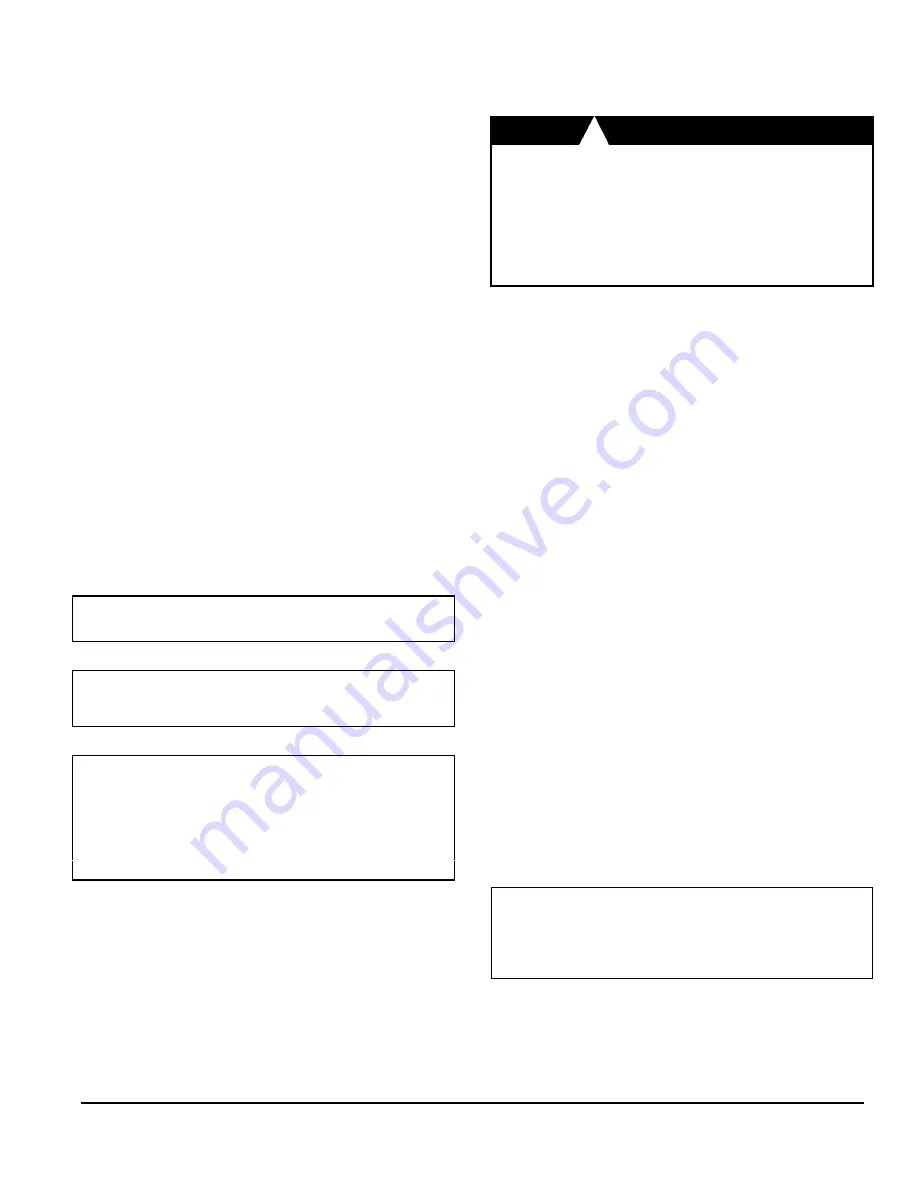
4
j.
Before servicing, allow furnace to cool. Always shut off electricity
and fuel to furnace when servicing. This will prevent electrical
shock or burns.
k.
Seal supply and return air ducts.
l.
The vent system
MUST
be checked to determine that it is the
correct type and size.
m. Install correct filter type and size.
n.
Unit
MUST
be installed so electrical components are protected
from direct contact with water.
2.1)
Safety Rules:
Your unit is built to provide many years of safe and dependable
service providing it is properly installed and maintained. However,
abuse and/or improper use can shorten the life of the unit and create
hazards for you, the owner.
a.
The U.S. Consumer Product Safety Commission recommends
that users of oil-burning appliances install carbon monoxide
detectors. There can be various sources of carbon monoxide in
a building or dwelling. The sources could be gas-fired clothes
dryers, gas cooking stoves, water heaters, furnaces, gas-fired
fireplaces, wood fireplaces, and several other items. Carbon
monoxide can cause serious bodily injury and/or death.
Therefore, to help alert people of potentially dangerous carbon
monoxide levels, you should have carbon monoxide detectors
listed by a nationally recognised agency (e.g. Underwriters
Laboratories or International Approval Services) installed and
maintained in the building or dwelling (see Note).
b.
There can be numerous sources of fire or smoke in a building or
dwelling. Fire or smoke can cause serious bodily injury, death,
and/or property damage. Therefore, in order to alert people of
potentially dangerous fire or smoke, you should have fire and
smoke detectors listed by Underwriters Laboratories installed
and maintained in the building or dwelling (see Note below).
NOTE:
The manufacturer of your furnace does not test any detectors
and makes no representations regarding any brand or type of
detector.
CAUTION
Insure that the area around the combustion air intake
terminal is free of snow, ice and debris
.
CAUTION
Do not use any commercially available soot remover.
This furnace has fiber type refractory combustion
chamber. Normal servicing of this unit does not require
cleanings of the combustion chamber. Use extreme
care if for any reason you have to work in the area of
the combustion chamber.
2.2)
Freezing Temperature and Your
Structure:
WARNING
WARNING
Freeze warning.
Turn off water system.
If your unit remains shut off during cold weather the
water pipes could freeze and burst, resulting in
serious water damage.
Your unit is equipped with safety devices that may keep it from
operating if sensors detect abnormal conditions such as clogged
exhaust flues.
If the structure will be unattended during cold weather you should take
these precautions.
a.
Turn off main water supply into the structure and drain the water
lines if possible. Open faucets in appropriate areas.
b.
Have someone check the structure frequently during cold
weather to make sure it is warm enough to prevent pipes from
freezing. Suggest they call a qualified service agency, if
required.
2.3)
Installation regulation:
All local and national code requirements governing the installation of
oil burning equipment, wiring and flue connections MUST be followed.
Some of the codes that may be applicable are:
CSA B139
INSTALLATION CODE FOR OIL
BURNING EQUIPMENT
ANSI/NFPA 31
INSTALLATION OF OIL BURNING
EQUIPMENT
ANSI/NFPA 90B
WARM AIR HEATING AND AIR
CONDITIONING SYSTEMS
ANSI/NFPA 70
NATIONAL ELECTRICAL CODE
CSA C22.2 No3
CANADIAN ELECTRICAL CODE
Only the latest issues of the above codes should be used.
3)
LOCATING THE FURNACE
CAUTION
Check carefully your furnace upon delivery for any
evidence of damage that may have occurred during
shipping and handling. Any claims for damages or lost
parts must be made with the Transport Company.
This furnace is approved for reduced clearances to combustible
construction, therefore, it may be installed in a closet or similar
enclosure and in any case, the unit should always be installed level.
In a basement, or when installed on the floor (as in a crawlspace), it is
recommended that the unit be installed on a concrete pad that is 1” to
2” thick.
!
Содержание FLO115DABR-A
Страница 20: ...21 FIGURE 4 2 Wiring diagram MBOV115DABRU B MBOV115DBU C DNS 0593 Rev B ...
Страница 21: ...22 Wiring diagram FLO115DABR A OLF140C12A FIGURE 4 3 DNS 0658 Rev B ...
Страница 22: ...23 PART LIST Model MBO115DABR B DNS 0597 Rev E ...
Страница 24: ...25 PART LIST Model MBOV115DABR B DNS 0598 Rev D ...
Страница 26: ...27 PART LIST Models MBOV115DABRU B MBOV115DBU C DNS 0605 Rev D ...
Страница 28: ...29 PART LIST Model LBO125DABR13 B DNS 0585 Rev D ...
Страница 30: ...31 PART LIST Models LBO145DABR12 B LBO145DABR34 B OLR182A16A DNS 0586 Rev B ...
Страница 32: ...33 DNS 0663 Rev C Model FLO115DABR A OLF140C12A PART LIST ...