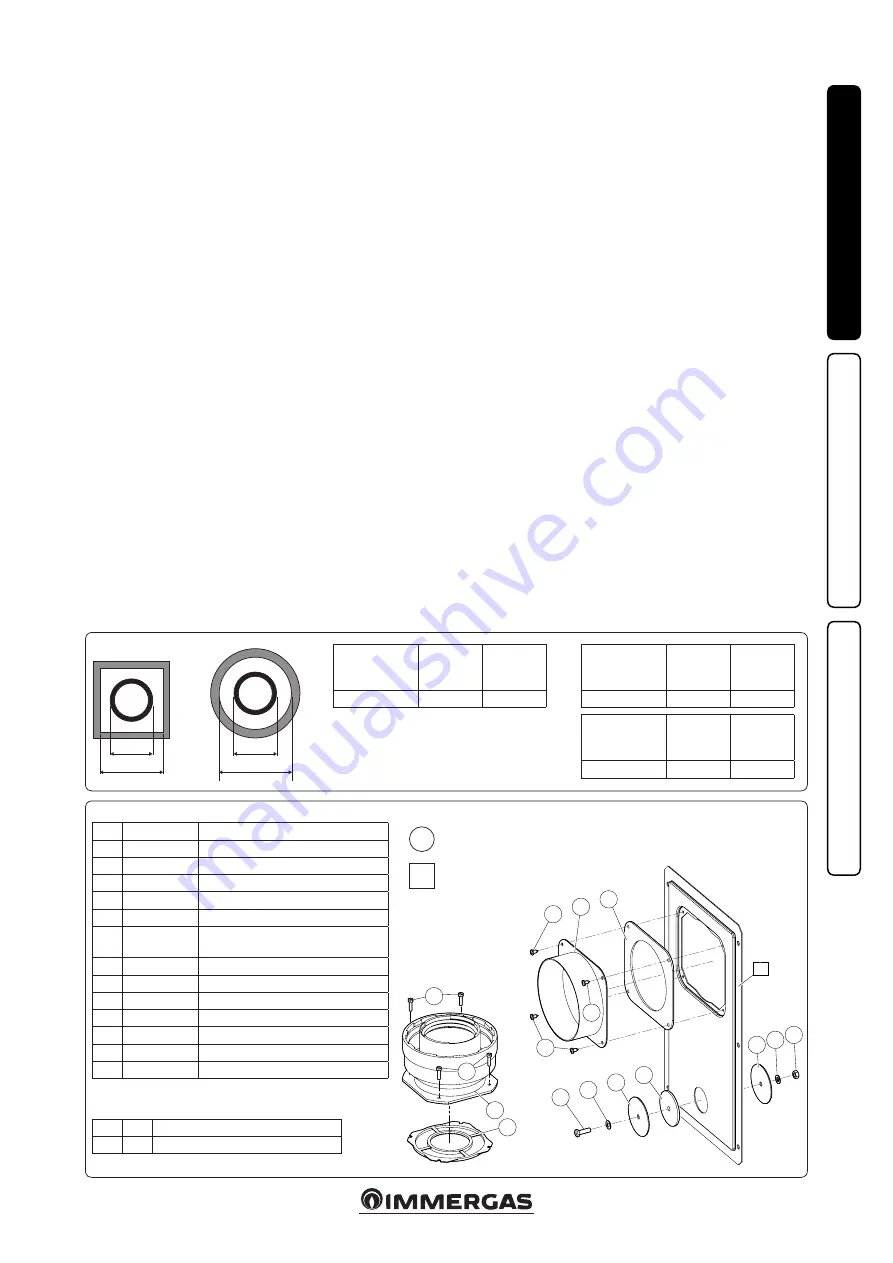
1
2
3
3
3
4
5
6
7
6 8
9
A
10
11
12
12
1-21
1-20
A
B
A
C
15
INS
TALLER
US
ER
MAINTEN
AN
CE TECHNI
CI
AN
Kit composition:
Ref.
Qty
Description
1
1
Door adaptor Ø 100 or Ø 125
2
1
Door gasket made of neoprene
3
4
Screws 4.2 x 9 AF
4
1
Hex headed screw M6 x 20
5
1
Flat nylon washer M6
6
2
Door hole closure metal-sheet plate
plug
7
1
Plug gasket made of neoprene
8
1
Toothed washer M6
9
1
Nut M6
10 1 (kit 80/125) Concentric gasket Ø 60-100
11 1 (kit 80/125) Flanged adapter Ø 80-125)
12 4 (kit 80/125) Hex headed screws M4 x 16 slotted
-
1 (kit 80/125) Bag of lubricating talc
Installation drawings key:
Unique identification of the component in
the kit
Identification of the component not supplied
in this kit
1
A
Supplied separately:
Ref. Qty Description
A
1
Ducting kit door
Rigid Ø 80
ducting
(A)
mm
SHAFT
(B) mm
SHAFT
(C) mm
86
126
146
Flexible Ø 80
ducting
(A)
mm
SHAFT
(B) mm
SHAFT
(C) mm
90
130
150
Rigid Ø 60
ducting
(A)
mm
SHAFT
(B) mm
SHAFT
(C) mm
66
106
126
1.14 ADAPTOR C9 KIT INSTALLATION.
This kit allows an Immergas boiler to be installed
in "C
93
" configuration, with combustion air intake
directly from the shaft where the flue gas exhaust
is, obtained by means of a ducting system.
System composition.
The system must be combined with the following
components (sold separately) to be functional
and complete:
- kit C
93
Ø 100 or Ø125 version
- ducting kit Ø 60 or Ø 80
- fumes exhaust kit Ø 60/100 or Ø 80/125 con-
figured according to the installation and type
of boiler.
Kit Assembly.
- Mount the components of kit "C9" on the door
(A) of the ducting system (Fig. 1-21).
- (Version Ø 125 only) mount the flanged adap-
tor (11) interposing the concentric gasket (10)
on the boiler, fitting it with the screws (12).
- Mount the ducting system as described in the
relative instructions sheet.
- Calculate the distances between the boiler drain
and the bend of the ducting system.
- Prepare the boiler flue system, making sure that
the internal pipe of the concentric kit is fitted
properly in the bend of the ducting system
(quota "X" fig. 1-22), while the external pipe
must be fitted on the adaptor until it stops (1).
N.B.:
to encourage the removal of possible
condensate forming in the exhaust pipe, tilt
the pipes towards the boiler with a minimum
slope of 1.5%.
- Mount the cover (A) complete with adaptor (1)
and caps (6) on the wall and assemble the flue
system to the ducting system.
N.B.:
(version Ø 125 only) before assembly
check the gaskets are in the right position. In
the event component lubrication (already car-
ried out by the manufacturer) is not sufficient,
remove the residual lubricant using a dry cloth,
then to ease fitting coat the parts with common
or industrial talc.
Once all components have been assembled prop-
erly, the exhaust fumes will be expelled via the
ducting system; the combustion air for normal
boiler operation will be aspirated directly by the
shaft (Fig. 1-22).
Technical data.
- The dimensions of the shafts must ensure a
minimum gap between the outer wall of the
smoke duct and the inner wall of the shaft: 30
mm for circular section shafts and 20 mm in
the event of a square section shaft (Fig. 1-20).
- Maximum 2 changes of direction are allowed
on the vertical section of the flue system with
a maximum clearance angle of 30° with respect
to the vertical.
- The maximum vertical extension using a Ø 60
ducting system is 13 m, the maximum exten-
sion includes 1 bend Ø 60/10 at 90°, 1 m of
horizontal pipe 60/100, 1 90° ducted bend Ø
60 and the roof terminal for ducting.
To determine the C
93
flue system in configura-
tions other than that described (Fig. 1-22)
one must consider that 1 metre of ducted pipe
according to the indications described has a
resistance factor equal to 4.9.
- The maximum vertical extension using a Ø 80
ducting system is 28 m, the maximum exten-
sion includes 1 adapter 60/100 to 80/125, 1 87°
bend Ø 80/125, 1 m of horizontal pipe 80/125,
1 90° ducted bend Ø 80 and the roof terminal
for ducting.
To determine the C
93
flue system in configura-
tions other than that described (Fig. 1-22) one
must consider the following pressure drops:
- 1 m of concentric pipe Ø 80/125 = 1 m of
ducted pipe;
- 1 87° bend = 1.4 m of ducted pipe;
Consequently one must subtract the equivalent
length of the part added to the 28 m available.