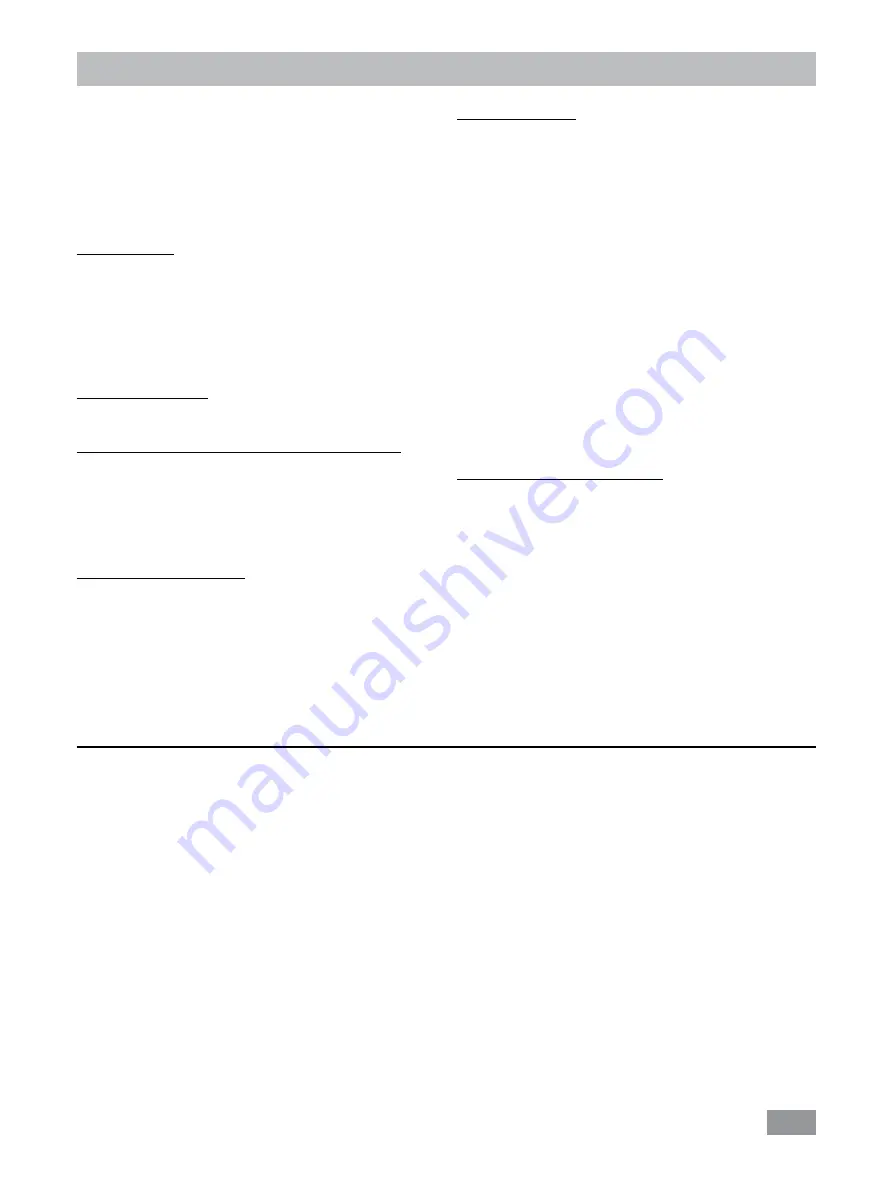
16
RS 232 interface:
Configuration:
- The functions of the interface connections between the
stirrer machine and the automation system are chosen
from the signals specified in EIA standard RS 232 in ac-
cordance with DIN 66 020 Part 1�
- For the electrical characteristics of the interface and the al-
location of signal status, standard RS 232 applies in accor-
dance with DIN 66 259 Part 1�
- Transmission procedure: asynchronous character transmis-
sion in start-stop mode�
- Type of transmission: full duplex�
- Character format: character representation in accordance
with data format in DIN 66 022 for start-stop mode� 1
start bit; 7 character bits; 1 parity bit (even); 1 stop bit�
- Transmission speed: 9600 bit/s�
- Data flow control: none
- Access procedure: data transfer from the stirrer machine to
the computer takes place only at the computer’s request�
Command syntax and format:
The following applies to the command set:
- Commands are generally sent from the computer (Master)
to the device (Slave)�
- The device sends only at the computer’s request� Even
fault indications cannot be sent spontaneously from the
device to the computer (automation system)�
- Commands are transmitted in capital letters�
- Commands and parameters including successive param-
eters are separated by at least one space (Code: hex 0x20)�
- Each individual command (incl� parameters and data) and
each response are terminated with CR LF (Code: hex 0x0d
hex 0x0A) and have a maximum length of 80 characters�
- The decimal separator in a number is a dot (Code: hex
0x2E)�
Interface and output
The device can be operated in “Remote” mode via the RS
232 port or the USB port connected to a PC and with the
laboratory software Labworld
soft
®
�
Note:
Please observe the system requirements together
with the operating instructions and help section included
with the software�
USB interface:
The Universal Serial Bus (USB) is a serial bus for connect-
ing the device to the PC� Equipped with USB devices can
be connected to a PC during operation (hot plugging)�
Connected devices and their properties are automatically
recognized� The USB interface can also be used to update
firmware�
USB device drivers:
First, download the latest driver for
IKA
devices with USB
interface from:
http://www.ika.com/ika/lws/download/usb-driver.zip.
Install the driver by running the setup file� Then connect the
IKA
device through the USB data cable to the PC�
The data communication is via a virtual COM port� Configu-
ration, command syntax and commands of the virtual COM
ports are as described in RS 232 interface�
Device software update:
For device software update, visit
IKA
website
www.ika.
com
and enter the “Service” menu� Download and run the
Firmware Update Tool�
Find and click the Firmware Update Tool in your PC after
installation� Register your E-mail and password�
Connect the device to your PC via the USB cable� Then, you
can update the device software according to instructions of
the Firmware Update Tool�
The above details correspond as far as possible to the recommendations of the NAMUR working party (NAMUR recom-
mendations for the design of electrical plug connections for analogue and digital signal transmission on individual items of
laboratory control equipment, rev� 1�1)�
The NAMUR commands and the additional specific
IKA
co mmands serve only as low level commands for communica-
tion between the device and the PC� With a suitable terminal or communications programme these commands can be
transmitted directly to the circulator equipment� The
IKA
software package, Labworldsoft
®
, provides a convenient tool for
controlling circulating equipment and collecting data under MS Windows, and includes graphical entry features, for pump
motor speed ramps for example�
Содержание RC 5 basic
Страница 1: ...IKA RC 5 basic Operating instructions EN ...