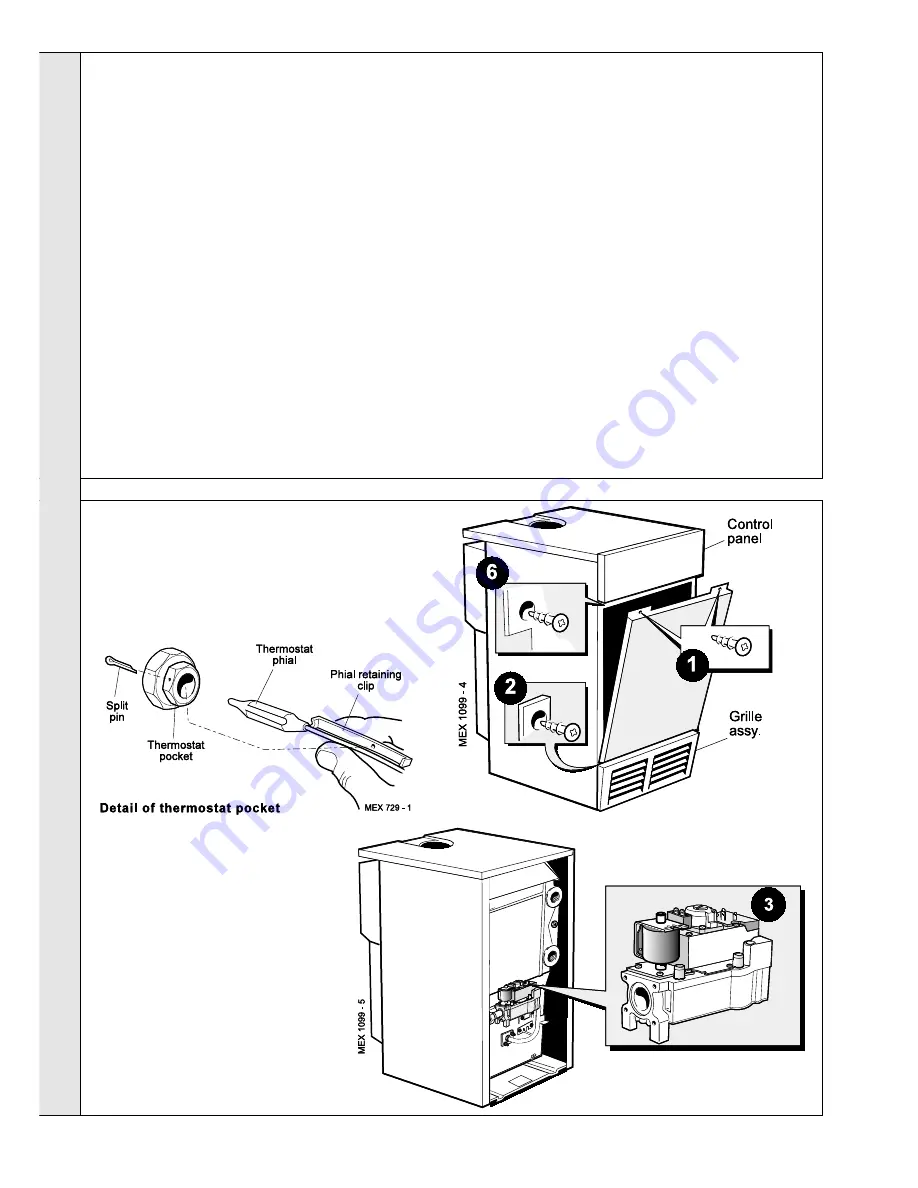
30
Mexico Super 100 FF & 125 FF -
Installation
56 SCHEDULE
SERVICING
WARNING.
BEFORE SERVICING
always turn OFF the gas supply at the
gas service cock and switch OFF and DISCONNECT the
electrical supply to the appliance.
To ensure the continued safe and efficient operation of the
appliance it is recommended that it is checked at regular
intervals and serviced as necessary. The frequency of
servicing will depend upon the installation condition and
usage but should be carried out at least annually .
It is the law that any service work must be carried out by a
CORGI registered installer.
a.
Light the boiler and carry out a pre-service check, noting
any operational faults.
b.
Operate the boiler for at least 20 minutes. Check the gas
consumption.
c.
Connect a suitable gas analyser to the sampling point on
the flue collector. Refer to Frame 60.
For correct operation the CO/CO
2
content of the flue gas
should not be greater than 0.004 ratio. If this is the case
and the gas input is within 95% of the nominal then no
further action need be taken. If not the case, proceed to
step (d)
d.
Clean the main burner.
e.
Clean the heat exchanger.
f.
Clean the main injectors.
g.
Check that the flue terminal is unobstructed and that the
flue system is sealed correctly.
h.
If the appliance has been installed in a compartment, check
that the ventilation areas are clear.
a.
Light the boiler and
carry out a pre-service check, noting any operational faults.
The servicing procedures are covered more fully in Frames
58 to 62 and MUST be carried out in sequence.
Note.
In order to carry out either servicing or replacement of
components, the boiler casing must removed. Refer to
Frame 57.
IMPORTANT.
After completing the servicing or exchange of
components always test for gas soundness and carry out
functional checks as appropriate.
When the work is complete the casing MUST be correctly
refitted and secured.
The boiler must NOT be operated if the casing is not fitted.
57 BOILER CASING REMOVAL
1.
Remove the 2 screws and lift off the lower front panel.
2.
Remove the 2 screws and lift off the grille assembly.
3.
Disconnect the electrical leads from the gas valve.
4.
Disconnect the in-line connector on the PCB box lead.
5.
Remove the thermostat phial
from the pocket as shown.
6.
Remove the 2 screws securing
the control panel and pull down
to release the tabs from under
the top panel.
7.
If the boiler is not fitted under a
work top, access for flue cleaning
will be improved by removing the
top panel.
SER
VICING
Содержание Mexico Super 100 FF
Страница 1: ......
Страница 40: ...40 Mexico Super 100 FF 125 FF Installation LIST OF PARTS 76 SHORT PARTS ...
Страница 45: ...45 Mexico Super 100 FF 125 FF Installation ...