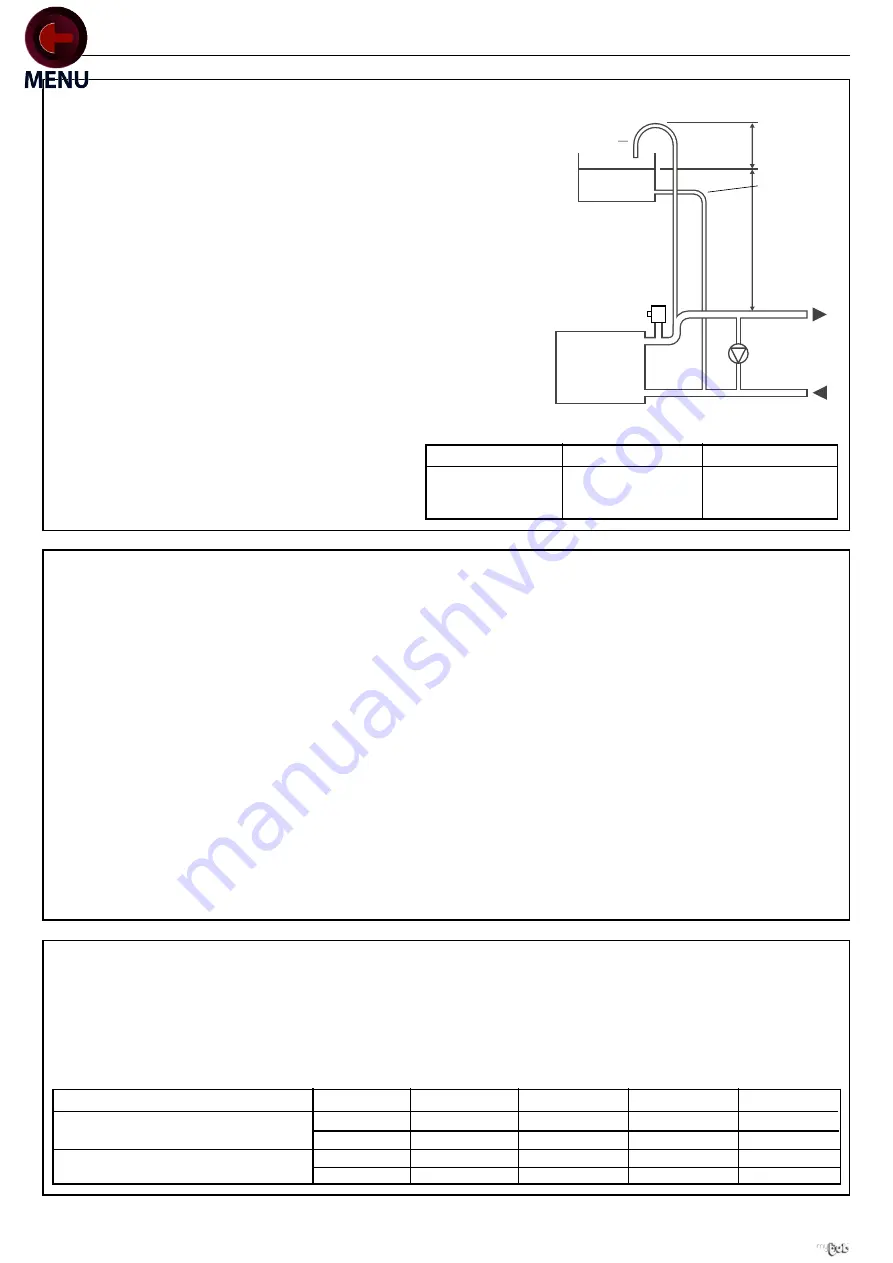
8
Harrier GTE -
Installation & Servicing
GENERAL
7
SEALED (PRESSURISED) SYSTEMS
6
OPEN VENTED SYSTEM REQUIREMENTS - minimum static head requirements
The Harrier GTE boiler has a minimum static head requirement of
2.5 metres (8 feet approx.) depending on the particular
characteristics of the system design (see diagram). The
information provided is based on the following assumptions.
1. An open vent/safety pipe connection is made immediately after
the flow connection.
2. A cold feed/expansion pipe connection is made to the system
return pipe within 0.75m of the boiler return connection.
3. The maximum flow rate through the boiler is based on a
temperature difference of 11ºC (20ºF) at full boiler output with
the circulating pump positioned in the flow of the system.
4. The boiler is at the highest point of the system. Systems
designed to rise above the flow connections will, of course,
automatically require a minimum static head higher than
shown.
5. The position of the open vent/safety pipe above the expansion
cistern water level is given as a guide only. The final position
will depend upon particular characteristics of the system.
Pumping over of water into the expansion cistern should
be avoided.
6. Both open vent/safety pipe and cold feed/expansion
pipes must be of adequate diameter to suit the output of
the boiler (see table below).
Working pressure 6 bar maximum.
Particular reference should be made to BS. 6644: Section 2;
Subsection 11 and Guidance note PM5 "Automatically
controlled steam and hot water boilers" published by the
Health and Safety Executive.
The information and guidance given below is not intended to
override any requirements of either of the above publications
or the requirements of the local authority, as or water
undertakings.
In general commercial closed pressurised systems are
provided with either manual or automatic water make up.
In both instances it will be necessary to fit automatic controls
intended to protect the boiler, circulating system and ancillary
equipment by shutting down the boiler plant if a potentially
hazardous situation should arise.
Examples of such situations are low water level and operating
pressure or excessive pressure within the system.
Depending on circumstances, controls will need to be either
manual or automatic reset. In the event of a shutdown both
visual and audible alarms may be necessary.
Open vent
safety pipe
750mm
Cold feed/
expansion pipe
H = 2.5m
To
pump
Pressure
relief
valve
FLOW
RETURN
Shunt pump
(if required)
Note: Height, H, MUST be
increased if necessary to
comply with the min.
head required by the
pump manufacturer
BOILER
This diagram does not show safety valves & water
flow switches etc necessary for safe operation
Expansion
cistern
har5966
Expansion vessels used must comply with BS. 4814 and must
be sized on the basis of the total system volume and initial
charge pressure.
Initial minimum charge pressure should not be less than 0.5
bar (7.2psi) and must take account of the static head and
specification of the pressurising equipment. The maximum
water temperatures permissible at the point of minimum
pressure in the system are specified in Guidance Note PM5.
When make up water is not provided automatically it will be
necessary to fit controls which shut down the plant in the event
of the maximum system pressure approaching to within
0.35bar (5psi) of the safety valve setting.
Other British Standards applicable to commercial sealed
systems are:
BS. 6880: Part 2
BS. 1212
BS. 6281: Part 1
BS. 6282: Part 1
BS. 6283: Part 4
8
SYSTEM DESIGN
Minimum Water Flow
Design Flow Rates
The following table gives the flow rate required for each boiler
based on a design temperature difference of 11ºC (20ºF) at the
maximum rated output. For hydraulic resistance see
Performance Data table (page 2).
Minimum Flow Rates
It may be necessary to fit a shunt pump to ensure minimum
flow rates.
Boiler Output kW
Open Vent (mm)
Cold Feed (mm)
60 to 150
32
25
151 to 300
38
32
301 to 600
50
38
Boiler Size
GTE 5
GTE 6
GTE 7
GTE 8
GTE 9
Normal water flow rate
l/s
3.04
3.91
5.00
6.08
7.17
temperature difference 11ºC (20ºF)
g.p.m.
40.1
51.6
66.0
80.2
94.6
Minimum water flow rate
l/s
0.96
1.23
1.57
1.91
2.25
temperature difference 35ºC (63ºF) g.p.m.
12.7
16.2
20.7
25.2
29.7
For latest prices and delivery to your door visit MyTub Ltd - 0845 303 8383 - www.mytub.co.uk - [email protected]