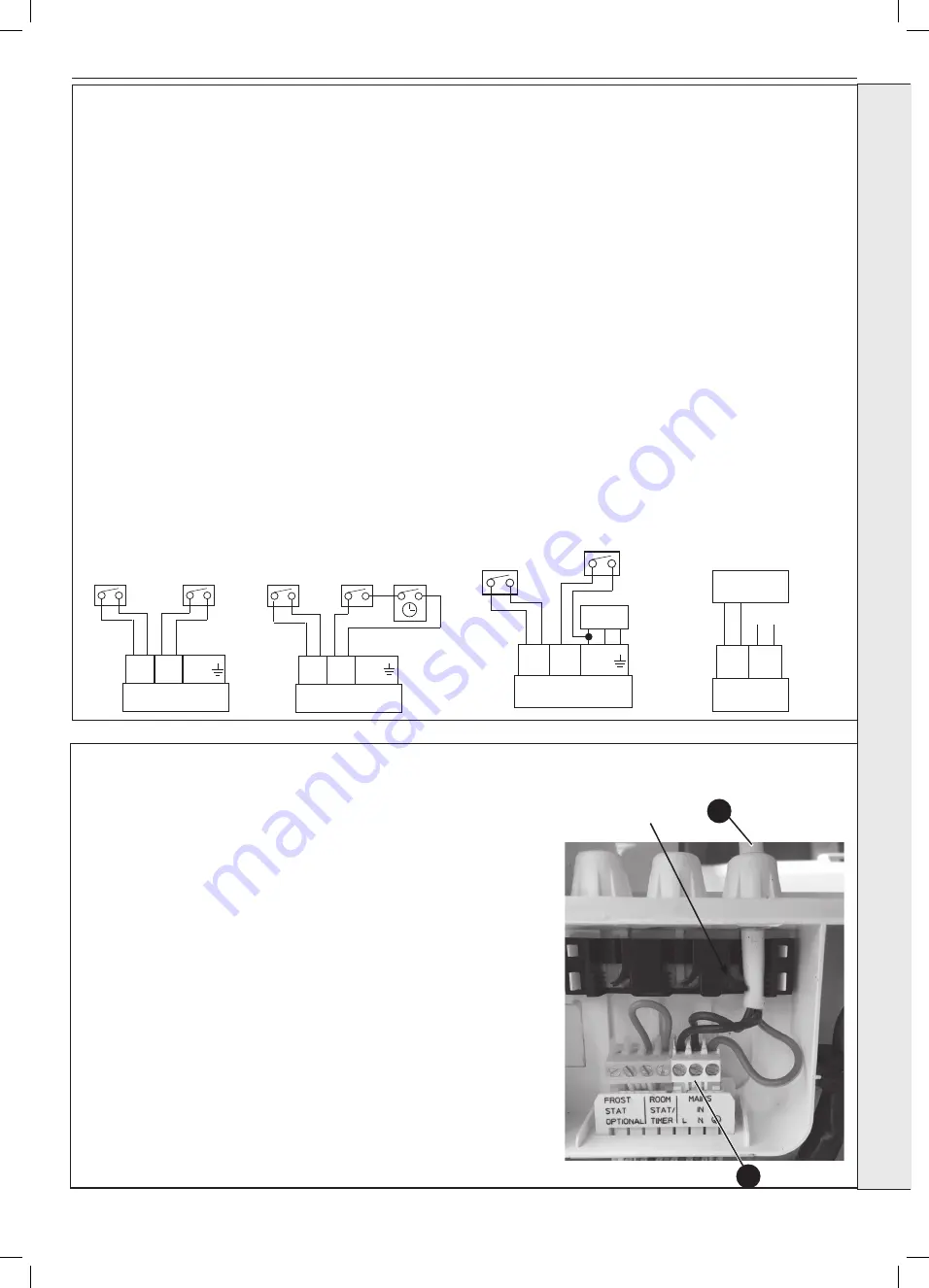
33
Installation and Servicing
SECTION 2 - INSTALLATION
2.20 REPLACING PRE-FITTED MAINS CABLE
If it is necessary to use an alternative mains cable to the one pre-fitted then use
the following guide.
Replacement wiring should comply with notes in Section 2.18 and be caried out
by a qualified person to avoid a hazard.
1.
Isolate the mains supply to the boiler.
2.
Remove the front panel. Refer to Section 3.2.
3.
Swing the control box down into the service position, unclip and swing back the
installer wiring cover to latch into the retaining clips. Refer to Section 3.8.
4.
Unplug the mains connector and release the cable from strain relief.
5.
Unscrew the L N & E connections & remove wires from connector.
6.
Remove the mains cable by pulling back through the grommet .
7.
Route the replacement cable through the grommet and re-fit in reverse order.
8.
Close the installer wiring cover ensuring that it is located correctly and that the
cable is retained into the strain relief as shown.
9.
Swing the control box back up into the operating position and re-fit the front
panel ensuring a good seal is made.
NOTE.
When making the mains electrical connections to the boiler it is important
that the wires are prepared in such a way that the earth conductor is longer than
the current carrying conductors, such that if the cord anchorage should slip, the
current carrying conductors become taut before the earthing conductor.
2.19 EXTERNAL WIRING
DIAGRAM A:
DIAGRAM B:
Room Stat with External Timer
Programmable Room Stat or
Room Stat with Internal Timer
Optional
Room Stat or
Optional
Frost
Programmable
Frost
Stat
Room Stat
Stat
Room Stat
Timer
Frost
Room
Frost
Room
Stat
Stat/
L N
Stat
Stat/
L N
(Optional)
Timer
(Optional)
Timer
DIAGRAM C:
Use of General Live for Room Stat
Optional
Room Stat
Frost
Stat
Mains In
Frost
Room
Stat
Stat/
L N
(Optional)
Timer
DIAGRAM A:
DIAGRAM B:
Room Stat with External Timer
Programmable Room Stat or
Room Stat with Internal Timer
Optional
Room Stat or
Optional
Frost
Programmable
Frost
Stat
Room Stat
Stat
Room Stat
Timer
Frost
Room
Frost
Room
Stat
Stat/
L N
Stat
Stat/
L N
(Optional)
Timer
(Optional)
Timer
DIAGRAM C:
Use of General Live for Room Stat
Optional
Room Stat
Frost
Stat
Mains In
Frost
Room
Stat
Stat/
L N
(Optional)
Timer
DIAGRAM A:
DIAGRAM B:
Room Stat with External Timer
Programmable Room Stat or
Room Stat with Internal Timer
Optional
Room Stat or
Optional
Frost
Programmable
Frost
Stat
Room Stat
Stat
Room Stat
Timer
Frost
Room
Frost
Room
Stat
Stat/
L N
Stat
Stat/
L N
(Optional)
Timer
(Optional)
Timer
DIAGRAM C:
Use of General Live for Room Stat
Optional
Room Stat
Frost
Stat
Mains In
Frost
Room
Stat
Stat/
L N
(Optional)
Timer
DIAGRAM D:
OpenTherm Device
DO NOT CONNECT 230V TO THESE
TERMINALS OR THE BOILER ELECTRONICS
WILL BE DAMAGED
Outside
Sensor
Open
Therm
OpenTherm Device
E.G. Honeywell OT
Bridge R8810
Strain Relief
External Controls – 230V 50Hz
Wiring a 230V 50Hz Room Thermostat,
Diagram A (with optional timer, Diagram B)
1. Remove the link wire from the room
stat/timer plug.
2. Connect the external cable from
the room stat/timer across these
two connections, if a general live
connection is used for the room stat
or timer then connect this to the
fused spur, on the load side (see
Diagram C)
3. If the room thermostat has
compensation and requires a neutral
connection, make this connection to
the fused spur, on the load side.
Optional External Controls – Extra Low
Voltage
Wiring OpenTherm Room Control or other
OpenTherm Master Device, Diagram D.
1. Locate the OpenTherm connection on
the right hand side of the boiler installer
connections area, remove the violet link
wire and connect the 2 core cable from
the OpenTherm device.
Frost Protection
If parts of the pipework run outside the
house or if the boiler will be left off for more
than a day or so then a frost thermostat
should be wired into the system.
This is usually done at the programmer, in
which case the programmer selector switches
are set to OFF and all the other controls
MUST be left in the running position.
The frost thermostat should be sited in a
cold place but where it can sense heat
from the system.
Wiring a system frost thermostat, see
digarams A, B and C. Wire the frost
thermostat across the two connections as
shown.
Note
.
If the boiler is installed in a garage it
may be necessary to fit a pipe thermostat,
preferably on the return pipework.
6
4
INST
ALLA
TION
Содержание LOGIC COMBI C24IE
Страница 4: ...4 Installation and Servicing...
Страница 6: ...6 Installation and Servicing...
Страница 62: ...62 Installation and Servicing SECTION 6 BENCHMARK COMMISSIONING...
Страница 68: ...68 NOTES Installation and Servicing...
Страница 69: ...69 NOTES Installation and Servicing...
Страница 70: ...70 NOTES Installation and Servicing...
Страница 71: ...71 NOTES Installation and Servicing...