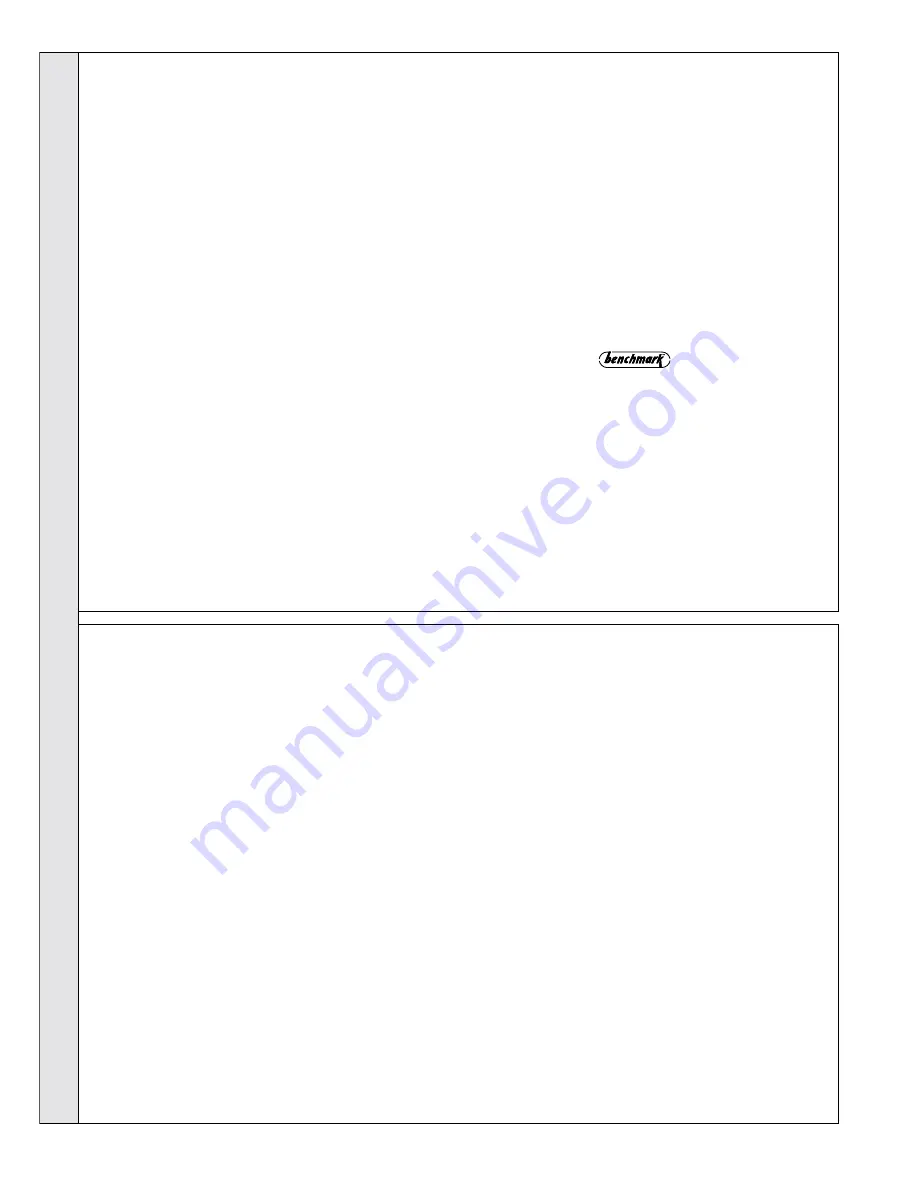
30
SERVICING
isar -
Installation and Servicing
41
SERVICING SCHEDULE
To ensure the continued safe and efficient operation of the
appliance it is recommended that it is checked at regular
intervals and serviced as necessary. The frequency of
servicing will depend upon the installation condition and
usage but should be carried out at least annually.
It is the law that any service work must be carried out by a
CORGI registered installer. In IE service work must be carried
out by a competent person.
Note.
Some aluminium oxide build-up on the heat exchanger
fins is usual with this type of condensing boiler. Though
removal is recommended annually, the heat exchanger
MUST be inspected and cleaned after a MAXIMUM of 2
years operation.
1. Light the boiler and carry out a pre-service check, noting
any operational faults.
2. Check the gas consumption.
3. Connect a suitable gas analyser to the sampling point on
the top of the boiler (refer to Frame 43) or into the flue
terminal if access is possible (optional test).
For correct boiler operation, the CO/CO
2
content of the flue
gas should not be greater than 0.004 ratio.
If this is the case, and the gas input is at least 90% of the
nominal, then no further action need be taken. If not,
proceed to Step 5 but see note above.
4. Clean the main burner.
5. Clean the heat exchanger.
6. Check the condition of the combustion chamber
insulation. Any cracked or damaged pieces should be
replaced.
7. Check the main injector for blockage or damage.
8. Wherever possible remove and clean the condensate ‘S’
trap (refer to Frame 47) and check the drain for blockage.
9. Check that the flue terminal is unobstructed and that the
flue system is sealed correctly.
10. Check the DHW filter for blockage. Refer to Frame 25.
The servicing procedures are covered more fully in Frames
42-49 and MUST be carried out in sequence.
Note.
In order to carry out either servicing or replacement of
components the boiler front panel and sealing panel
must be removed. Refer to Frames 42 and 43.
WARNING.
Always turn OFF the gas supply at the gas
service cock, and switch OFF and disconnect the electricity
supply to the appliance before servicing.
IMPORTANT.
11. After completing the servicing or exchange of components
always test for gas soundness and carry out functional
checks in 3 and 4 above.
12. When work is complete the sealing panel MUST be
correctly refitted, ensuring that a good seal is made.
Do NOT OPERATE the boiler if the sealing
panel is not fitted.
13. If, for any reason, the condensate ‘S’ trap has been
removed ensure the trap is refilled with water before
reassembling.
14. Complete the service section in the Benchmark log book.
40
HANDING OVER
7. If a programmer is fitted draw attention to the Programmer
Users Instructions and hand them to the householder.
8. Loss of system water pressure
Explain that the dial underneath the boiler indicates the
central heating system pressure and that if the normal COLD
pressure of the system is seen to decrease over a period of
time then a water leak is indicated. In this event a registered
local heating installer should be consulted.
WARNING.
Do not fire the boiler if the pressure has reduced to zero from
the original setting.
9. After installation, commissioning and customer hand-over
please complete the
appliance log book and
leave this with the customer. For IE it is necessary to
complete a “Declaration of Conformity” to indicate
compliance to I.S. 813:2002
10. IMPORTANT
A comprehensive service should be carried out ANNUALLY.
Stress the importance of regular servicing by a CORGI
registered installer. In IE servicing work must be carried out
by a competent person.
11. As the installer you may wish to undertake the service
contract yourself or alternatively offer to the customer the
benefits of the Ideal Care Scheme, details of which are
outlined in the householder pack supplied with this boiler.
1. Hand the User Instructions to the householder and
explain his/her responsibilities under the relevant
national regulations.
2. Explain and demonstrate the lighting and shutting
down procedures.
3. The operation of the boiler and the use and adjustment
of all system controls should be fully explained to the
householder, to ensure the greatest possible fuel
economy consistent with the household requirements of
both heating and hot water consumption.
Advise the User of the precautions necessary to prevent
damage to the system and to the building, in the event
of the system remaining inoperative during frosty
conditions.
4. Explain the function and the use of the boiler heating
and domestic hot water controls.
5. Explain the function of the boiler fault mode.
Emphasise that if a fault is indicated, the boiler should
be turned off and a CORGI registered local heating
installer consulted. In IE contact a competent person.
6. Explain and demonstrate the function of time and
temperature controls, radiator valves etc., for the
economic use of the system.
After completing the installation and commissioning of the system the
installer should hand over to the householder by the following actions:
SER
VICING