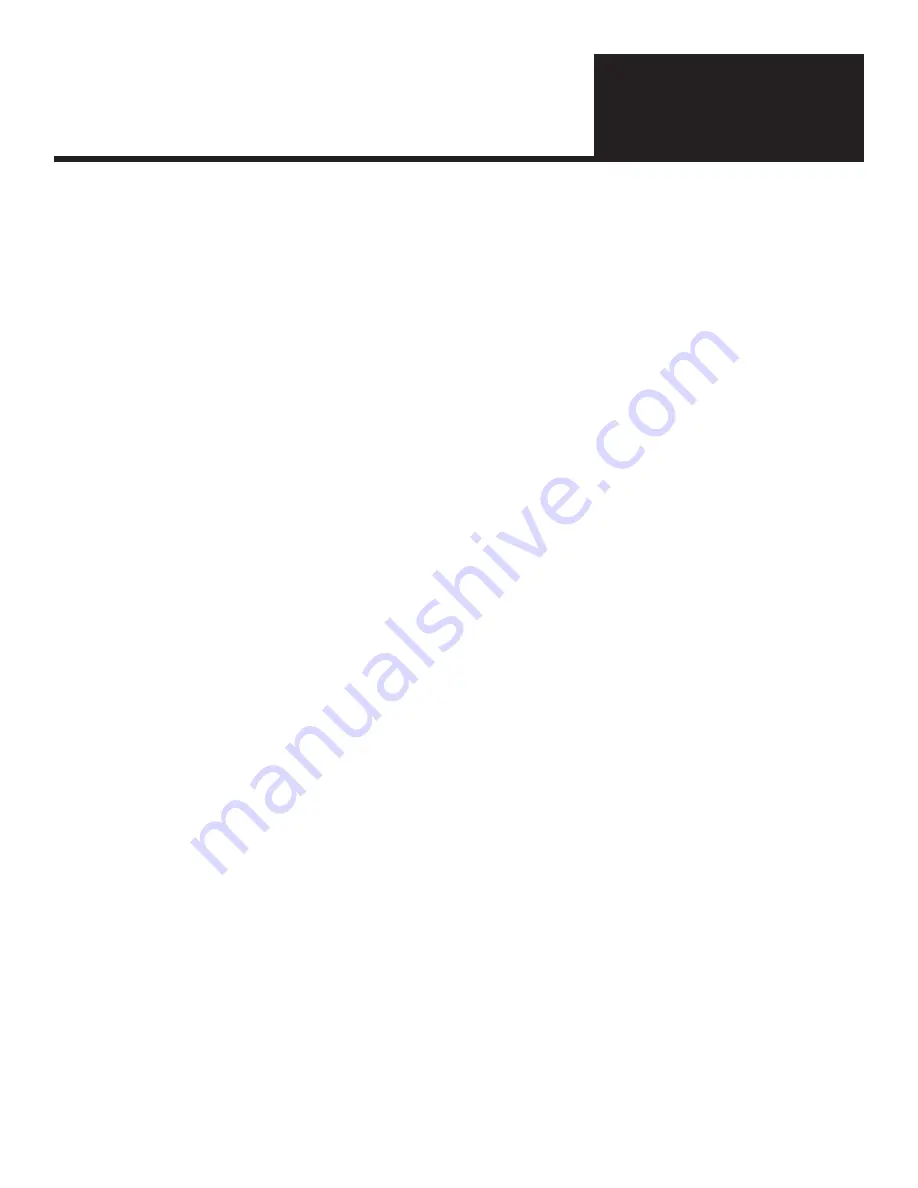
1
Special Welding
Techniques
Section 5
quence as DASW. At the end of the weld cycle gas post-flow begins. After the gas post-flow concludes the entire weld cycle
is complete and the weld tool can be removed.
While the actual weld arc times are similar to DASW there is typically gas pre-flow and post-flow times which add to the
overall time per weld.
Since no ferrule is required handling and cleanup are reduced. The absence of a ferrule has pros and cons. On the plus side
it can reduce the cost of the studs. It also lends itself to automated processes since the handling operations are reduced. On
the minus side there is less fillet control. This can create difficulties when welding in any direction other than down handed.
Additionally, shielding gas does not typically offer as deep of penetration as flux.
Short cycle Stud Welding (SCSW)
This process is similar to DASW except no flux load or ferrule is used. Instead of a ferrule grip and ferrule a spark
shield is used. The process sequence is the same as for DASW. Because there is no flux or shielding gas this process typi-
cally exhibits porosity. The fundamental difference between this process and DASW is that high currents and short weld
times are used. The short weld time minimizes the effect of the porosity.
This is the least expensive process in that no ferrule or gas is utilized. This process also uses the shortest weld times. Short
weld times are used to minimizes the porosity from the unshielded atmosphere. Because of the porosity inherent in this
process it is generally not a recommended process. Factors such as thin sheet metal, insignificant strength requirements,
significant cost constraints, and very high installation speed requirements may over ride weld quality and this process may be
chosen.
Gas Arc Short Cycle Stud Welding (GASCSW)
This process combines GASW and SCSW. This uses the short cycle process, but adds shielding gas to eliminate the
effects of porosity. By reducing the weld time versus GASW there is better fillet control. However, weld current require-
ments are increased and can require a larger power supply. The reduced weld time also reduces weld penetration. This
can be a plus for arc welding onto thinner gauge sheet metal. Because shielding gas is used, the installed cost is greater than
SCSW, but porosity is eliminated.
SPeCIAL TeChNIQUe DISCUSSION
Low-Carbon Steel
Low-carbon (mild) steels can be stud welded with no major metallurgical problems. The upper carbon limit for steel to
be arc stud welded without preheat is 0.30 percent. If work sections are relatively thin for the stud diameters being welded,
the carbon limit may be somewhat higher because of the decreased cooling effect of the work. If the section to which the
stud is to be welded is relatively thick, stud welding of steel with more than 0.30 percent carbon using normal techniques
and without preheat must be evaluated. The most important factor regarding work section thickness is that the material
must be heavy enough to permit welding the studs without melt-through.
Medium Carbon Steel
If medium carbon steels are to be stud welded, it is imperative that preheat be used to prevent cracking in the heat- af-
fected zones. In some instances, a combination of preheating and post-heating after welding is recommended. In the case
of tough alloy steels, either preheating or post-heating may be used to obtain satisfactory results. In cases where the welded
assemblies are to be heat treated for hardening after the welding operation, the preheating or post-heating operation may be
eliminated if the parts are handled in a manner that prevents damage to the studs.
Содержание Smartweld SW1200
Страница 9: ...Safety Precautions Section 1 Symbols and Definitions...
Страница 14: ...14 Installation Set Up Section 2 230 Volt Jumper Configuration 60Hz 460 Volt Jumper Configuration 60Hz...
Страница 40: ...40 Parts List Section 9 230 460 60 Hz Parts List...
Страница 42: ...42 Schematic Diagram Section 10...
Страница 44: ...44 Parts List Section 11 220 380 50 Hz Parts List...