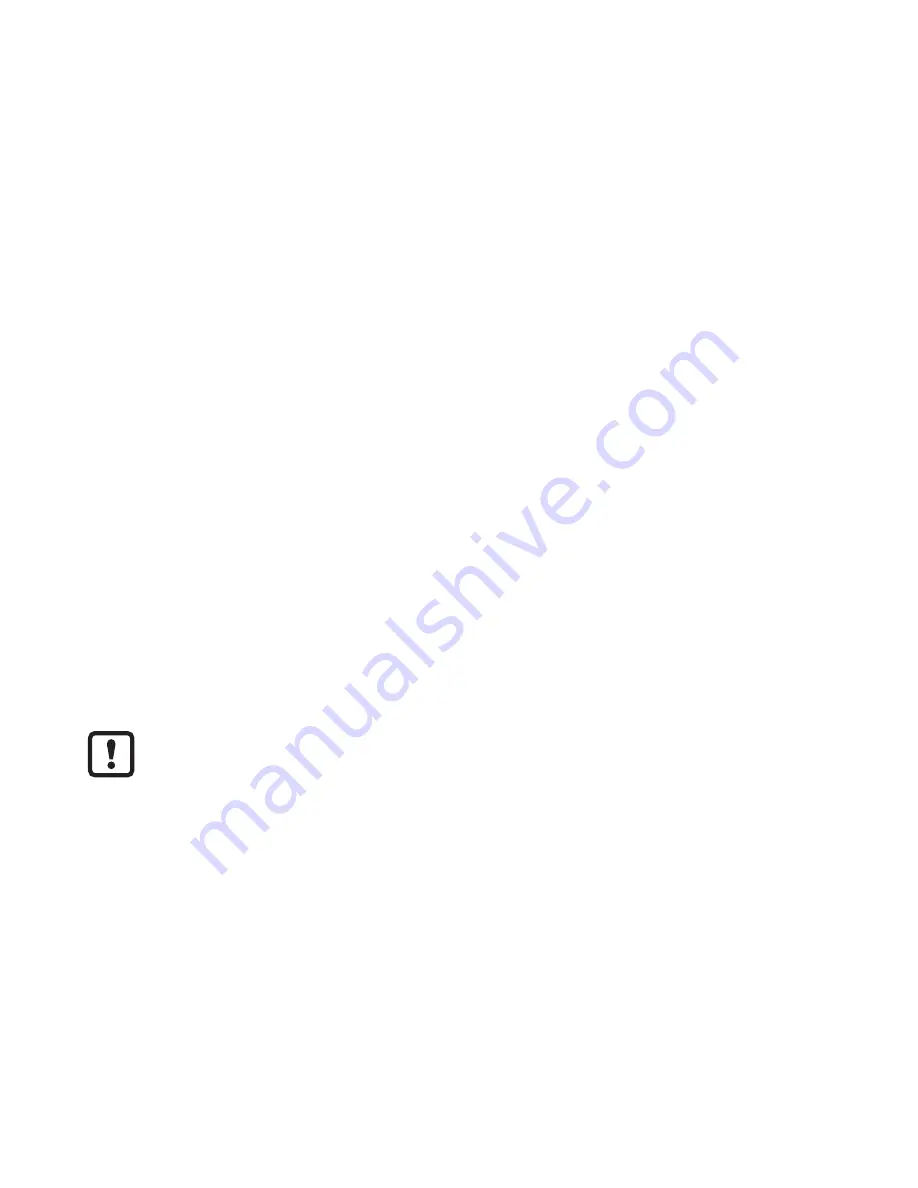
6
exposure to a mechanical hazard�
For the control system this means the following:
-Switch-on commands which cause hazardous situations must become active
only when the safety guard is in a protective position and the guard locking in
locked position�
-The locked position of the guard locking must be released only when the
hazardous situation is no longer present�
Before safety switches are used, a risk assessment must be performed on the
machine, e�g� according to
-EN ISO 13849, Safety of machinery - Safety-related parts of control systems
-EN 12100-1, Safety of machinery - General principles for design - Risk
assessment and risk reduction
Correct use includes compliance with the relevant requirements for installation
and operation, in particular
-IEC 62061, Safety of machinery - Functional safety of safety-related electrical,
electronic and programmable electronic control systems
-EN ISO 13849, Safety of machinery - Safety-related parts of control systems
-EN 14119, Interlocking devices associated with guards
-EN 60204-1, Electrical equipment of machines
The user is responsible for a safe integration of the device into a safe
overall system�
►
Validate the whole system, e�g� to EN ISO 13849-2�
If the simplified procedure to EN ISO 13849-1:2016 (section 6�3) is used for
validation, the performance level (PL) may be reduced in the event of several
units being connected in series� If a data sheet is supplied with the product, the
specifications of the data sheet apply in case of deviations from the operating
instructions�
5 Structure and operating principle
AS-Interface safety switches, type AC903S/AC904S feature a slave interface to
the safety bus AS-Interface Safety at Work� They enable locking of movable safety
guards�
Содержание AC903S
Страница 1: ...7390915 03 01 2017 Original operating instructions Safety switch with guard locking AC903S AC904S UK ...
Страница 3: ...3 UK 15 Standards and approvals 22 15 1 Directives and standards 22 15 2 Approvals 22 ...
Страница 16: ...16 11 Scale drawing 55 25 144 190 41 4 240 154 M12x1 30 38 5 44 50 46 4 ...
Страница 23: ...23 UK ...