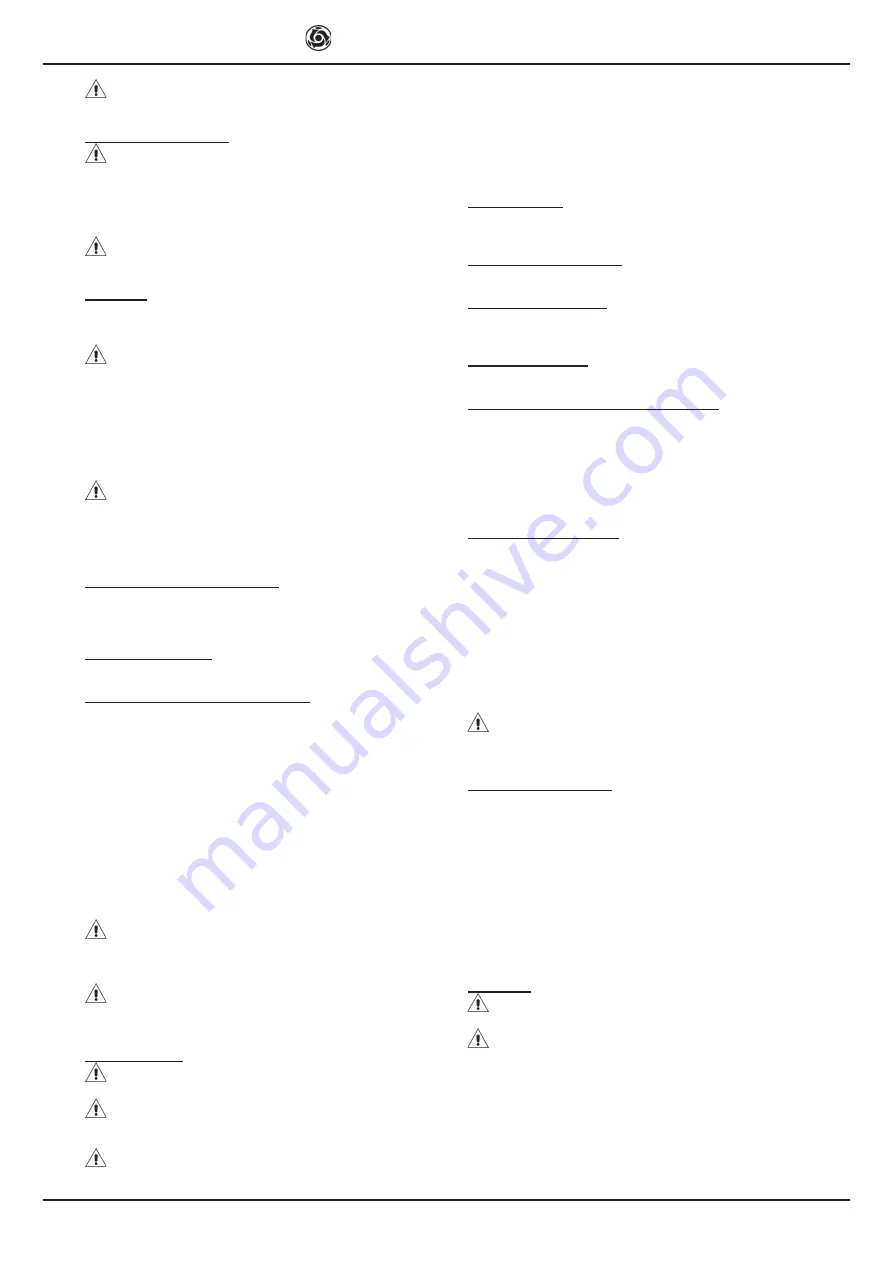
IMER INTERNATIONAL S.p.A.
MASONRY 750
15
machine.
- To resume work after a voltage cut-off, turn the selector to
zero and repeat point 12.5 (ref.9, fi g.1).
15.1 Vertical disk movement
- Always switch off the machine before carrying out blade
adjustment.
To raise or lower the disk, work on the lever (ref.19, g.1) until reaching
the required height from the cutting table and tighten the clamping lever
(ref.17, g.1)
- Make sure that the clamping lever is fi rmly tightened before
starting to work.
15.2 Cutting
For safe use of the machine when cutting, push the carriage forwards
as the cut advances, placing your hands to the two sides of the carriage.
Never push directly on the piece to be cut.
- Check alignment of the disk in relation to the cutting line.
1. Place the workpiece on the worktable (ref.4, g.1), resting rmly
against the stop.
2. Start the engine.
3. Wait until the water reaches the blade.
4. Begin cutting.
5. Horizontal cutting movement is carried out by pulling the carriage
towards the blade.
- The higher the cutting height, the greater the effort required
at the disk to cut the piece. Therefore, the operator will have to
adjust the carriage advance speed to avoid overloading the en-
gine. This speed also depends on the type of material to be cut
(hardness, toughness, etc....).
15.3.1 Cutting downwards from above
Release the cutting head working on the clamping lever (ref.17, g.1).
Position the piece to be cut. Start the sawing machine and start cutting
downwards from above working on the head lever (ref.19, g.1).
15.3.2 Changing the disk
For changing the disk, please refer to paragraph 4.
16. USING 700 DIAMETER CUTTING WHEEL
A 700 mm diameter cutting disk can be tted on the machine. Operation
involves setting the cutter head stroke. This operation is carried out at
the factory by the manufacturer for a 750 mm diameter disk. If not car-
ried out properly, this adjustment can damage the machine and cause
hazard for persons, it must be carried out by competent and quali ed
personnel.
Proceed as follows:
1. Make sure that the machine is disconnected from the power supply.
2. Fit the 700 mm diameter disk according to the procedure described
in paragraph 14.
3. Loosen the bolt (ref.18, g.1).
4. Lower the cutting head until the disk is in the best cutting position (the
disk outside diameter should protrude 15 mm from the cutting surface).
5. Turn the cam until locking the cutting head and tighten the bolt.
At this point, the cutting head is adjusted for a 700 mm diameter disk.
- To refi t a 750 mm diameter disk, the adjustment should be
repeated restoring the original setting. If adjustment is not carried
out, the 750 mm disk would interfere with the piece holder carriage
structure and damage it with the risk of breakage.
- Note that the blade must have an external diameter of 700
mm, a central hole diameter of 25.4 mm and max. thickness of 4
mm.
17. MAINTENANCE
- Servicing must always be carried out by qualifi ed techni-
cians and only after the motor has been switched off.
- Always keep the guards in proper working order and free
from damage.Take particular care to ensure that the blade guards
are kept effi cient and clean, replacing them if they are damaged.
- As there is the continuous risk of inadvertent damage to the
electric cables, these must be checked regularly each time before
the machine is used.
In particular, keep the blade guards in ef cient conditions and clean,
changing them when damaged.
Never leave the machine outdoors: it must be sheltered from the wea-
ther.
Below is a list of the cleaning operations that must be carried out at the
end of every shift.
17.1 Tank cleaning
Empty the tank by removing the drain plug. Remove cutting residue
using a jet of water.
17.2 Tank removal (ref.1, fi g.7)
Empty the drum opening the drum cap from right or left side.
17.3 Work surface cleaning
Always keep work surfaces clean. Residual dirt can impair cutting pre-
cision.
17.4 Guide rail cleaning
It is good practice to remove all traces of dirt from the guides.
17.5 Cleaning and maintenance of cooling circuit
If water does not reach the blade stop the machine immediately to avoid
blade damage.
After stopping the machine check that the water level in the tank is suf-
cient.
If necessary, after disconnecting the machine from the power supply
check that the tap, hose and pump lter are not blocked
17.6 Tensioning the drive belt
1. Switch off the electric motor and remove the plug from the power
supply.
2. Unscrew the 4 screws that secure the movable belt guard (ref.1,
g.8).
3. Loosen the 4 (ref.2, g.8) screws that clamp the electric motor to the
blade support.
4. Tension the belt using the nut (ref.3): applying a force of about F=6
Kg to the centre of the free section of the belt, the arrow should be about
f=6 mm ( g.9).
5. Tighten the screws on the electric motor (ref.2, g.8), checking the
alignment of the motor pulley and the blade pulley
6. Re t the guard and lock it using the 4 screws (ref.1, g.8).
- To avoid shortening the life of the belt, the bearings and the
blade shaft, do not overtension the belt. Finally, check the two pul-
leys are aligned.
17.7 Changing the drive belt
1. Switch off the electric motor and disconnect the plug.
2. Slacken the 4 screws fastening the belt mobile guard (ref.1, g.8).
3. Slacken the 4 screws (ref.2, g.8) fastening the electric motor on the
disk holder arm.
4. Slacken the belt working on the screws (ref.3, g.8) and replace it
with the new one.
5. Pull the belt working on the screws (ref.3, g.8): if the belt tension
is correct, applying a force of approx. F=6 Kg at the centre of the free
section of belt, the camber should be approx. f=6 mm ( g.9).
6. Tighten the electric motor screws (ref.2, g.8), checking the alignment
of the motor pulley and that of the disk.
7. Re t the belt guard and lock it with the 4 screws (ref.1, g.8).
17.8 Repairs
- Before carrying out any maintenance operations, switch off
the machine, and remove the plug from the power socket.
- If the guards are removed to carry out repairs, they must be
refi tted properly when the repair work is fi nished.
Only use genuine IMER spare parts and do not modify them.
GB