of winch, all points requiring lubrication
must be serviced with correct lubricant at proper time interval as indicated for each
assembly.
Refer to ‘Maintenance Interval’ chart in Product Maintenance Information Manual for
recommended lubrication intervals. Use only those lubricants recommended. Other
lubricants may affect product performance. Approval for use of other lubricants must
be obtained from your
Ingersoll Rand
distributor. Failure to observe this precaution
may result in damage to winch and/or its associated components.
Table 5: Lubrication Intervals
Component
Interval
Check Air Line Lubricator
Daily
Check Motor Oil Level
Check Reduction and Disc Brake Oil
3 Months
Change Motor Oil
1 Year or 1,000 Hours
of Product Operation
Change Gearbox Oil
Change Disc Brake Oil
n
Recommended Lubricants
Table 6: Reduction Gear and Disc Brake Recommended Lubricant Grade
Temperature
Grade Type
Below 32
°
F (0
°
C)
2 EP (ISO VG 68)
32
°
to 80
°
F (0
°
to 27
°
C)
3 EP (ISO VG 100) *
Above 80
°
F (27
°
C)
4 EP (ISO VG 150)
* Units are shipped from factory with 3 EP (ISO VG 100) lubricant.
Table 7: Air Motor Recommended Lubricant Grade
Temperature
Grade Type
Below 32
°
F (0
°
C)
ISO VG 32 (SAE 10W)
32
°
to 80
°
F (0
°
to 27
°
C)
ISO VG 68 (SAE 20W) *
Above 80
°
F (27
°
C)
ISO VG 100 (SAE 30W)
* Units are shipped from factory with ISO VG 68 (SAE 20W) lubricant.
Table 8: Recommended Grease Grade
Temperature
Grade Type
-20
°
to 50
°
F (-30
°
to 10
°
C)
EP 1 multipurpose lithium based grease
30
°
to 120
°
F (-1
°
to 49
°
C)
EP 2 multipurpose lithium based grease
n
Motor
Refer to Dwg. MHP2271 on page 11,
A.
Fill/Breather Plug;
B.
Motor Case;
C.
Level
Plug Position;
D.
Drain Plug Position.
CAUTION
• Do not use synthetic or detergent lubricants in air motor. Synthetic lubricants
will result in oil blowing by piston rings.
The oil level in the motor should be checked daily or at the start of each shift after
accumulated water has been drained off. To drain, locate and remove oil level, pipe
plug (121) in bottom of motor housing (118). Any fluid drained should be disposed
of in an environmentally safe manner.
Correct lubrication is one of the most important factors in maintaining efficient winch
operation. The motor is splash lubricated by the oil in the motor housing and has no
other means of lubrication. It is therefore important to use only high quality, Extreme
Pressure (EP) rust and oxidation inhibiting gear oils or non-detergent motor oils to
ensure maximum performance and minimum downtime for repairs.
Add oil through filler opening until oil flows from level plug hole. Add oil slowly to
prevent spilling. Refer to Table 9 ‘Motor Oil Capacity’ on page 9. Allow oil to settle
before topping off.
When motors are operated in temperatures below freezing, wait long enough at end
of shift for water to separate from oil but not long enough for it to freeze. Failure to
drain the water when the winch is to remain idle for a protracted period at low
temperatures may result in the oil splasher freezing fast. Drain the water then refill
to the level plug. If desired, all the oil may be drained at the end of the shift and
the motor refilled with new oil.
Table 9: Motor Oil Capacity
Capacity
pint
litres
0.5
0.236
n
Reduction Gear and Disc Brake Lubrication
Refer to Dwg. MHP2297 on page 12,
A.
Fill Plug Position;
B.
Inboard Upright;
C.
Drain Plug;
D.
Drum;
E.
Reduction Gear Assembly.
CAUTION
• Do not over fill. Excess oil will reduce operating efficiency and increase oil
temperature.
• Only use synthetic lubricant in reduction gear and disc brake.
The reduction gear and disc brake are filled with oil from the factory. Check oil level
before initial winch operation.
Form MHD56314 Edition 4
9
Содержание FORCE 5i Man Rider FA Series
Страница 14: ...SERVICE NOTES 14 Form MHD56314 Edition 4...
Страница 16: ...www ingersollrandproducts com...