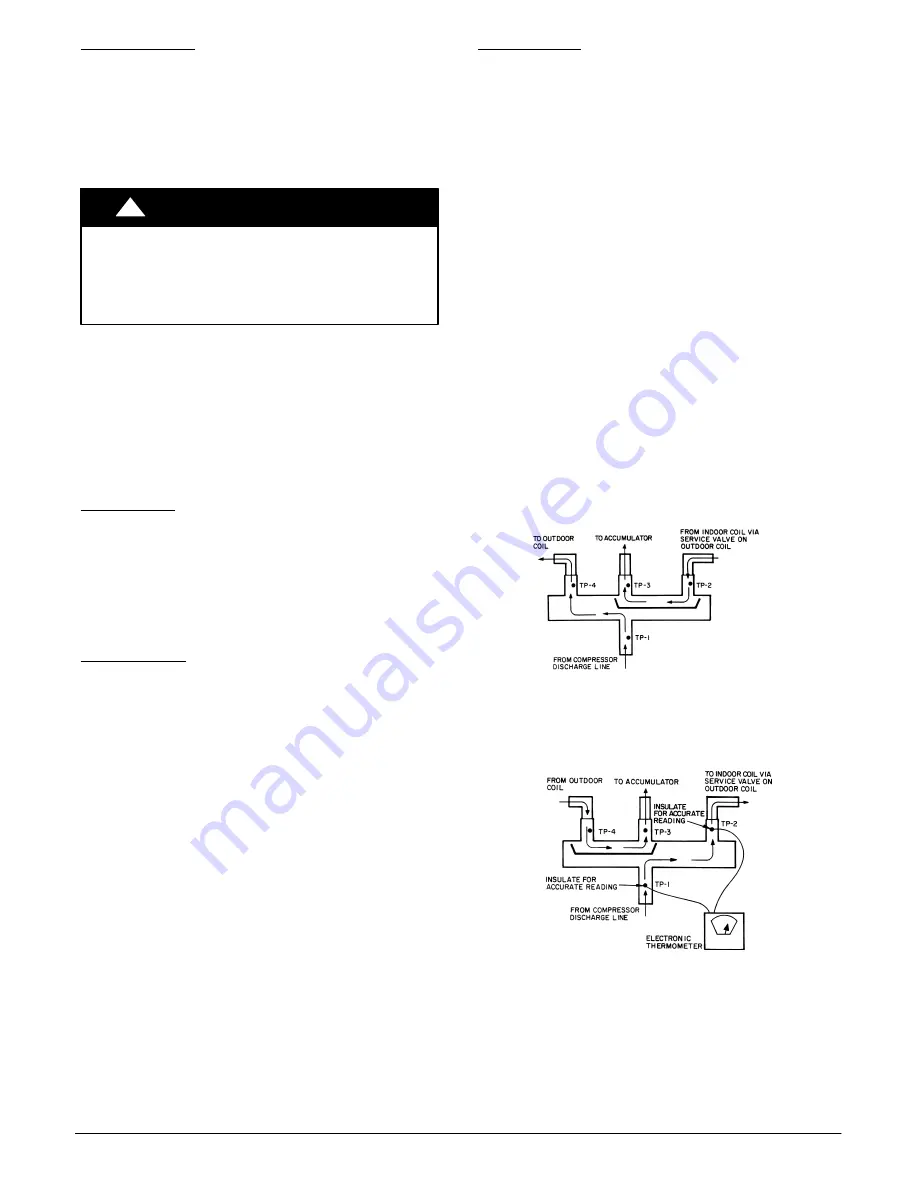
428 01 9700 03
11
Crankcase Heater
The crankcase heater prevents refrigerant migration and
compressor oil dilution during shutdown when compressor
is not operating. If the crankcase heater is de
−
energized for
more than 6 hours, both compressor service valves must be
closed.
The crankcase heater is powered by the high
−
voltage
power of the unit. It is connected across the line side of the
contactor and is thermostatically controlled.
!
WARNING
PERSONAL INJURY HAZARD
Failure to follow this warning could result in
personal injury or death.
Use extreme caution when troubleshooting this
device as line voltage is continually present.
To troubleshoot:
1. Apply voltmeter across crankcase heater leads to see
if heater voltage is on. Do not touch heater. Carefully
feel area around crankcase heater; if warm,
crankcase heater is functioning.
2. With power off and heater leads disconnected, check
across leads with ohmmeter. Do not look for a specific
resistance reading. Check for resistance or an open
circuit, and change heater if an open circuit is
detected.
Service Valves
The service valves in the outdoor unit come from the factory
frontseated. This means the refrigerant charge is isolated
from the line
−
set connection ports. To prevent damage to
the valve, use a wet cloth or other accepted heat sink
material on the valve before brazing.
The service valve cannot be field repaired, therefore, only a
complete valve or valve stem seal and service port caps are
available for replacement.
Defrost Controls
The control, which consists of defrost control board and
defrost thermostat, interrupts the normal system heating
operation to defrost the outdoor coil, if the coil saturated
suction temperature indicates freezing temperatures.
Defrost control board can be field set to check need for
defrost every 30, 50, or 90 minutes of operating time, by
connecting the jumper (labeled W1, on the circuit board) to
the spade terminal for the defrost time desired. The board is
factory set for 90 minutes. The defrost period is field
selectable, depending upon geographic areas and defrost
demands. Control board has additional feature that allows
unit to restart in defrost cycle if room thermostat is satisfied
during defrost. Defrost control simultaneously tops outdoor
fan, energizes reversing valve solenoid to return system to
cooling cycle (outdoor unit as condenser, indoor unit as
evaporator), and activates accessory electric heater.
The defrost timer limits defrosting period to 10 minutes.
Normally, the frost is removed and the defrost thermostat
contacts open to terminate defrosting before 10 minutes
have elapsed. When defrosting is terminated, the
outdoor
−
fan motor is energized, and reversing valve
solenoid is de
−
energized, returning unit to heating cycle.
Reversing Valve
In heat pumps, changeover between heating and cooling
modes is accomplished with a valve that reverses flow of
refrigerant in the system. The reversing valve solenoid can
be checked with the power off using an ohmmeter. Check
for continuity and shorting to ground. With control circuit (24
v) power on, check for correct voltage at solenoid coil, and
for burned or overheated solenoid.
With unit operating, other items can be checked, such as
frost or condensate on refrigerant lines.
Using a remote measuring device, check inlet and outlet line
temperatures. Do not touch lines. If reversing valve is
operating normally, inlet and outlet temperatures on
appropriate lines should be similar. Any temperature
difference would be due to heat loss or gain across valve
body. Temperatures are best checked with a remote reading
electronic
−
type thermometer with multiple probes.
Figure 11 and Figure 12 show test points on reversing valve
for recording temperatures. Insulate points for more
accurate reading. If valve is defective:
1. Shut off all power to unit.
2. Remove all charge from system.
3. Remove valve using a tubing cutter.
4. Install new valve (wrap valve with a wet rag to prevent
overheating while brazing).
5. After valve is brazed in, check for leaks.
6. Evacuate and charge system. Operate system in both
modes several times to be sure valve functions
properly.
LEGEND
TP —
Test Point
A07433
Figure 11
-
Reversing Valve
(Cooling Mode or Defrost Mode, Solenoid Energized)
LEGEND
TP —
Test Point
A07434
Figure 12
-
Reversing Valve
(Heating Mode, Solenoid De
−
energized)