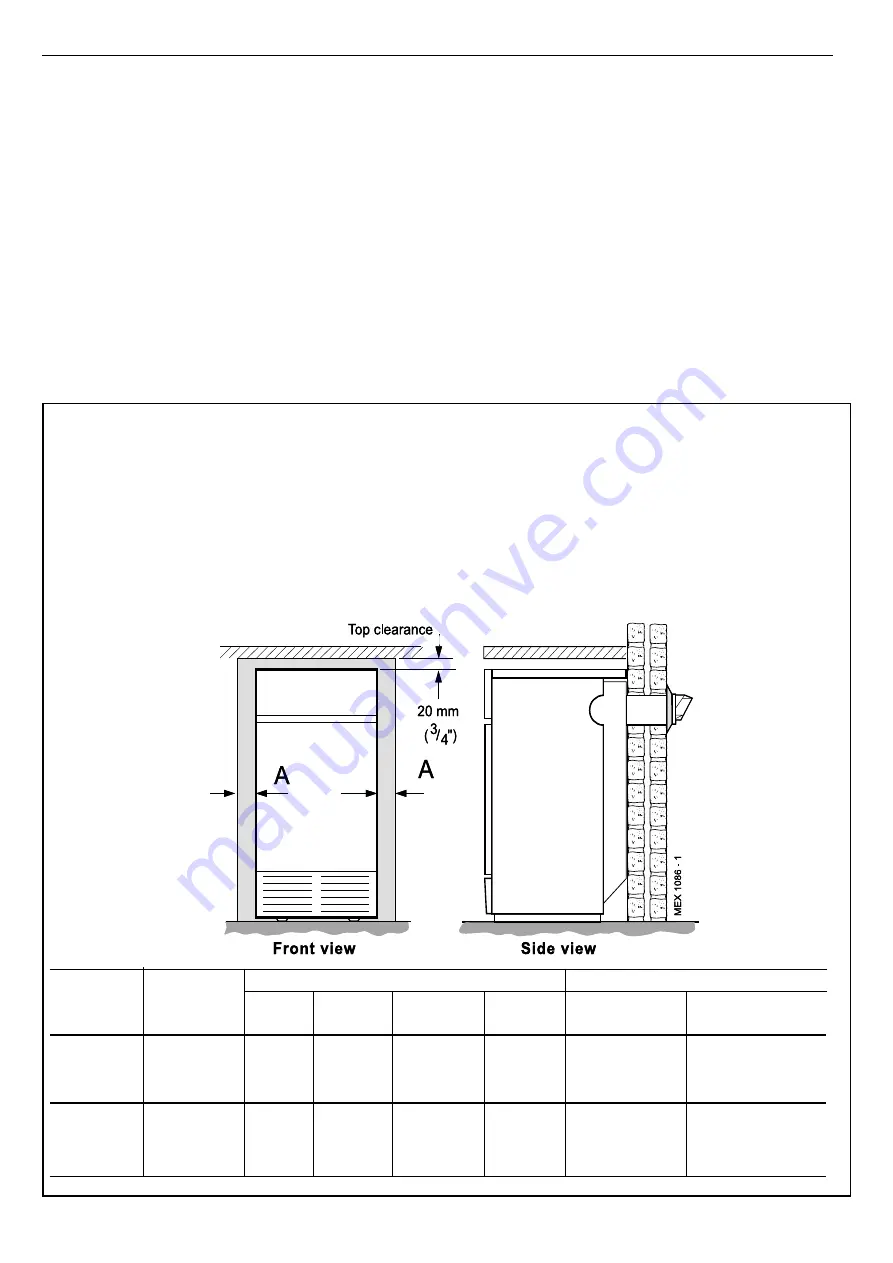
6
British Gas 40 - 80 RD2 -
Installation & Servicing
GENERAL
Bathrooms
The boiler may be installed in any room or internal space,
although particular attention is drawn to the requirements of the
current I.E.E. (BS 7671) Wiring Regulations and, in Scotland,
the electrical provisions of the building regulations applicable in
Scotland with respect to the installation of the boiler in a room or
internal space containing a bath or shower.
Where a room-sealed appliance is installed in a room containing
a bath or shower then the appliance and any electrical switch or
appliance control utilising mains electricity should be so situated
that it cannot be touched by a person using the bath or shower.
Where installation will be in an unusual location, special
procedures may be necessary and BS.6798 gives detailed
guidance on this aspect.
Compartment Installations
A compartment used to enclose the boiler MUST be designed
and constructed specially for this purpose.
An existing cupboard or compartment may be used, providing it
is modified for the purpose.
2 FLOOR MOUNTING AND BOILER CLEARANCES
Flammable materials must not be placed in close proximity to
the appliance. Materials giving off flammable vapours must
not be stored in the same room as the appliance.
Floor mounting
1.
The floor must be flat, level and of suitable load bearing
capacity.
2.
The back of the boiler may be fitted up to the wall.
Boiler clearances
The minimum overall dimensions of the space in which the
boiler is to operate and to facilitate servicing are as shown in
the Table.
Additional space will be required for installation, depending
upon site conditions.
IMPORTANT.
In order to facilitate gas connection, a clearance of at least
100 mm (4") must be available at either the left hand side or
the right hand side DURING installation. Refer to Frame 31.
In addition a MINIMUM clearance of 533 mm (21") MUST
be available at the front of the boiler, for servicing.
In both cases details of essential features of cupboards/
compartment design, including airing cupboard installation, are
to conform to the following:
z
z
z
z
z
BS. 6798.
z
z
z
z
z
The position selected for installation MUST allow
adequate space for servicing in front of the boiler
and for air circulation around the boiler.
Side clearance is only necessary for installation. The amount
of side clearance will depend upon the type of connection
used.
z
This position MUST also permit the provision of a
satisfactory flue termination.
z
For the minimum clearances required for safety, and
subsequent service, see Frame 2.
Boiler
Flue
Overall Space dimension
Minimum Side Clearance 'A'
Model
Length
Depth
Height
Width
Width
Rear Flue
Side/Top Flue
Rear Flue
Side/Top
40, 50,
114 to
533 mm
870 mm
460 mm
510 mm
10 mm
35 mm
60, 70
600 mm
(21")
(34
1/4"
)
(18
1/8"
)
(20
1/8"
)
(
3/8
")
(1
3/8
")
80
(
4
1/2"-
23
5/8")
40, 50,
600 to
533 mm
870 mm
510 mm
510 mm
35 mm
35 mm
60, 70
3000mm
(21")
(34
1/4"
)
(20
1/8"
)
(20
1/8"
)
(1
3/8
")
(1
3/8
")
80
(23
5/8"-
118
"
)