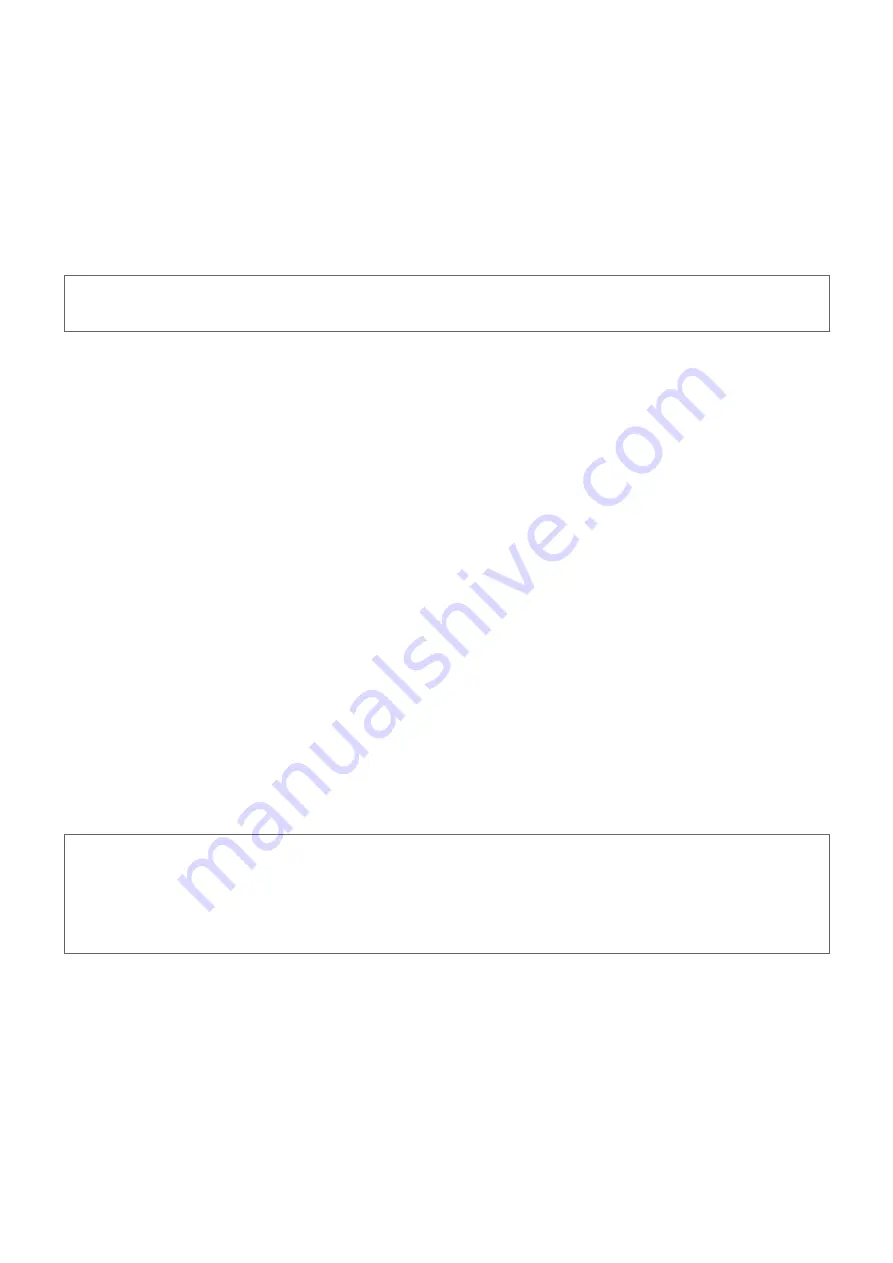
Maintenance
60
ROUTINE MAINTENANCE
–
Depending on the degree of pollution of the premises, clean the ventilation and/or the air conditioner (if present) filters and
grilles frequently.
–
Every 2-3 months check if there are dust deposits inside the control panel, suck and/or blow to remove any deposit.
–
Every six months check the clamping of the connections to the inner components, paying particular attention to the power
circuits.
–
Every six months check the clamping of the connections to the field control/safety devices, including any junction boxes.
–
Annually check that the electrical panel, the generator and the control unit equipotential is properly connected to earth.
–
Every six months check the condition of the safety devices (probes and pressure switches).
–
Every six months checkthat the pump and burner control circuits still meet the original conditions (refer to paragraph
“Commissioning”
)
m
IMPORTANT
In order to preserve the proper operation of the generator over time, we recommend requesting a half-yearly/yearly
inspection by the Technical Assistance Service, for a general check of all parts.
EXTRAORDINARY MAINTENANCE
The generator must be stopped periodically for a thorough inspection and maintenance: the time interval between downtime is
established through experience, by operating conditions, by the quality of the feed water, and by the type of fuel used.
Before accessing the generator body for inspection and cleaning, thoroughly check that no water or steam can reach the
generator through the connecting ducts. Each valve will have to be locked and, if necessary, isolated by removing a section of the
connection pipe to the system or by placing a blind flange in-between.
The pressurised parts must be carefully examined internally to look for any build-up, corrosion and other potential sources of
danger pertaining to the feed water.
It is necessary to remove the deposits through mechanical or chemical action and use suitable tools to ensure that the actual
thickness of the internal parts is not affected by corrosion. Any pockmark or other type of corrosion must be scraped and cleaned
with an iron brush until the metal is exposed. Leaks between all fume pipes and tube sheets must be examined carefully: any
welding must comply with legal requirements, not forgetting that the steam generator is a pressure appliance with an explosion
hazard, subject to control by the relative Body.
During the inspection, check all safety accessories (safety valve, safety level switches and safety pressure switches).
LEVEL SWITCH REPLACEMENT
To replace the safety level switch or part of it, strictly observe the following instructions:
–
check that the ceramic part of the new level probe is intact
–
check the rod length
–
check the coaxiality of the rod with the level probe axis
–
check the integrity of the electrical system, in particular check that the insulation resistance of the electrical cable that
connects the probe to the panel is above 2 MΩ
–
check the integrity of the probe with particular regard to the isolation between the central electrode and the external part,
that must be ≥ at 10 MΩ
–
check the operation of the level switch, consisting of the assembly of the two ceramic probes and relative conductivity relays.
m
IMPORTANT
–
The electronic level relays inside the electrical panel HAVE AN AVERAGE CALCULATED DURATION (MTTFd, "Mean Time To
Failure") of 8 YEARS. It is an average time before a dangerous failure occurs. Therefore, they must be replaced after this
operating period. We recommend replacing the probes once a year. To be evaluated, during cleaning/maintenance, the
other mechanical, electromechanical and electronic parts.
–
The faulty components must be replaced with ICI CALDAIE S.p.A. original components.
Содержание 86440350
Страница 78: ...Appendixes for Technical Personnel 78 ...
Страница 79: ...Appendixes for Technical Personnel 79 ...