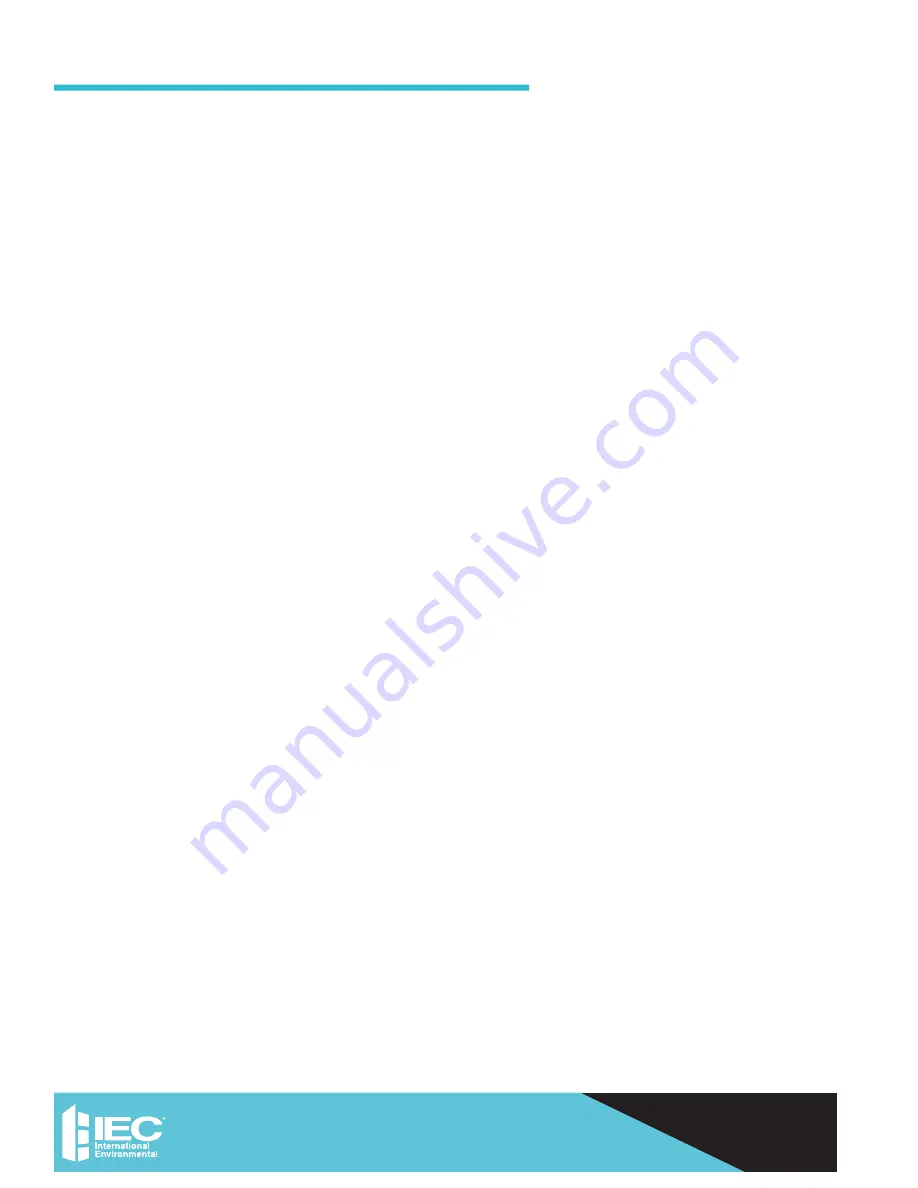
Fan Coils
INSTALLATION, OPERATION, & MAINTENANCE MANUAL
4
SECTION ONE — Receipt & Initial Installation
Preface
International Environmental Corporation fan coil units
represent a prudent investment offering trouble-free
operation and long service with proper installation,
operation, and regular maintenance.
Your equipment is initially protected under the
manufacturer’s standard warranty; however, this
warranty is provided under the condition that the steps
outlined in this manual for initial inspection, proper
installation, regular periodic maintenance, and everyday
operation of the equipment be followed in detail. This
manual should be fully reviewed in advance before initial
installation, start-up, and any maintenance. Should
any questions arise, please contact your local Sales
Representative or the factory BEFORE proceeding.
The equipment covered by this manual is available with a
variety of options and accessories. Consult the approved
unit submittals, order acknowledgment, and other manuals
for specific details on unit options and accessories.
No attempt should be made to handle, install, or service
any unit without following safe practices regarding
mechanical equipment.
The equipment must always be properly supported.
Temporary supports used during installation or service
must be adequate to hold the equipment securely.
All power must be disconnected before any installation
or service is attempted. More than one power source
may be supplied to a unit. Power to remote mounted
control devices may not be supplied through the unit.
Never wear bulky or loose fitting clothing when working
on any mechanical equipment. Gloves should always
be worn for protection against heat and other possible
injuries. Safety glasses or goggles should always be
worn, especially when drilling, cutting, or working with
chemicals such as refrigerants or lubricants.
Never pressurize any equipment beyond specified test
pressures as shown on unit rating plate. Always pressure
test with an inert fluid or gas such as clear water or dry
nitrogen to avoid possible damage or injury in the event
of a leak or component failure during testing.
Always protect adjacent flammable material when
welding or soldering. Use a suitable heat shield material
to contain sparks or drops of solder. Have a fire
extinguisher readily available.
The manufacturer assumes no responsibility for personal
injury or property damage resulting from improper or
unsafe practices during the handling, installation, service,
or operation of any equipment.
Unpacking and Inspection
All units are carefully inspected at the factory throughout
the manufacturing process under a strict detailed quality
assurance program. All major components and sub-
assemblies are carefully tested for proper operation
and verified for full compliance with factory standards.
Operational testing of some customer-furnished
components such as pneumatic control valves and
switches may be a possible exception.
Each unit is carefully packaged for shipment to avoid
damage during normal transit and handling. Equipment
should always be stored in a dry and covered location and
in the proper orientation as marked on the carton.
All shipments are made F.O.B. factory and it is the
responsibility of the receiving party to inspect the
equipment upon arrival. Any obvious damage to the
carton and/or its contents should be recorded on the bill of
lading and a claim should be filed with the freight carrier.
After determining the condition of the carton exterior,
carefully remove each unit from the carton and inspect
for hidden damage. At this time, check to make sure that
“furnished only” items such as switches, thermostats, etc.
are accounted for. Any hidden damage should be recorded
and immediately reported to the carrier and a claim filed.
In the event a claim for shipping damage is filed, the unit,
shipping carton, and all packing must be retained for
physical inspection by the freight carrier. All equipment
should be stored in the factory shipping carton with
internal packing in place until installation.
At the time of receipt, the equipment type and
arrangement should be verified against the order
documents. Should any discrepancy be found, the local