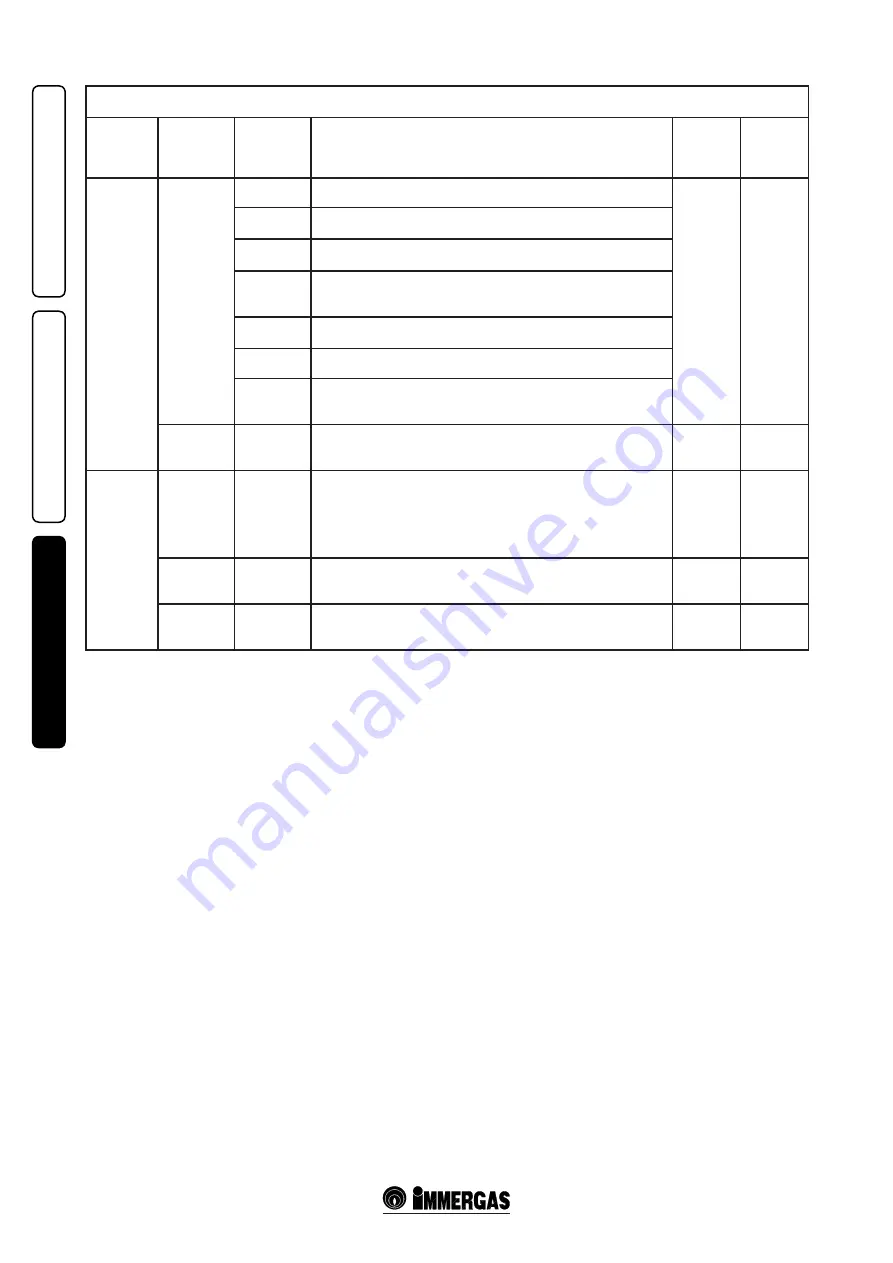
36 - IE
INS
TALLER
US
ER
MAINTEN
AN
CE TECHNI
CI
AN
M5 menu
(password must be entered)
1
st
Level
2
nd
Level
Options
Description
Default
value
Value
set
by the
technician
RELE 3
RELE3-0
Relay 3 not used.
RELE3-0
RELE3-1
Check the storage tank recirculation pump
(not used on this model).
RELE3-2
The relay signals the intervention of boiler block (Can be coupled to an
external signalling device, not supplied).
RELE3-3
The relay signals that the boiler is in heating or cooling request mode (the
status of the system circulator pump is replicated)
(Can be coupled with an external circulator pump, not supplied).
RELE3-4
Controls the opening of an external gas valve in concomitance with an
ignition request of the boiler burner.
RELE3-5
Function not available on this boiler model.
RELE3-6
In the event the boiler circulator pump is replaced with a traditional fixed
speed circulator pump one must connect the new circulator pump to the
relay board.
P76
-15°C ÷
+14°C
CE
With S34 = On. If the reading of the external probe is not correct it is possible
to correct it in order to compensate any environmental factors.
With S34 = Off. Setting not used.
0°C
MAGIS
PAR. 1
0, 25 ÷ 55°C
Heat pump set point value during the heating mode.
Attention: set the same value selected on the heat pump.
By setting the parameter = 0, the functions relating to the heat pump are
disabled and the boiler can operate normally, without taking into account
the activation delays due to combined operation with the heat pump.
45
PAR. 2
20 ÷ 100
(tenths of °C)
Activation band.
Temperature interval to establish the intervention or non-intervention of
the boiler as integration.
50
PAR. 3
0 ÷ 20’
Activation delay.
Time interval relating to the activation, disabling and reactivation of the
boiler integrating the heat pump.
20
Содержание MAGIS Victrix
Страница 1: ...MAGIS Victrix IE Instruction and warning book 1 035518ENG ...
Страница 2: ......
Страница 42: ......
Страница 43: ......