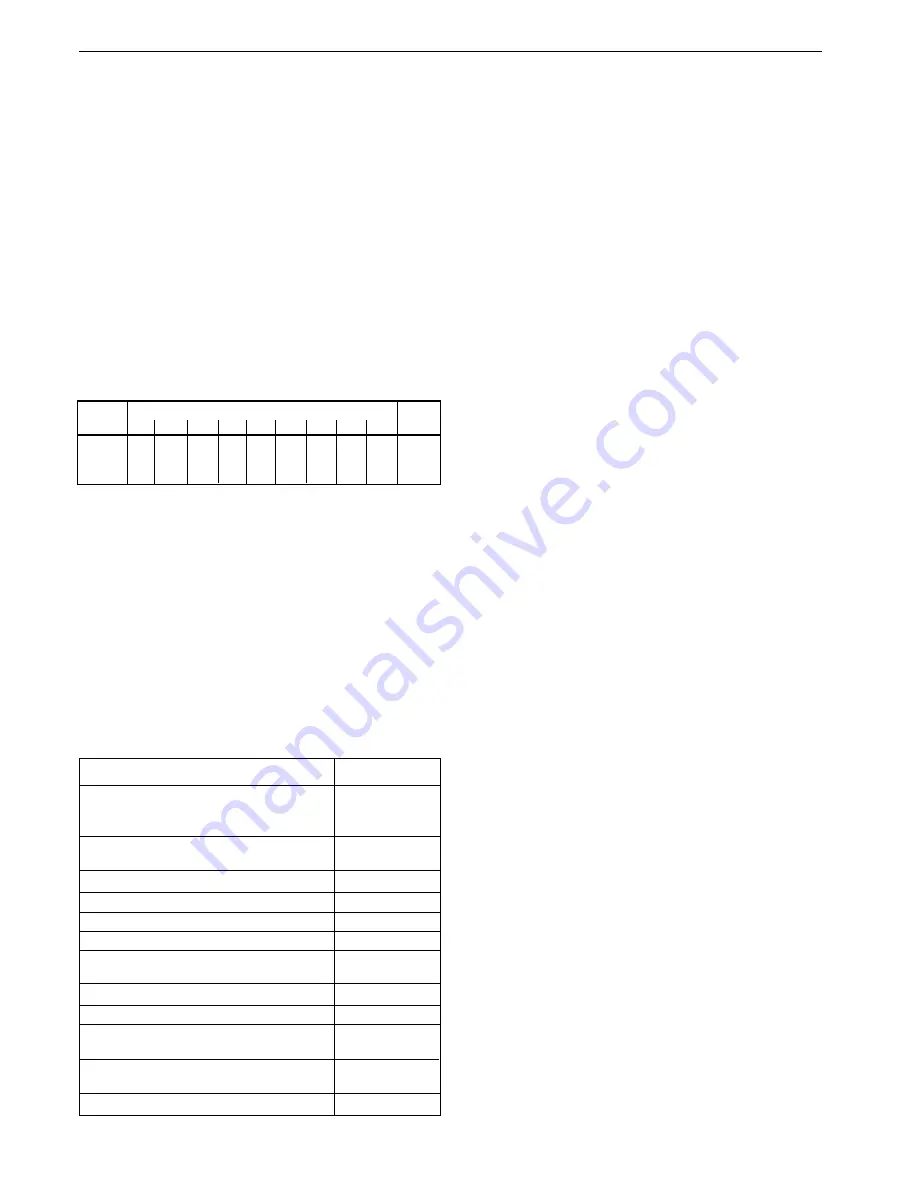
8
Response 80 / 100 / 120
- Installation
Terminal Position
Minimum Spacing
1.
Directly below or alongside an
opening window, air vent or other
ventilation opening
300 mm (12")
2.
Below guttering, drain pipes or soil
pipes
25 mm
( 1")
3.
Below eaves
25 mm
( 1")
4.
Below balconies or a car port roof
25 mm
( 1")
5.
From vertical drain pipes or soil pipes
25 mm
( 1")
6.
From internal or external corners
25 mm
( 1")
7.
Above adjacent ground, roof or
balcony level
300 mm (12")
8.
From a surface facing the terminal
600 mm (24")
9.
From a terminal facing a terminal
1200 mm (48")
10. From an opening in a car port
(e.g. door or window) into dwelling
1200 mm (48")
11. Vertically from a terminal on the
same wall
1500 mm (60")
12. Horizontally from a terminal on the wall
300 mm (12")
GENERAL
GAS SUPPLY
The local gas supplier should be consulted, at the installation
planning stage, in order to establish the availability of an adequate
supply of gas. An existing service pipe must NOT be used without
prior consultation with the local gas supplier.
A gas meter can only be connected by the local gas supplier or
by a registered CORGI installer.
Check that the appliance is suitable for the proposed gas supply.
A working gas pressure of 20 mbar MUST be available at the
boiler inlet.
IMPORTANT.
Installation pipes MUST be fitted in accordance with BS. 6891.
Pipework from the meter to Response boilers MUST be of an
adequate size, i.e. not less than 22mm O.D. copper or
3/4" BSP iron.
The complete installation MUST be tested for gas soundness
and purged as described in the above code.
Table 6 - Balanced flue terminal position
Approved Manufacturer's Clearance
N.B.
These clearances are for horizontal flue only. For vertical
clearances see the publication for Pack K/Pack H.
Note (Positions 2-6)
: Due to the terminal design, installation
is possible with clearances less than those specified in BS
5440, Part 1.
Total length of supply pipe (metres)
Pipe size
9
12
15
20
25
35
40
45
50
(mm Dia.)
Gas
160 140
120
100
89
74.2 67.1 63.6
60
22
Discharge
ft
3
/ h
330 280
250
210 180 151.9 137.7 130.7 123.6
28
FLUE INSTALLATION
The flue must be installed in accordance with the
recommendations of BS. 5440: Part 1.
The following notes are intended for general guidance:
1. The boiler MUST be installed so that the terminal is
exposed to external air.
2. It is important that the position of the terminal allows the
free passage of air across it at all times.
3. Minimum acceptable spacing from the terminal to
obstructions and ventilation openings are specified in
Table 6.
4. Where the lowest part of the terminal is fitted less than 2m
(6'6") above a balcony, above ground or above a flat roof to
which people have access then the terminal MUST be
protected by a purpose designed guard. The minimum
spacing in Table 6, Nos. 2, 3, 4, 5 and 6 would be 75mm, in
order to allow a terminal guard to be fitted.
Terminals guards are available from boiler suppliers - ask
for TFC Guard, Model K1. In case of difficulty contact:
Grasslin (UK) Ltd., Tower House, Vale Rise, Tonbridge,
Kent TN9 1TB. Tel: 01732 359888. Fax: 01732 354445.
www.ffc.ukco.com
Ensure that the guard is fitted centrally.
5. The flue assembly shall be so placed or shielded as to
prevent ignition or damage to any part of any building.
6. The air inlet/products outlet duct and the terminal of the
boiler MUST NOT be closer than 25mm (1") to combustible
material. Detailed recommendations on the protection of
combustible material are given in BS. 5440: 1990.
7. Where it is essential that the terminal wall plate
is fitted, i.e.
wall thicknesses over 610mm (24") or with an inaccurately
cut hole, the minimum spacing in Table 6, Nos. 2, 3, 4, 5
and 6 would be 60mm (2.4") in order to allow the terminal
wall plate to be fitted.
IMPORTANT. It is the responsibility of the installer to ensure, in
practice, that products of combustion discharging from the
terminal cannot re-enter the building or any other adjacent
building through ventilators, windows, doors, other sources of
natural air infiltration, or forced ventilation / air conditioning.
If this should occur the appliance MUST be turned OFF,
labelled as 'unsafe' until corrective action can be taken.
FLUE LENGTHS
The flue assembly can be adapted to accommodate flue
lengths up to 3 metres for the 80 and up to 4m for the 100 and
120. Refer to Frame 10.
WATER CIRCULATION SYSTEM
The boilers are designed for connection to pressurised, fully
pumped, sealed water central heating systems ONLY. The
domestic hot water (DHW) calorifier is incorporated within the
heat exchanger and only requires connection to the mains
water supply.
IMPORTANT.
Copper tubing to BS2871:1 MUST be used throughout the
heating and domestic hot water systems.
Table 5 - Gas Supply
Note.
Each fitting used in the gas line from the meter is equivalent
to a length of straight pipe which must be added to the straight
pipe length to give the total length. i.e.: bend = 0.5 metres, Tee =
0.5 metres, 90
o
elbow = 0.3 metres.
Содержание responce 80
Страница 1: ......
Страница 61: ...61 Response 80 100 120 Installation 89 SHORT PARTS LIST 90 BOILER CASING ASSEMBLY SHORT LIST OF PARTS Res 5972...
Страница 62: ...62 Response 80 100 120 Installation NOTES...
Страница 63: ...63 Response 80 100 120 Installation NOTES...