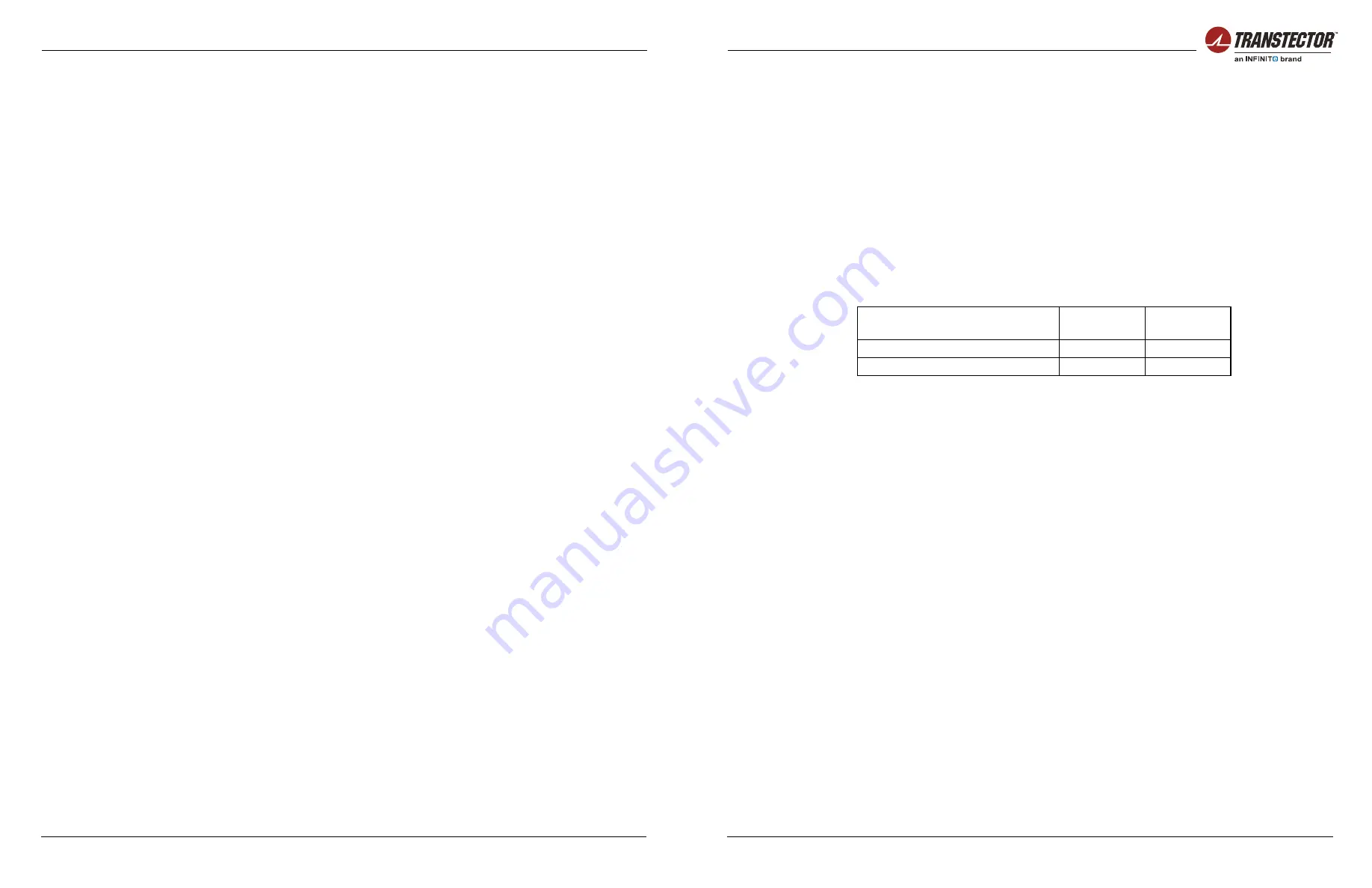
Installation Manual
| DCIPS2B-S-00-B11 Power Supply System
42
43
+1 (208) 635-6400 | www.transtector.com
+1 (208) 635-6400 | www.transtector.com
5.4 Commissioning procedure
1. Remove the covers and check that all connections are made according to the installation
drawing. Verify that all connections are properly tightened with sufficient torque.
2. Ensure that load and battery MCB breakers are set to OFF position - ensuring the load
and battery strings are connected.
3.
Ensure that all rectifier modules are removed. If not, remove each one in turn starting
from the rightmost position.
4.
If the rectifier subrack has dip switches for addressing, verify that the dip switches are
set correctly.
5. Check the battery polarity with the multimeter (3½ Digit, 0·1% dc). Place the positive
lead of the meter to the positive busbar and the negative lead to the battery breaker.
The meter must now show a positive voltage. If the voltage is negative, change over the
connection of the blue and black battery cables to the batteries.
6. Turn on the AC mains voltage.
7. Measure the AC voltage on the AC terminal block between phases and neutral. The
correct value is approximately 120V or 230V as appropriate. If the value is different,
check the AC connection.
8.
Plug in all rectifier modules, starting from the leftmost position. Make sure to fasten the
rectifiers again. The rectifiers will turn on automatically.
9. Set all load breakers into the “1” (ON) position.
10. The green LED on the controller should blink for approximately 20 sec.
11.
The output voltage will increase slowly to U1 (float charge voltage).
12. Turn the battery breaker(s) to the “1” (ON) position.
13. Set the battery current limit according to the battery manufacturers requirements.
14. If any alarms are present, they should be reset in accordance with the procedure for the
ACX Advanced controller.
15. The system should now be without alarms.
16. Attach all the system covers in their correct places.
17. Check that all changes to drawings, if any, have been completed.
18. Clean the site.
19. Fill in the commissioning record (see end of chapter).
5.5 Test of output voltage
5.5.1 Float charge (U1)
Ensure that the controller is operating.
Connect a load, approx. 50% of total capacity, to the system.
Check the voltage according to the battery manufacturer’s requirements. If the batteries
require a different float charging voltage, adjust the output voltage from the controller. (See
the section for the appropriate controller)
If no change is required, use the following values:
Battery type
Float charge Boost
charge
Open lead-acid batteries
2.23 V/Cell
2.33 V/Cell
Valve regulated lead-acid batteries 2.27 V/Cell
-
Table 5-1 Float/Boost Charge Voltages
5.5.2 Adjustment of Float Charge, U1
Unless otherwise ordered the default output voltage is factory pre-set to 53.5V. The total
voltage has to be in accordance to the number of battery cells.
Please verify number of cells and the battery manufacturers requirement.
Adjust the output voltage from the control unit as necessary.
5.5.3 Boost charging (U2) (if applicable)
Open lead-acid batteries.
Automatic boost charging - calculation based on the time the battery voltage has been below
certain levels. Automatic activating of boost charging for this calculated time multiplied by
a (boost) factor.
Activate boost charging from the “Set/select U1-U4” menu in the controller.
Return to float charge manually by selecting “U1”, or automatically after a pre-set time.
VRLA batteries.
Most of the manufactures of valve regulated lead acid batteries
do not recommend
boost
charging. If this type of battery is used, the boost function should be disabled.