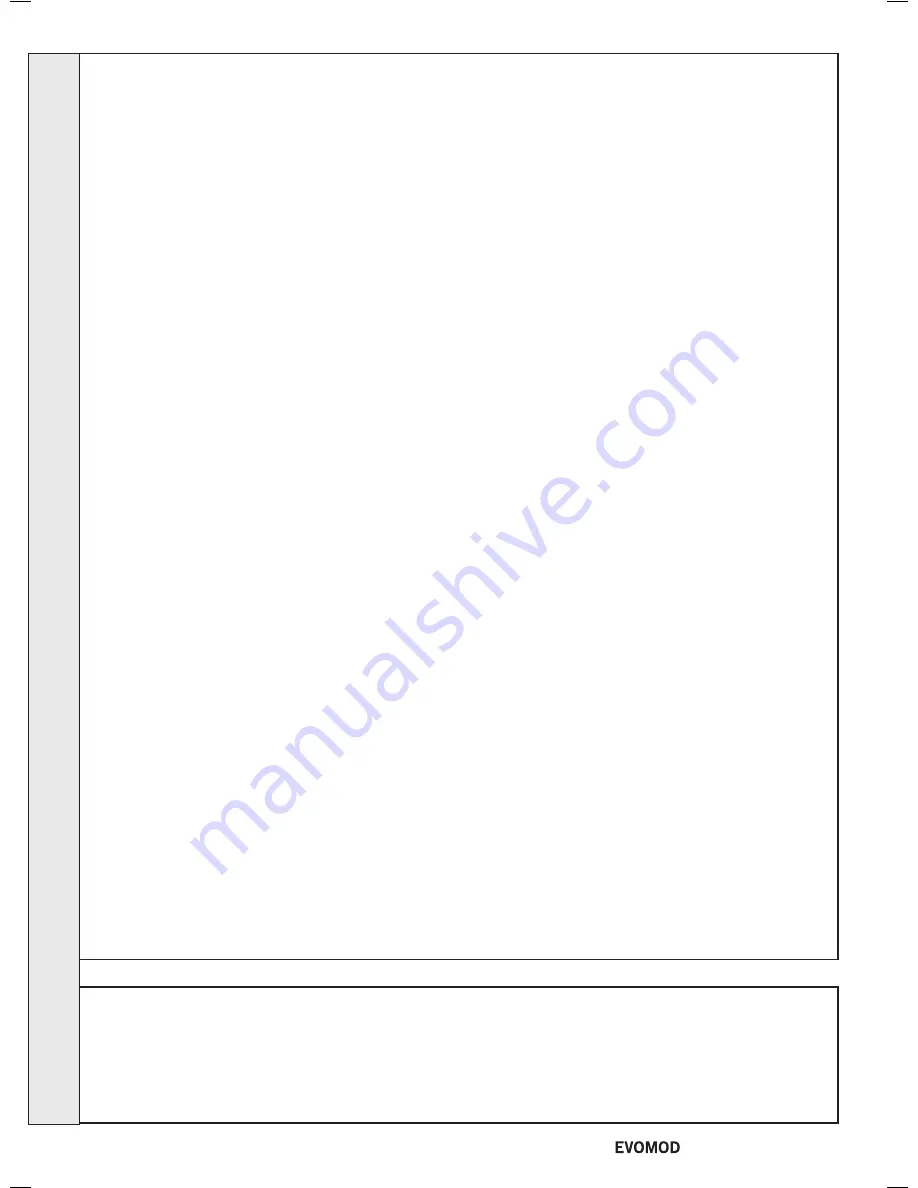
18 FROST PROTECTION
The boiler has built into its control system the facility to protect
the boiler only against freezing.
If the flow temperature falls below 5
o
C the boiler will fire until the
flow temperature exceeds 19
o
C. The pump will stay running for
a further 2 minutes.
Central heating systems fitted wholly inside the building do
not normally require frost protection as the building acts as
a 'storage heater' and can normally be left at least 24 hours
without frost damage. However, if parts of the pipework run
outside the building or if the boiler will be left off for more than a
day or so, then frost protection for the system is recommended.
AIR INLET
Combustion air can be drawn in via the grille situated on the top of boiler assembly or ducted in from outside of the building in
which the boiler is installed using the air inlet kit.
IMPORTANT NOTE. If combustion air is drawn from within the boiler room, ensure no dust or airborne debris can be
ingested into the appliance. Dusty concrete flooring should be sealed to reduce the presence of dust. Ideally where
possible duct the air supply into the boiler room from a clean source outside the boiler room/building.
An air inlet collar kit is available as an optional extra for fitting to the boiler.
1000kW
(note - refer to diagrams in Frame 16 for reference)
1. Assemble the 2 pairs of flue manifold T pieces (long legs
point upwards), ensuring the seals are fitted and lubricated
using the seal lubricant provided.
2. Push the assembled T pieces into the boiler connections
ensuring the seals are fitted and lubricated using the seal
lubricant provided.
3. Unpack and position the first header assembly at the rear
of the right hand modules, when viewed from the back.
4. Use the adjustable feet to both level the unit and
position the unions adjacent to their respective module
connections.
5. Connect each header flow & return flexible hose
connection to the appropriate module male thread
using the fibre washer provided. Note: A number of
adjustments are available within the header assembly to
help align connections. These must be secured after any
adjustments.
6. Connect each flexible gas header pipe to the appropriate
module male thread. Note: A number of adjustments
are available within the header assembly to help
align connections. These must be secured after any
adjustments.
7. Unpack the second header assembly. Remove any
blanking plates from the side to mate with the first header
assembly. Remove the flue header support frame by
removing the 6 nuts and bolts. Position the header
assembly at the rear of the left hand modules, when
viewed from the back.
8. Use the adjustable feet to level the unit, position the unions
adjacent to their respective module connections and align
with the adjacent header.
9. Bolt the 5” flow & return headers pipes of the 2 header
assemblies together using the gaskets and fasteners
provided.
10. Connect each header flow & return flexible hose
connection to the appropriate module male thread
using the fibre washer provided. Note: A number of
adjustments are available within the header assembly to
help align connections. These must be secured after any
adjustments.
11. Connect each flexible gas header pipe to the appropriate
module male thread. Note: A number of adjustments
are available within the header assembly to help
align connections. These must be secured after any
adjustments.
12. Refit the flue header support frame using the 6 nuts and
bolts.
13. Secure the flue manifolds to the header frames with the 4
support brackets provided. Note: The frame that supports
the flue manifold & gas header can move forwards or
backwards for adjustment.
14. Fit the bottom caps to the flue manifolds & secure with the
locking bands provided. Use locking bands to secure the
flue manifold T pieces together. Note: The bottom caps
must be connected to a drain via water traps using plastic
components only.
15. Assemble the 2 flue elbows to the Y piece ensuring the
seals are fitted and lubricated using the seal lubricant
provided. Fit this assembly to combine the outlets of the 2
flue manifolds. Secure using the locking bands provided.
16. An air vent point is provided in the top of both flow
headers. An automatic air vent must be fitted to the boss
nearest the end from which the water flow will be taken.
17. If the header kit used includes isolation valves, a pressure
relief valve MUST be fitted to the 1” boss provided on the
flexible flow pipe of each module.
18. A 1” boss is provided on the underside of the flexible
return pipe to enable a drain valve to be fitted. Remove
any blanking plates from the side to mate with the second
header assembly.
19. The header thermistor MUST be fitted to the boss provided
on the header flow pipe nearest to the end from which the
flow water will be taken.
20. Link the 2 vertical gas headers using the gas manifold
provided
INST
ALLA
TION
17 CONT'D WATER AND GAS HEADER INSTALLATION
20
-
Installation & Servicing
INSTALLATION
Содержание EVOMOD 250
Страница 59: ...59 Installation Servicing NOTES...
Страница 60: ...60 Installation Servicing NOTES...
Страница 61: ...61 Installation Servicing NOTES...