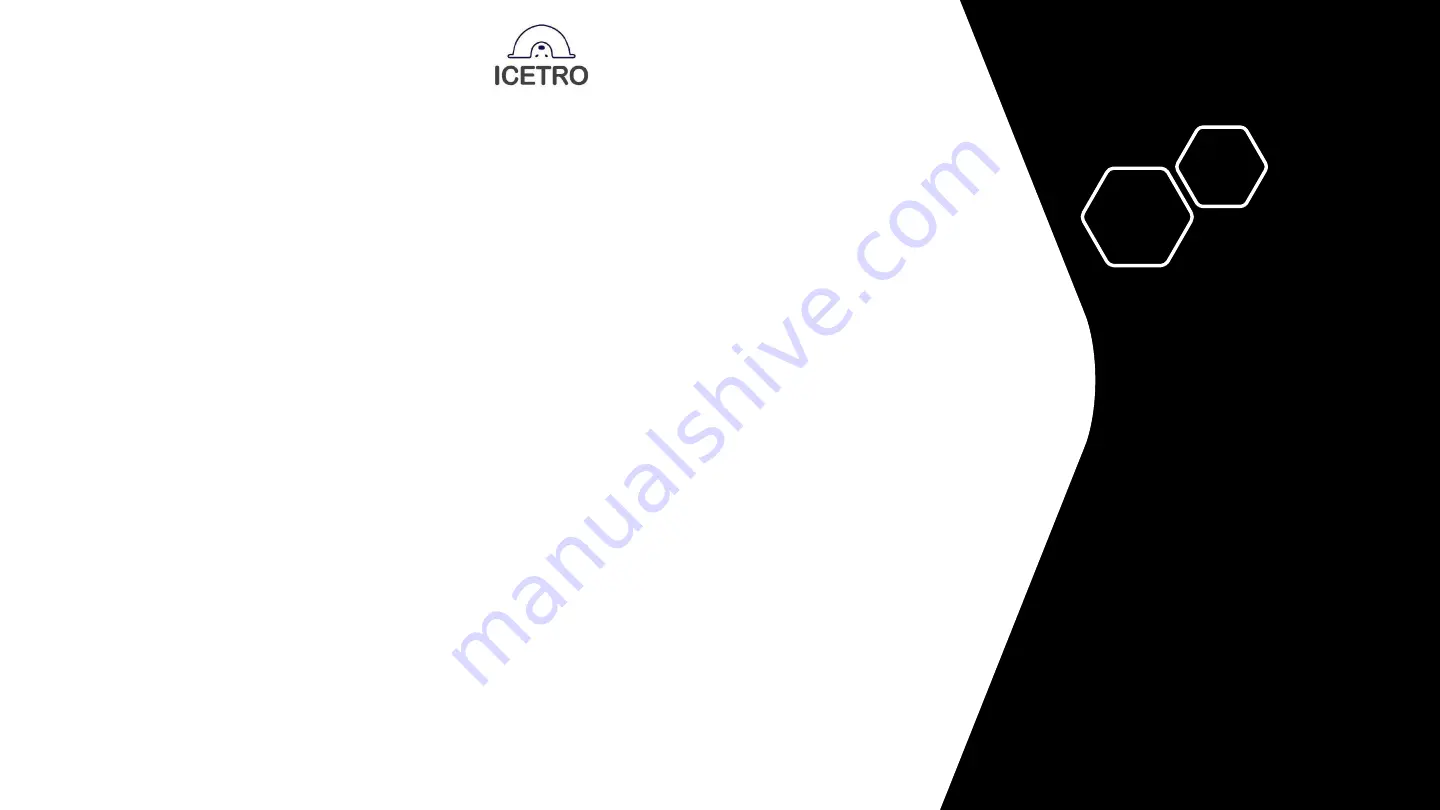
Proper Installation
IM-Series
4
Installation, Start Up, and Check
Please double check these items before install & start-up before calling for service.
(These items are not covered under your Labor Warranty)
1.
Has all tape and packing materials been removed from Machine?
2.
Is the unit installed in a location that is away from heat generating equipment or direct sunlight?
3.
Is the unit level front to back and side to side? Adjustable legs on bins and dispensers make this quick and easy.
4.
Is the correct electrical power provided? Ensure the unit has the specified voltage and amperage and is on a dedicated circuit. Do not use a
drop cord or power strip with any ice machine. This could cause a voltage drop and compensatory amperage spike or cause the circuit
breaker to trip.
5.
Check drain line pipe sizes. Insure they are ¾ inch and line drops ¼ inch per foot of run to insure both machine and bin drainage is
effective.
6.
Is water supplied to the unit? Water Line size, 3/8 inch, must be supplied to ensure sufficient water flow is always available. Required
water pressure is 20 psi minimum and 80 psi maximum. This unit is designed to work with water temperatures of 50
°F - 90°F.
7.
Is the unit installed in an area with sufficient ventilation at the back for proper rejection of condenser heat?
The manufacturer requires 8”
of clearance at the back & sides of the unit. Twelve (12”) inches is required at the top of unit. Fresh air is taken in from the back and
dispelled from the top and sides. Never block the top air vents!
8.
This unit is designed to work in ambient air temperatures of 50
°F - 100°F.
9.
Is the Unit located in an area which has air borne particulate (flour, yeast, etc) that can build mold and bacteria inside the machine or clog
the filter and condenser? There are products that can be installed to help these problems.
10.
Scale or Mold build-up can affect the sequence of operation, timing and production. Is a water filter installed? We recommend our
exclusive Citryne Pro Ice Filtration for the best scale clean results. Scale will increase operating costs and reduce or shut down the
machine’s performance.
11.
Do not install this unit outdoors.
12. If you are installing an ice maker on top of an existing bin, check the bin to it insure it has a baffle in the bin to keep ice
from coming out of the bin door.
13. If you are installing the ice maker on top of a dispenser, the dispenser manufacturer must provide the top kit to prevent
leaks and bin problems. Additionally, an Icetro thermostat kit is required (ITS-150-KIT).
Содержание IM Series
Страница 1: ...IM Series Installation Service Manual Air Water Cooled Cubers ...
Страница 24: ...24 IM Series Wiring Diagram ...
Страница 30: ...30 IM Series Service Tips Pinching Tubing Re rounding Tubing ...
Страница 42: ...42 IM Series Service Tips P T Chart Cycle Times ...
Страница 43: ...43 IM Series Service Tips P T Chart Cycle Times ...
Страница 44: ...44 IM Series Service Tips P T Chart Cycle Times ...
Страница 45: ...45 IM Series Service Tips P T Chart Cycle Times ...
Страница 46: ...Tubing Schematic IM Series Tubing Schematic 46 ...
Страница 52: ...THANK YOU 1 15 2022 ...