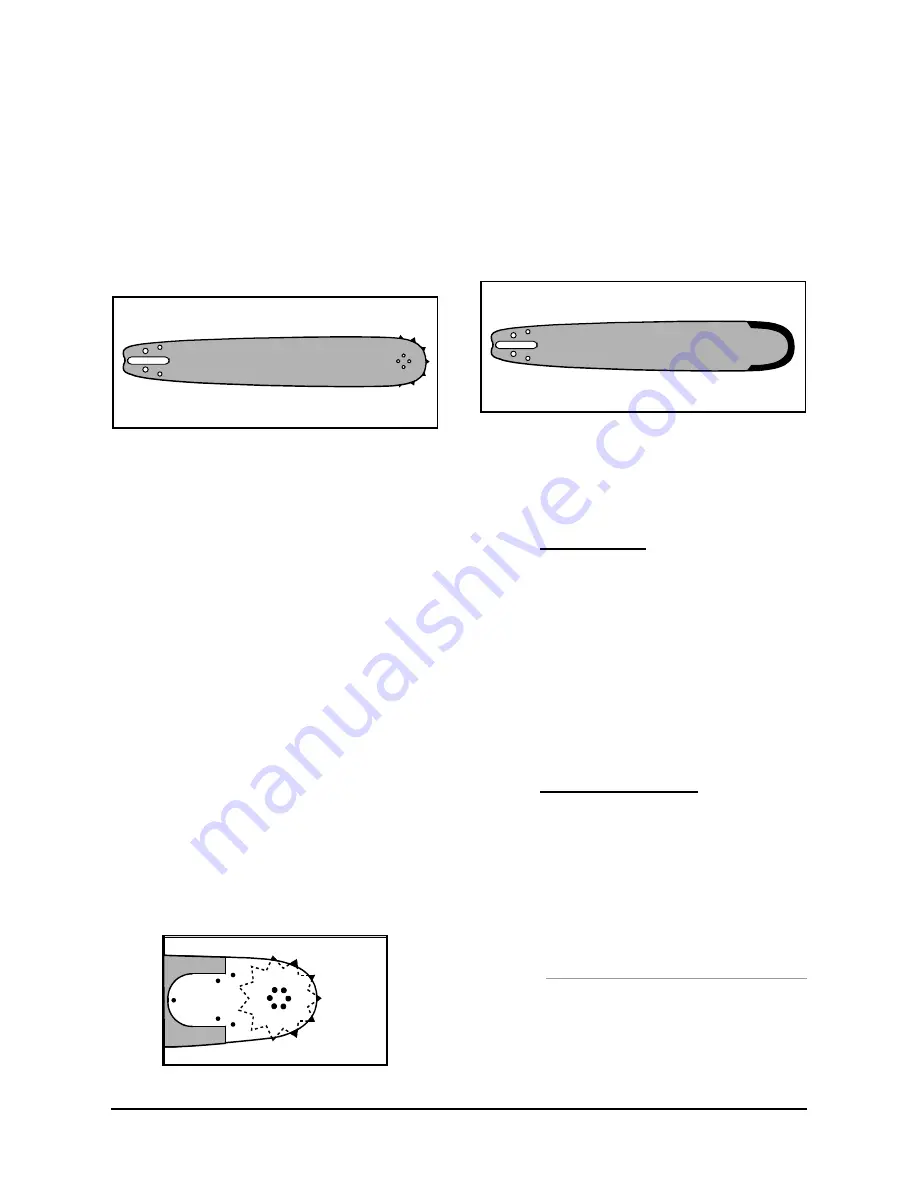
ICFR – Chainsaw Safety and Operating Handbook
49
Bars with sprocket noses produce significantly less
friction than solid nose bars. For highest efficiency,
bars with sprocket noses are recommended.
•
Sprocket nose guide bar
The sprocket is replaceable. Friction and wear
on the guide bar nose are substantially reduced
compared to solid nose bars (rolling friction
instead of sliding friction). The reduced friction
enables the chain to be run with more tension.
Figure 75: Sprocket nose guide bar
These guide bars have a higher cutting capacity
than solid nose bars. Bore cuts are also easier and
safer to perform. The lower rate of frictional wear
and higher cutting capacity also have a positive
effect when debranching, i.e. cutting alternately
with the top and the bottom of the guide bar.
These guide bars are ideally suited for felling
smaller trees and debranching.
•
Replaceable sprocket nose guide bar
On this type of guide bar the entire nose or only
the sprocket can be replaced.
These guide bars combine the high strength
and robustness of solid guide bars with the high
cutting performance of the sprocket nose. They
are recommended for use with long guide bars
to reduce the load on the bar tip. The load is
transferred to the high quality roller bearing.
These guide bars are ideally suited for very
demanding professional felling and cross-cutting
on high powered, heavy duty chainsaws.
Figure 76: Replaceable sprocket nose guide bar
•
Solid nose guide bar
These bars and are sometimes called “stellite tip”
bars and are made in a single piece from specially
formulated steel.
Their great resilience make them highly resistant
to flexing stresses and warping. The rails are
hardened and the highly stressed nose area is
stellite tipped.
Figure 77: Solid nose guide bar
These guide bars are ideally suited for heavy-duty
professional felling and cross-cutting on high powered
saws for large trees and in extreme conditions.
14.2.3
g
uide
bAr
cAre
As mentioned earlier, the cutting attachment is subject
to high wear. The guide bar wears particularly in the
area where most of the cutting is done, normally the
underside of the bar.
To ensure that the guide bar wears evenly on both sides,
it should be turned over every time the saw chain is
removed. The chain lubrication inlet holes and the bar
groove should be cleaned thoroughly at the same time
by using a groove cleaner.
14.2.4
g
uide
bAr
mAintenAnce
Once a guide bar has been in use for an extended
period the groove depth should be measured before a
sharpened chain is fitted. The measurement is taken in
the area where most of the cutting is done on the guide
bar. If the measured depth is less than the minimum
specified by the manufacturer, the guide bar must be
replaced.
14.2.4.1 d
ressing
guide
bar
raiLs
to
remove
burrs
Burrs on the guide bar rails result from normal wear
over time. Remove the burrs regularly with a flat file,
filing at a 45° angle.