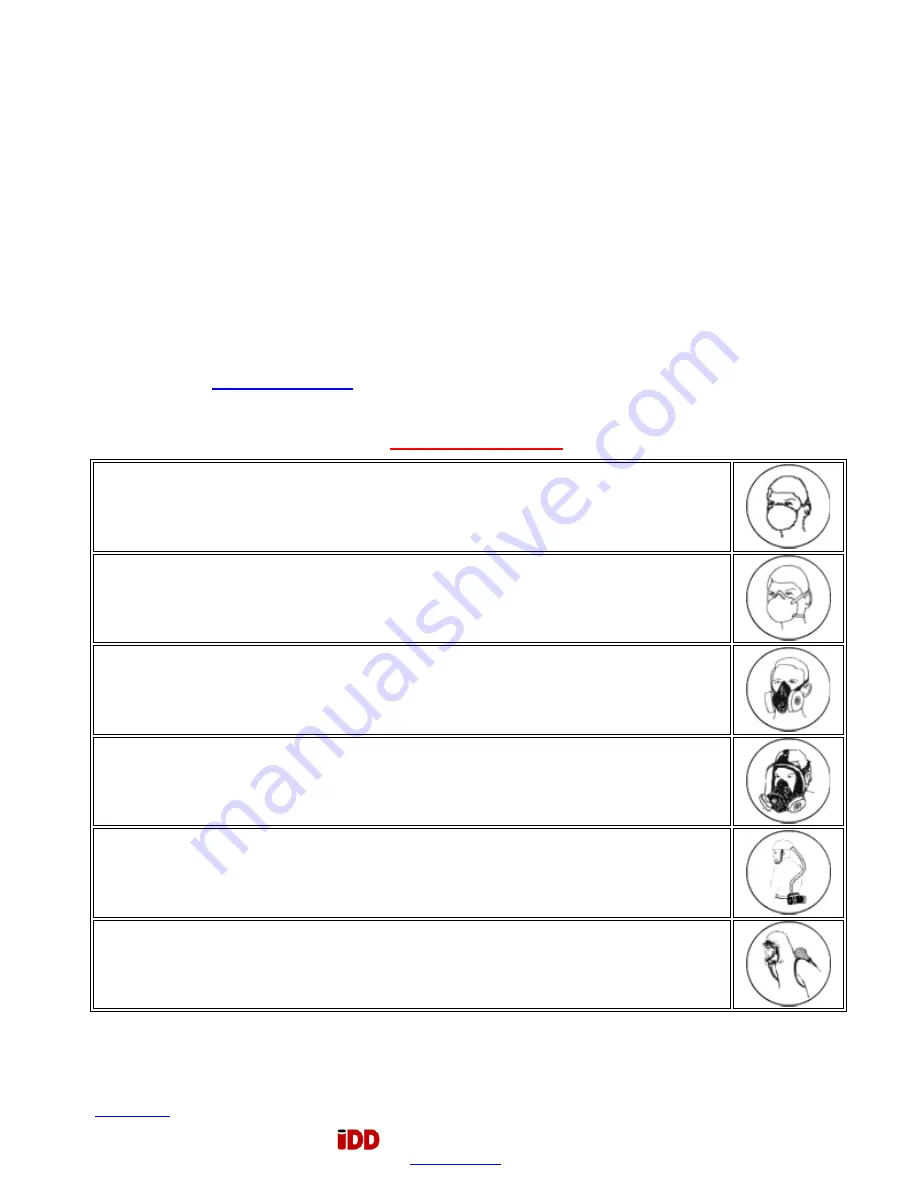
SQUIRE
PLUS
2
OPERATIONS
MANUAL
PROCESS & PACKAGING, INC.
P
AGE
125
OF
125
www.iddeas.com
Appx. D PROGRAM LISTING
Program
has been loaded into PLC and fully tested.
Appx. E TRAINING
On-
site
training is available from our technical staff at customer’s request.
Appx. F
WHICH MASK SHOULD I WEAR?
Respiratory protection must be worn whenever you are working in a hazardous atmosphere. The
appropriate respirator will depend on the contaminant(s) to which you are exposed and the
protection factor (PF) required. Respirators should be used whenever hazardous fumes are present,
as listed under
Respirator Types
.
As stated in
Section 4 – Safety
: The work area should have adequate ventilation as approved by
Safety Personnel.
R
ESPIRATOR
T
YPES
Single-strap dust masks
can be used for providing comfort from dirt, dust, pollen, or other
allergens. These are not NIOSH-approved and should never be used to protect from
hazardous atmospheres.
Approved filtering face pieces
(dust masks) can be used for dust, mists, welding fumes,
etc. They do not provide protection from gases or vapors. DO NOT USE FOR ASBESTOS
OR LEAD; instead, select from the respirators below.
Half-face respirators
can be used for protection against most vapors, acid gases, dust, or
welding fumes. Cartridges/filters must match contaminant(s) and be changed periodically.
Full-face respirators
are more protective than half-face respirators. They can also be used
for protection against most vapors, acid gases, dust, or welding fumes. The face-shield
protects face and eyes from irritants and contaminants. Cartridges/filters must match
contaminant(s) and be changed periodically.
Loose-fitting powered-air-purifying respirators
(PAPR) offer breathing comfort from a
battery-powered fan which pulls air through filters and circulates air throughout helmet/hood.
They can be worn by most workers who have beards. Cartridges/filters must match
contaminant(s) and be changed periodically.
A Self-Contained Breathing Apparatus
(SCBA) is used for entry and escape from
atmospheres that are considered immediately dangerous to life and health (IDLH), or are
oxygen deficient. They use their own air tank.
Back To TOC
Содержание SQUIRE PLUS 2
Страница 13: ...SQUIRE PLUS 2 OPERATIONS MANUAL PROCESS PACKAGING INC PAGE 13 OF 125 www iddeas com Back To TOC ...
Страница 47: ...SQUIRE PLUS 2 OPERATIONS MANUAL PROCESS PACKAGING INC PAGE 47 OF 125 www iddeas com ...
Страница 48: ...SQUIRE PLUS 2 OPERATIONS MANUAL PROCESS PACKAGING INC PAGE 48 OF 125 www iddeas com ...
Страница 49: ...SQUIRE PLUS 2 OPERATIONS MANUAL PROCESS PACKAGING INC PAGE 49 OF 125 www iddeas com ...
Страница 50: ...SQUIRE PLUS 2 OPERATIONS MANUAL PROCESS PACKAGING INC PAGE 50 OF 125 www iddeas com ...
Страница 51: ...SQUIRE PLUS 2 OPERATIONS MANUAL PROCESS PACKAGING INC PAGE 51 OF 125 www iddeas com Back To TOC ...
Страница 58: ...SQUIRE PLUS 2 OPERATIONS MANUAL PROCESS PACKAGING INC PAGE 58 OF 125 www iddeas com Functional Diagrams ...
Страница 60: ...SQUIRE PLUS 2 OPERATIONS MANUAL PROCESS PACKAGING INC PAGE 60 OF 125 www iddeas com PROCESS VALVE Back To TOC ...
Страница 61: ...SQUIRE PLUS 2 OPERATIONS MANUAL PROCESS PACKAGING INC PAGE 61 OF 125 www iddeas com SOLENOID VALVE Back To TOC ...
Страница 63: ...SQUIRE PLUS 2 OPERATIONS MANUAL PROCESS PACKAGING INC PAGE 63 OF 125 www iddeas com TANK DOSING UNIT ...
Страница 70: ...SQUIRE PLUS 2 OPERATIONS MANUAL PROCESS PACKAGING INC PAGE 70 OF 125 www iddeas com ...
Страница 71: ...SQUIRE PLUS 2 OPERATIONS MANUAL PROCESS PACKAGING INC PAGE 71 OF 125 www iddeas com ...
Страница 72: ...SQUIRE PLUS 2 OPERATIONS MANUAL PROCESS PACKAGING INC PAGE 72 OF 125 www iddeas com ...
Страница 73: ...SQUIRE PLUS 2 OPERATIONS MANUAL PROCESS PACKAGING INC PAGE 73 OF 125 www iddeas com ...
Страница 74: ...SQUIRE PLUS 2 OPERATIONS MANUAL PROCESS PACKAGING INC PAGE 74 OF 125 www iddeas com ...
Страница 75: ...SQUIRE PLUS 2 OPERATIONS MANUAL PROCESS PACKAGING INC PAGE 75 OF 125 www iddeas com ...
Страница 76: ...SQUIRE PLUS 2 OPERATIONS MANUAL PROCESS PACKAGING INC PAGE 76 OF 125 www iddeas com Back To TOC ...
Страница 78: ...SQUIRE PLUS 2 OPERATIONS MANUAL PROCESS PACKAGING INC PAGE 78 OF 125 www iddeas com ...
Страница 79: ...SQUIRE PLUS 2 OPERATIONS MANUAL PROCESS PACKAGING INC PAGE 79 OF 125 www iddeas com ...
Страница 80: ...SQUIRE PLUS 2 OPERATIONS MANUAL PROCESS PACKAGING INC PAGE 80 OF 125 www iddeas com ...
Страница 81: ...SQUIRE PLUS 2 OPERATIONS MANUAL PROCESS PACKAGING INC PAGE 81 OF 125 www iddeas com ...
Страница 82: ...SQUIRE PLUS 2 OPERATIONS MANUAL PROCESS PACKAGING INC PAGE 82 OF 125 www iddeas com ...
Страница 83: ...SQUIRE PLUS 2 OPERATIONS MANUAL PROCESS PACKAGING INC PAGE 83 OF 125 www iddeas com ...
Страница 84: ...SQUIRE PLUS 2 OPERATIONS MANUAL PROCESS PACKAGING INC PAGE 84 OF 125 www iddeas com ...
Страница 85: ...SQUIRE PLUS 2 OPERATIONS MANUAL PROCESS PACKAGING INC PAGE 85 OF 125 www iddeas com ...
Страница 86: ...SQUIRE PLUS 2 OPERATIONS MANUAL PROCESS PACKAGING INC PAGE 86 OF 125 www iddeas com ...
Страница 87: ...SQUIRE PLUS 2 OPERATIONS MANUAL PROCESS PACKAGING INC PAGE 87 OF 125 www iddeas com ...
Страница 88: ...SQUIRE PLUS 2 OPERATIONS MANUAL PROCESS PACKAGING INC PAGE 88 OF 125 www iddeas com ...
Страница 89: ...SQUIRE PLUS 2 OPERATIONS MANUAL PROCESS PACKAGING INC PAGE 89 OF 125 www iddeas com ...
Страница 90: ...SQUIRE PLUS 2 OPERATIONS MANUAL PROCESS PACKAGING INC PAGE 90 OF 125 www iddeas com ...
Страница 91: ...SQUIRE PLUS 2 OPERATIONS MANUAL PROCESS PACKAGING INC PAGE 91 OF 125 www iddeas com ...
Страница 92: ...SQUIRE PLUS 2 OPERATIONS MANUAL PROCESS PACKAGING INC PAGE 92 OF 125 www iddeas com ...
Страница 93: ...SQUIRE PLUS 2 OPERATIONS MANUAL PROCESS PACKAGING INC PAGE 93 OF 125 www iddeas com ...
Страница 94: ...SQUIRE PLUS 2 OPERATIONS MANUAL PROCESS PACKAGING INC PAGE 94 OF 125 www iddeas com ...
Страница 95: ...SQUIRE PLUS 2 OPERATIONS MANUAL PROCESS PACKAGING INC PAGE 95 OF 125 www iddeas com ...
Страница 96: ...SQUIRE PLUS 2 OPERATIONS MANUAL PROCESS PACKAGING INC PAGE 96 OF 125 www iddeas com ...
Страница 97: ...SQUIRE PLUS 2 OPERATIONS MANUAL PROCESS PACKAGING INC PAGE 97 OF 125 www iddeas com ...
Страница 98: ...SQUIRE PLUS 2 OPERATIONS MANUAL PROCESS PACKAGING INC PAGE 98 OF 125 www iddeas com ...
Страница 99: ...SQUIRE PLUS 2 OPERATIONS MANUAL PROCESS PACKAGING INC PAGE 99 OF 125 www iddeas com ...
Страница 100: ...SQUIRE PLUS 2 OPERATIONS MANUAL PROCESS PACKAGING INC PAGE 100 OF 125 www iddeas com ...
Страница 101: ...SQUIRE PLUS 2 OPERATIONS MANUAL PROCESS PACKAGING INC PAGE 101 OF 125 www iddeas com ...
Страница 102: ...SQUIRE PLUS 2 OPERATIONS MANUAL PROCESS PACKAGING INC PAGE 102 OF 125 www iddeas com ...
Страница 103: ...SQUIRE PLUS 2 OPERATIONS MANUAL PROCESS PACKAGING INC PAGE 103 OF 125 www iddeas com ...
Страница 104: ...SQUIRE PLUS 2 OPERATIONS MANUAL PROCESS PACKAGING INC PAGE 104 OF 125 www iddeas com ...
Страница 105: ...SQUIRE PLUS 2 OPERATIONS MANUAL PROCESS PACKAGING INC PAGE 105 OF 125 www iddeas com ...
Страница 106: ...SQUIRE PLUS 2 OPERATIONS MANUAL PROCESS PACKAGING INC PAGE 106 OF 125 www iddeas com ...
Страница 107: ...SQUIRE PLUS 2 OPERATIONS MANUAL PROCESS PACKAGING INC PAGE 107 OF 125 www iddeas com Back To TOC ...
Страница 108: ...SQUIRE PLUS 2 OPERATIONS MANUAL PROCESS PACKAGING INC PAGE 108 OF 125 www iddeas com 18 PNEUMATICS Back To TOC ...
Страница 109: ...SQUIRE PLUS 2 OPERATIONS MANUAL PROCESS PACKAGING INC PAGE 109 OF 125 www iddeas com 19 DIMENSIONS Back To TOC ...
Страница 111: ...SQUIRE PLUS 2 OPERATIONS MANUAL PROCESS PACKAGING INC PAGE 111 OF 125 www iddeas com Back To TOC ...