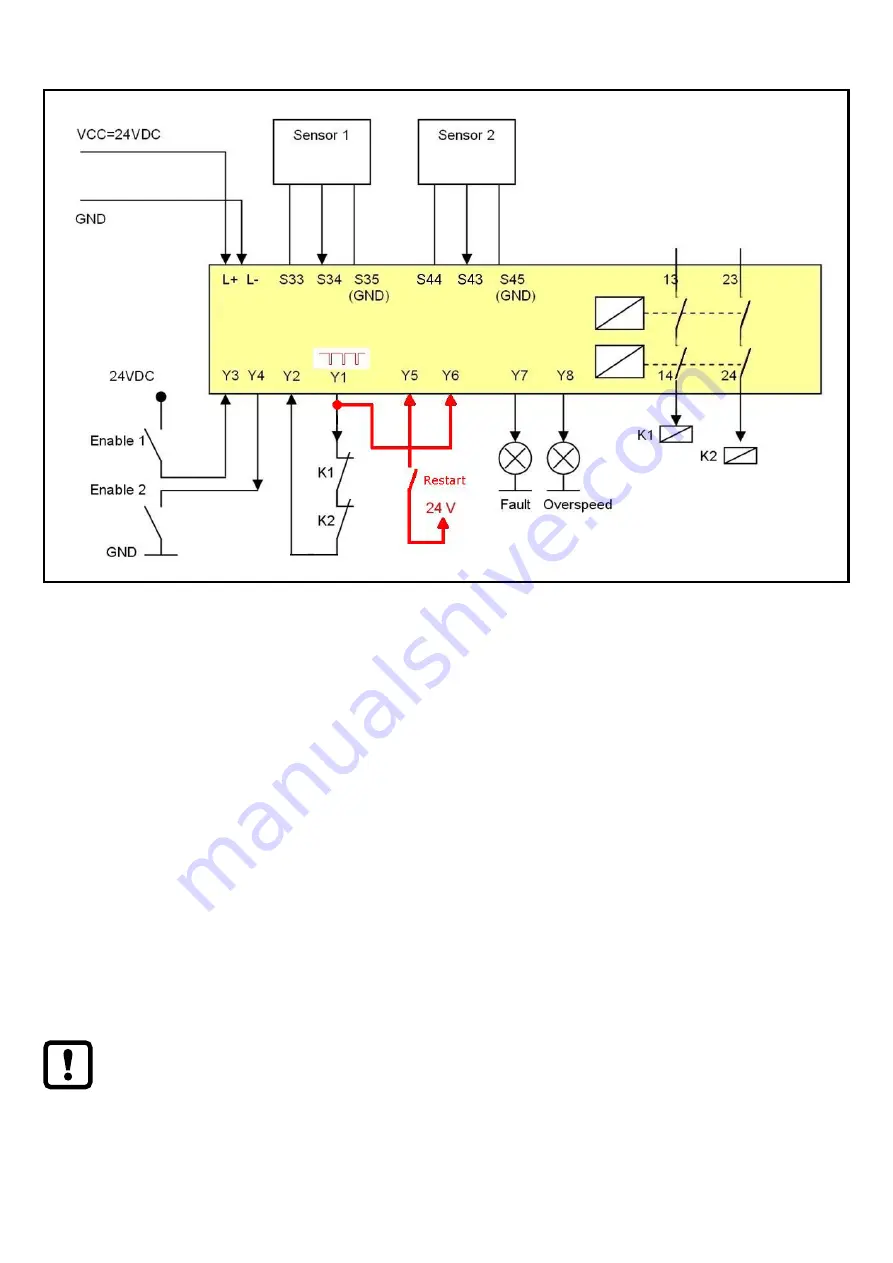
14
5.2.2 Manual mode
Manual mode
In this operating mode, the outputs of the device are only activated if the input
frequency is below the target value and after the restart signal has been sent to
the device via an external restart command (terminal Y5)�
Once the overspeed has been detected, the relay outputs are not switched�
The sequence described above must be repeated in order to re-activate them�
Manual operation is implemented when during initialisation input Y6 is on the
pulsed test signal of Y1 and input Y5 is open�
In this case the current path remains open until there is a restart signal on input
Y5� The restart signal on input Y5 responds after the falling edge (a complete
transition 0 V DC → + 24 V DC → 0 V DC ) of this input. This signal is only active
if the frequency is below the Foh value�
The restart command element must be installed outside the hazardous
area in a position where the hazardous area and the entire work area
concerned are clearly visible�
The device may also be installed within the hazardous area� It is not
required to operate it from outside the hazardous area�