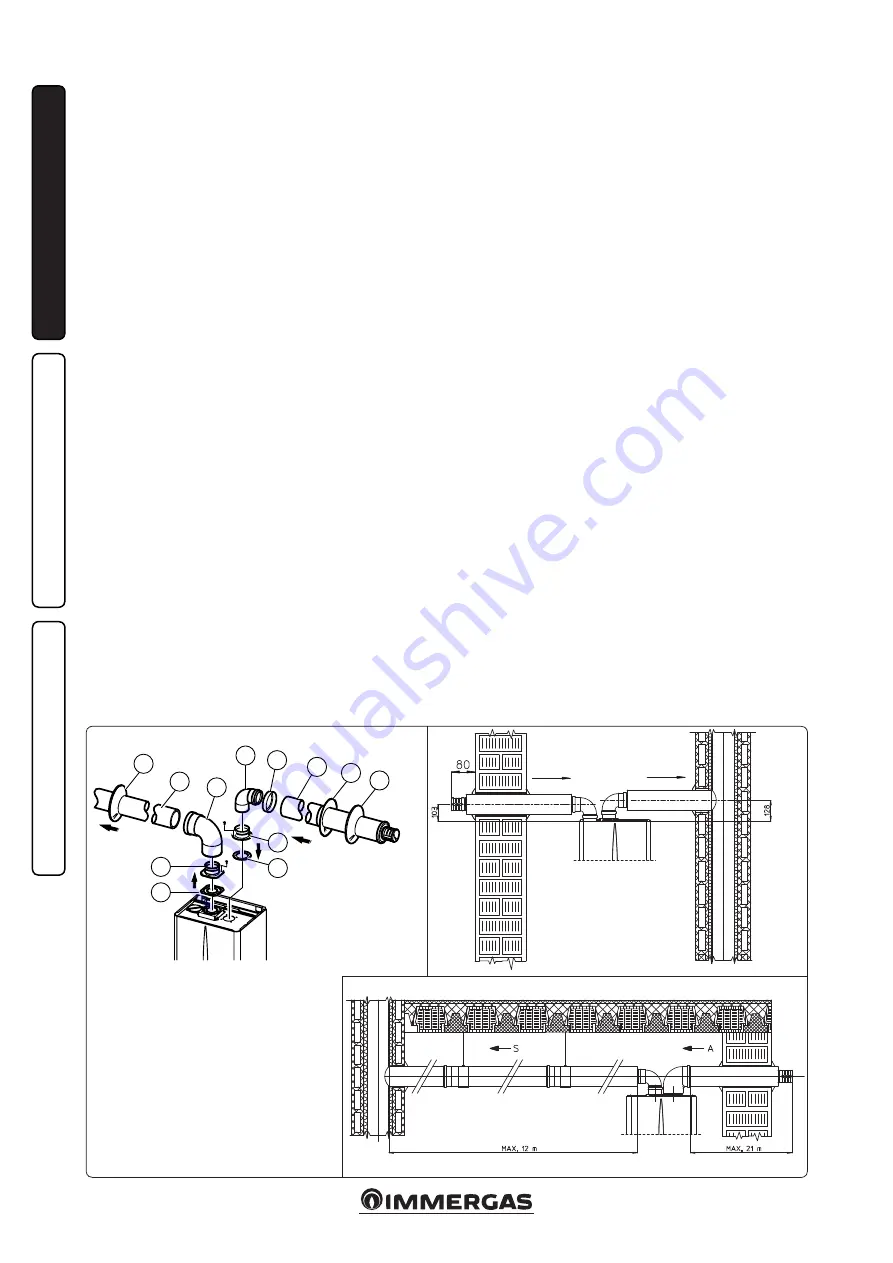
16
C82
1-27
1-28
C82
C82
1-26
5
4
1
3
2
5
6
7
8
8
10
11
9
S
A
INS
TALLER
US
ER
MAINTEN
AN
CE TECHNI
CI
AN
Insulated separator kit Ø 80/80.
Kit assembly
(Fig. 1-26): install flange (4) on the central hole of
the boiler, fitting gasket (1) and tighten with the
flat-tipped hex screws included in the kit. Remo-
ve the flat flange present in the lateral hole with
respect to the central one (according to needs)
and replace it with the flange (3), positioning
the gasket (2) already present in the boiler and
tighten using the supplied self-threading screws.
Insert and slide cap (6) onto bend (5) from the
male side (smooth), and join bends (5) with the
male side (smooth) in the female side of flange
(3). Fit bend (11) with the male side (smooth)
into the female side of flange (4). Fit the male
end (smooth) of the intake terminal (7) up to the
stop on the female end of the bend (5), making
sure you have already inserted the wall sealing
plates (8 and 9) that ensure correct installation
between pipe and wall, then fix the closing cap
(6) on the terminal (7). Join the exhaust pipe (10)
with the male side (smooth) in the female side
of the bend (11) to the end stop, ensuring that
the wall sealing plate (8) is already inserted for
correct installation between the pipe and flue.
• Coupling extension pipes and elbows. To snap-
fit extensions with other elements of the flue gas
extraction elements, operate as follows: engage
the concentric pipe or elbow with the male
side (smooth) on the female section (with lip
seal) up to the stop on the previously installed
element. This will ensure sealing and joining
of the elements correctly.
• Insulation of separator terminal kit. Whenever
there are flue gas condensate problems in the
exhaust pipes or on the external surface of the
intake pipes, on request Immergas supplies
insulated intake-exhaust pipes. Insulation
may be necessary on the exhaust pipe, due to
excessive loss of temperature of the flue gas on
their route. Insulation may be necessary on the
intake pipe as the air entering (if very cold)
may cause the outside of the pipe to fall below
the dew point of the environmental air. The
figures (Fig. 1-27 and 1-28) illustrate different
applications of insulated pipes.
Insulated pipes are formed of a Ø 80 internal
concentric pipe and a Ø 125 external pipe with
static air space. It is not technically possible
to start with both Ø 80 elbows insulated, as
clearances will not allow it. However starting
with an insulated elbow is possible by choosing
either the intake or exhaust pipe. When star-
ting with the insulated intake bend it must be
engaged on its flange until it is taken up to stop
on the flue gas exhaust flange, a situation that
takes the two intake flue gas exhaust outlets to
the same height.
• Temperature loss in insulated flue ducting.
To prevent problems of flue gas condensate in
the exhaust pipe Ø 80, due to flue gas cooling
through the wall,
the length of the pipe must be
limited to 12 m.
The figure (Fig. 1-28) illustrates
a typical insulation application in which the
intake pipe is short and the exhaust pipe is very
long (over 5 m). The entire intake pipe is in-
sulated to prevent moist air in the place where
the boiler is installed, in contact with the pipe
cooled by air entering from the outside. The
entire exhaust pipe, except the elbow leaving
the splitter is insulated to reduce heat loss from
the pipe, thus preventing the formation of flue
gas condensate.
N.B.:
When installing the insulated pipes, a
section clamp with pin must be installed every
2 metres.
• Configuration type B, open chamber and fan
assisted.
When using type B installation configuration
indoors, it is compulsory to install the relative up-
per cover kit along with the flue gas discharge kit.
The air intake comes directly from the area where
the boiler is installed and from the flue exhaust
in each single flue or directly from outdoors.
The boiler in this configuration, following the
assembly instructions stated in the par. 1.8 is
classified as type B.
With this configuration:
- air intake takes place directly from the envi-
ronment in which the boiler is installed and
only functions in permanently ventilated
rooms.
- The flue exhaust must be connected to its own
individual flue or channelled directly into the
external atmosphere.
- Type B open chamber boilers must not be
installed in places where commercial, artisan
or industrial activities take place, which use
products that may develop volatile vapours
or substances (e.g. acid vapours, glues, paints,
solvents, combustibles, etc.), as well as dusts
(e.g. dust deriving from the working of wood,
coal fines, cement, etc.), which may be dama-
ging for the components of the appliance and
jeopardise functioning.
On installation indoors in type B configuration
it is mandatory to install the relevant top cover
kit along with the flue gas exhaust kit.
The technical regulations in force must be
respected.
The kit includes:
N°1 - Exhaust gasket (1)
N°1 - Flange seal (2)
N°1 - Female intake flange (3)
N°1 - Female exhaust flange (4)
N°1 - Bend 90° Ø 80 (5)
N°1 - Pipe closure cap (6)
N°1 - Intake terminal Ø 80 insulated (7)
N°2 - Internal wall sealing plates (8)
N°1 - External wall sealing plate (9)
N°1 - Discharge pipe Ø 80 insulated (10)
N°1 - Concentric bend 90° Ø 80/125 (11)
Содержание Maior Eolo 24 4E
Страница 1: ...MAIOR EOLO 24 28 32 4E Instruction and warning booklet IE 1 038771ENG ...
Страница 2: ......
Страница 30: ...30 3 5 4 4 5 6 6 d d c INSTALLER USER MAINTENANCE TECHNICIAN ...
Страница 35: ......