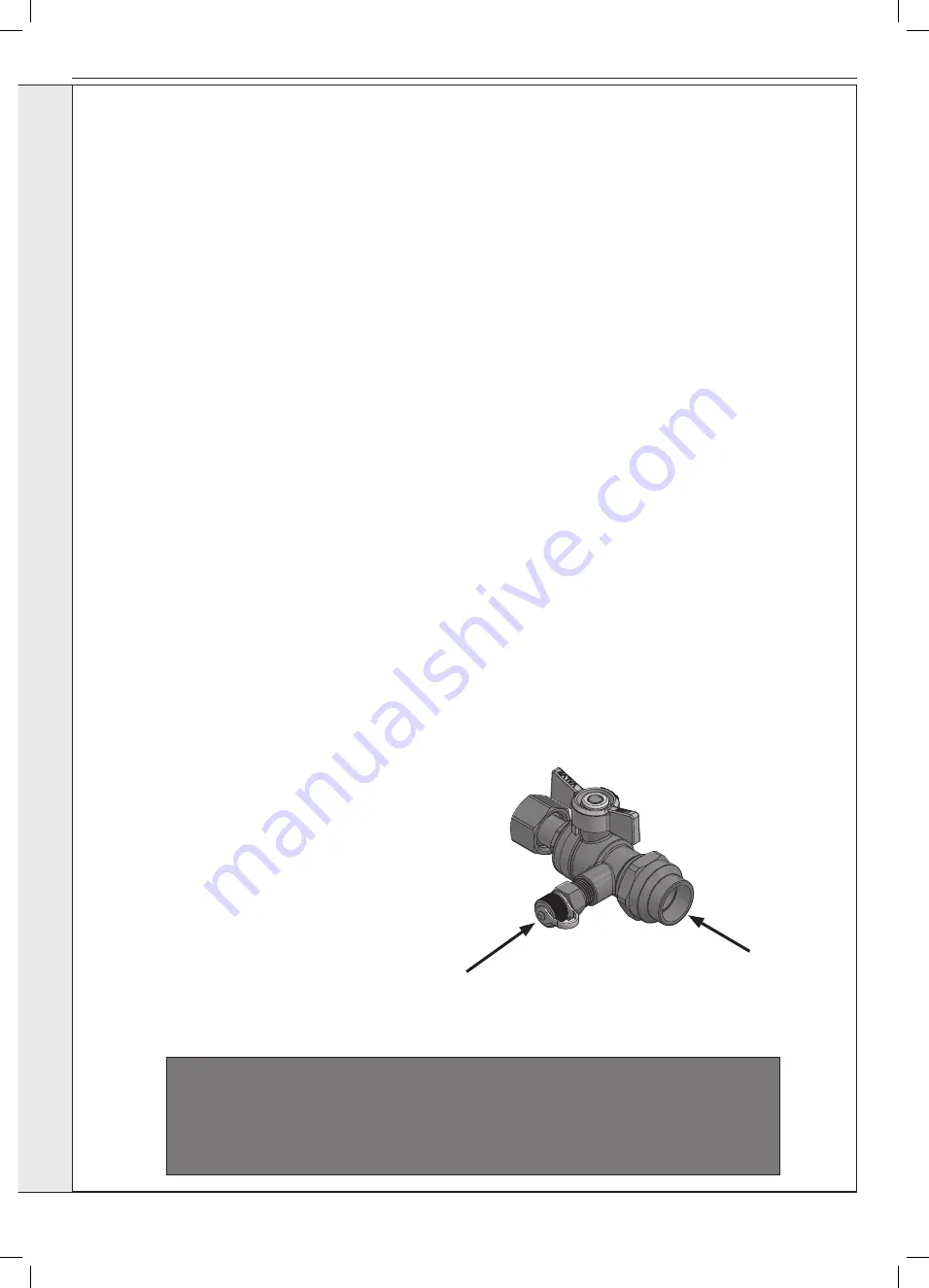
32
Installation and Servicing
SECTION 2 - INSTALLATION
WARNING.
Whilst effecting the required gas tightness test and purging air from the gas installation,
open all windows and doors if boiler is located indoors, extinguish naked lights and
DO NOT SMOKE.
A. Electrical Installation
1.
Checks to ensure electrical safety should be carried out by a
competent person.
2.
ALWAYS carry out the preliminary electrical system checks,
i.e. earth continuity, polarity, resistance to earth and short
circuit, using a suitable test meter.
3.
After wiring the boiler, all grommets in the bottom panel
MUST be in place to ensure that the boiler case sealing is
maintained.
B. Gas Installation
1.
The whole of the gas installation, including the meter,
should be inspected and tested for tightness and purged in
accordance with the recommendations of AS/NZS 5601.
2.
Purge air from the gas installation by the approved
methods only.
2.24 COMMISSIONING AND TESTING
GENERAL
Please Note
: The combustion for this appliance has
been checked, adjusted and preset at the factory for
operation on the gas type defined on the appliance
data plate.
DO NOT
adjust the air/gas ratio valve.
Having checked:
- That the boiler has been installed in accordance
with these instructions.
- The integrity of the flue system and the flue seals,
as described in the Flue Installation Section.
Proceed to put the boiler into operation as follows:
CHECK THE OPERATIONAL (WORKING) GAS
INLET PRESSURE
Set up the boiler to operate at maximum rate.
With the boiler operating in the maximum rate
condition check that the operational (working) gas
pressure at the inlet gas pressure test point complies
with the requirements - refer to “Gas Supply” on Page
8.
Ensure that this inlet pressure can be obtained with all
other gas appliances in the property working.
ATTENTION !
IT IS A CONDITION OF THE MANUFACTURERS WARRANTY THAT THE
COMMISSIONING CHECKLIST IS FULLY COMPLETED
AND LEFT WITH THE APPLIANCE
As part of the commissioning process, the combustion of this appliance must be checked
and the Checklist completed. A flow chart to assist is provided on Page 63.
Inlet from Gas Meter
Pressure Test Point
Outlet
attach to the
appliance
Turn 90° until
horizontal to isolate
gas to the appliance
INST
ALLA
TION
Содержание LOGIC+ SYSTEM S18
Страница 2: ...2 Installation and Servicing...
Страница 61: ...61 Installation and Servicing...
Страница 72: ......