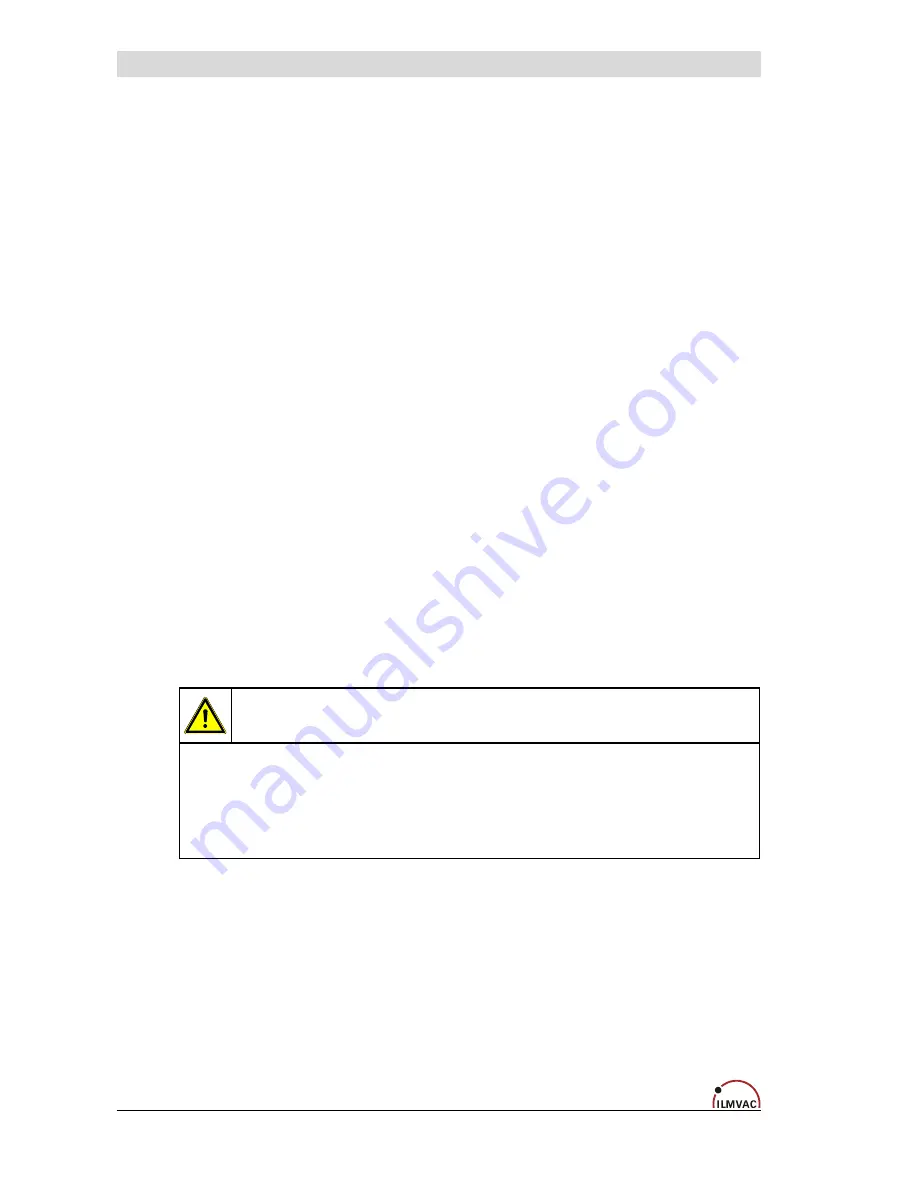
Maintenance and Servicing
6 Maintenance
and
Servicing
6.1 General
Requirements
Repairs of the chemvac combination pump system may only be performed by the manufac-
turer or authorized workshops. The prerequisites are a complete and factually correct dam-
age report, and a clean and, if necessary, a decontaminate device.
•
Check the
diaphragm pump
daily for unusual running noises and heat building up on the
surface of the pump. We recommend changing the diaphragm after 10,000 operating
hours. The user may specify that the exchange be made earlier, depending upon the
application process.
•
Check the level and quality of the oil in the
rotary vane pump
every day. Comply with
the oil change intervals, if necessary they can be defined by the user.
•
Check the electrical and vacuum connections daily.
•
Check the screw connections and hoses for leaks every day, and exchange if necessary.
•
Check the
glass vessels of the separator AKD
separator for integrity and exchange if
necessary. Empty the glass vessel in good time, comply with the regulations for the dis-
posal of hazardous substances. Check that the filter cartridge is in good working order.
The filter cartridge must be exchanged if the in-built valve is actuated during operation.
•
Check that the
pressure control valve
is in good working order, open the valve (4
screws) and clean the seating if necessary.
6.2
Maintenance Performed by the User
The user can perform maintenance work as described below.
WARNING !
Only perform the work that is described here, and that which is permitted to be done
by the user.
All other maintenance and service work may only be performed by the manufacturer
or a dealer authorized by him.
Beware of the pump parts being possibly contaminated by hazardous substances.
Wear protective clothing if there is contamination.
A regeneration phase is required after pumping aggressive media or solvent vapours in or-
der to maintain the serviceability and reliability of the chemvac combination pump system.
This means that you let the chemvac combination pump system run for one hour at ultimate
pressure. The bubbler on the rotary vane pump must remain open. The ultimate pressure at
the suction port must be checked by means of a vacuum gauge. The regeneration process
has been completed when the maximum possible improvement of the ultimate pressure has
been attained.
18 109025