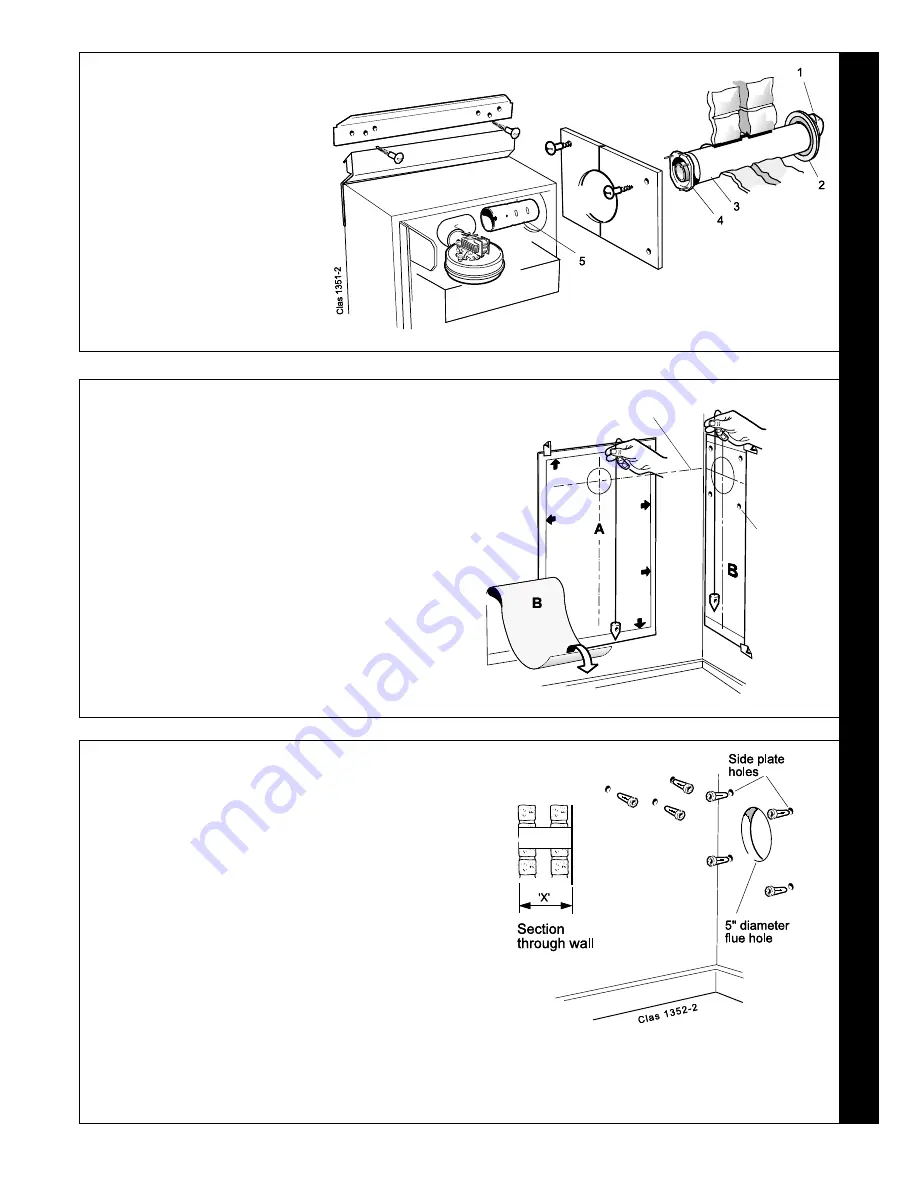
17
INSTALLATION
Classic
Slimline FF
-
Installation & Servicing
SIDE FLUE OUTLET
Extended centre
line
Terminal
mounting
plate screw
and flue
duct hole
positions
1. An optional flue duct
extension kit is required
for lengths (distance from
the outside wall to the
relevant side of the boiler
casing) greater than
600mm (23
1/2
") Refer to
Frame 10.
2. When cutting the ducts
always use the cardboard
support provided.
21 FLUE ASSEMBLY - Exploded view
For wall thickness 114mm to 600mm
IMPORTANT. Ensure that, during the cutting operation, masonry
falling outside of the building does not cause damage or
personal injury.
1. Cut the flue hole, preferably with a 125mm (5") core boring
tool, ensuring that the hole is square to the wall. If the hole
has been accurately cut with a drill then making good the wall
faces is not essential as seals are provided at both ends of
the flue. However, both wall faces immediately around the cut
hole should be flat; make good if necessary. For less accurate
holes make good to approximately 125mm (5") diameter at
the 2 wall faces.
2. Drill 2 holes with an 8mm (
5/16
") masonry drill and insert the
plastic plugs provided, for the wall mounting plate.
3. Drill 1 further hole below the wall plate fixing screws, in the
position shown on the template, for boiler fixing with the same
8mm (
5/16
") masonry drill and insert the plastic plug provided.
4. Drill 4 holes with a 7mm (
9/32
") masonry drill and insert the
plastic plugs provided, for the side mounting plate.
22 WALL MOUNTING TEMPLATE
1. Separate the templates.
2. Tape both templates into the selected position locating
template B through an extended centre line as shown.
3. Ensure squareness by hanging a plumb line as shown.
4. Mark onto the wall (if required) the following:
a. The 4 wall mounting plate screw positions (choose one
from each group).
b. The 4 screw positions for the side outlet plate.
c. The position of the flue duct hole.
Note.
Mark the centre of
the hole as well as the circumference.
d. The side of the casing nearest the flue outlet.
5. Remove both templates from the wall.
LEGEND
1.
Terminal
2.
Weather sea
3.
Flue assembly
4.
Boiler sealing plate
5.
Flue extension tube
23 PREPARING THE WALL
Note.
If the terminal is to be sited within 25-40mm of a corner
or vertical pipe (refer to Table 3) then the hole MUST be
accurately cut and the rubber weather seal trimmed around
the groove provided. The terminal wall plate need not be
fitted.
Содержание Classic FF 360
Страница 1: ......
Страница 39: ...Classic Slimline FF Installation Servicing 39 NOTES...