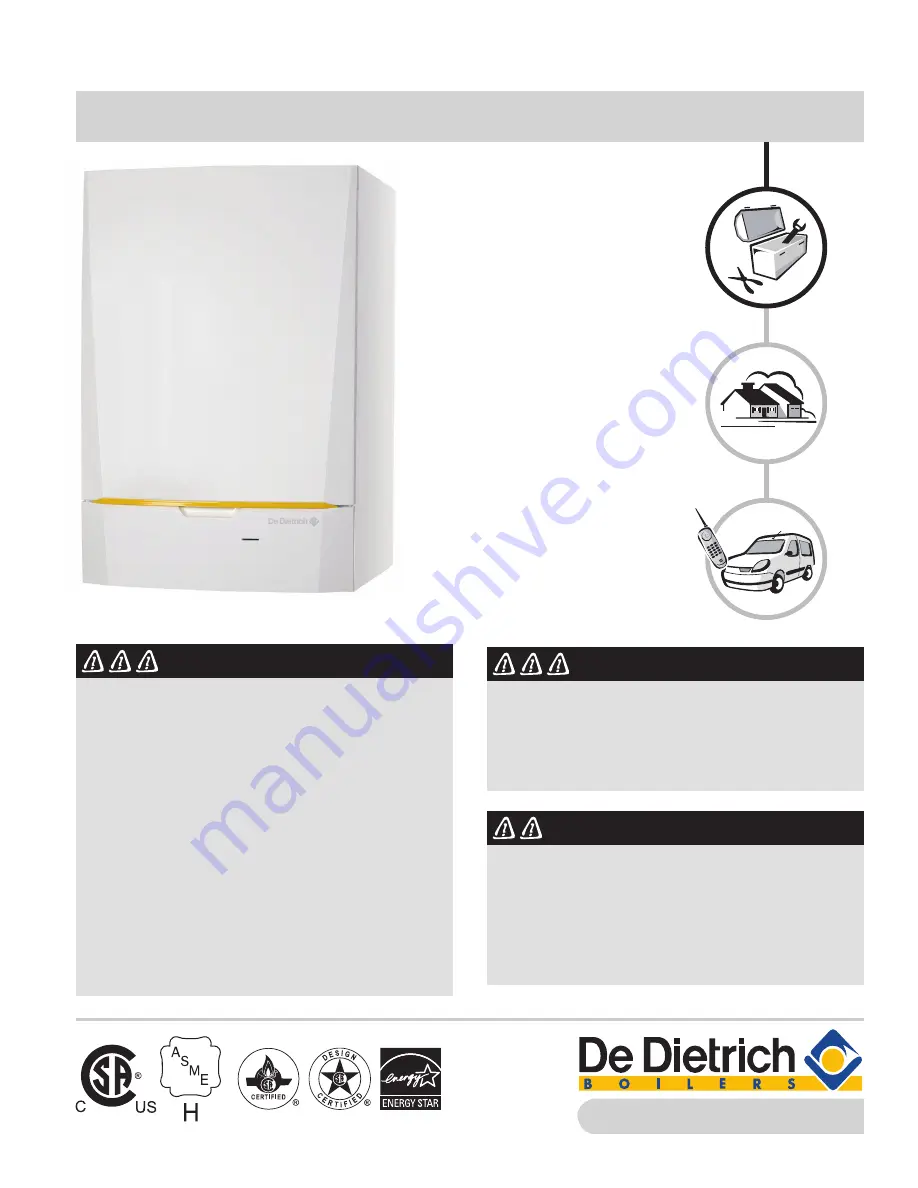
Wall-hung gas-fired condensing boilers
MCA Pro 45/65/90/115
MCA-Pro ISM Rv.4.0 3/2014
www.dedietrichboilers.com
Installation
and Service
Manual
DANGER
If you do not follow these instructions exactly, a fire
or explosion may result causing property damage,
personal injury or death.
Do not store or use gasoline or other flammable
vapors and liquids in the vicinity of this or any other
appliance.
WHAT TO DO IF YOU SMELL GAS:
• Do not try to light or operate any appliance.
• Evacuate all people.
• Do not try to light any appliance.
• Do not touch any electric switch; do not use any
phone in your building.
• Immediately call your gas supplier from a neighbor's
phone. Follow the gas supplier's instructions.
• If you cannot reach your gas supplier, call the fire
department.
Installation and service must be performed by a
professional licensed heating contractor, qualified
installer, service agency or the gas supplier.
WARNING
This manual and all instructions must be read in its
entirety by a qualified and certified installer with the
appropriate gas fitter's license for the jurisdiction
within the area of installation. This manual and ALL
documentation MUST BE READ BEFORE installation to
avoid any possible dangerous conditions. Failure to do
so may create a seriously dangerous situation which
may cause death, severe personal injury or substantial
product/property damage.
Product may not be exactly as shown.
DANGER
When using either PVC, CPVC, Polypropylene or
stainless steel venting the components must be
certified according to ULC-S636 and or UL1738. Read
the Installer and Service Manual prior to installing.
Failure to follow the instructions in the manuals
could lead to death, serious personal injury and or
substantial product and or property damage.
Summary of Contents for MCA Pro 115
Page 45: ...45 MCA Pro 45 65 90 115 MCA Pro ISM Rv 4 1 2 2017 4 Installation H D G C B A E I J F ...
Page 117: ......
Page 118: ......
Page 119: ......