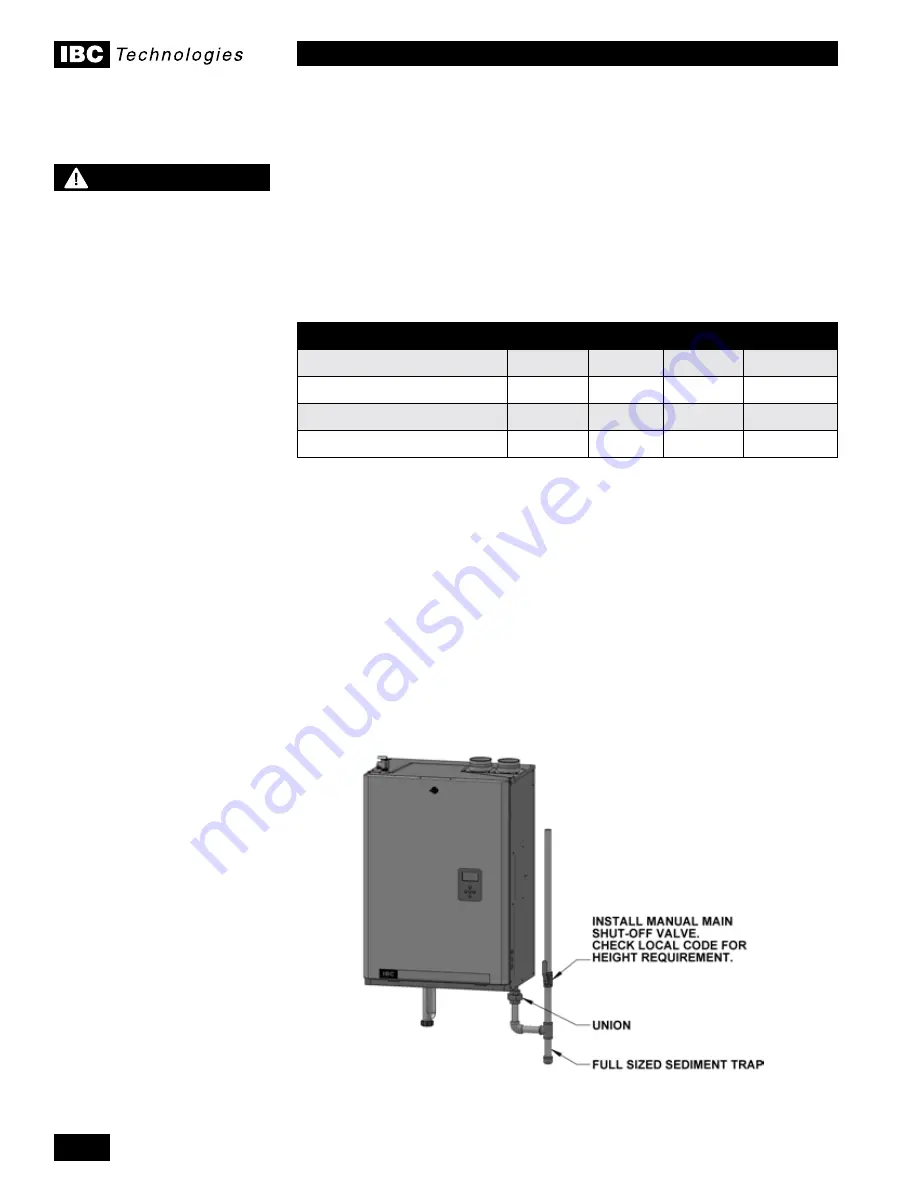
INSTALLATION AND OPERATION INSTRUCTIONS
1-22
SL 30-175, SL 45-260 MODULATING GAS BOILERS
gas PiPing
the sl 30-175 and sl 45-260 boilers require an inlet gas pressure of at least
5.0" w.c. for natural gas or propane, ensuring 4” at the gas valve at high fire.
For either fuel, the inlet pressure shall be no greater than 14.0" w.c. Confirm this
pressure range is available with your local gas supplier. the inlet gas connection
of the boiler is 3/4" nPt (female).
adequate gas supply piping shall be provided with recommended minimum
3/4" sched 40 (e.g. iron Pipe size (iPs)) and using a 1" w.c. pressure drop, in
accordance with the following chart:
MODEL
1/2" IPS
3/4" IPS 1" IPS
1 1/4" IPS
sl 30-175 (natural gas)
10’
60’
200’
700’
sl 30-175 (Propane)
40’
150’
500’
2,000’
sl 45-260 (natural gas)
n/a
30’
90’
350’
sl 45-260 (Propane)
20’
80’
250’
900’
Table 7: Maximum Pipe Length (ft)
gas piping must have a sediment trap ahead of the boiler’s gas valve
(see Figure
29)
. a manual shutoff valve must be located outside the boiler, in accordance with
local codes/standards. all threaded joints in gas piping should be made with an
approved piping compound resistant to the action of natural gas/propane. use
proper hangers to support gas supply piping as per applicable codes.
the boiler must be disconnected or otherwise isolated from the gas supply
during any pressure testing of the system at test pressures in excess of 1/2 psig.
dissipate test pressure prior to reconnecting. the boiler and its gas piping shall
be leak tested before being placed into operation.
the gas valve is provided with pressure taps to measure gas pressure upstream
(supply pressure) and downstream (manifold pressure) of the gas valve
(see
Figure 32).
Note that manifold pressure varies slightly in accordance with firing
rates with the modulating series boilers, but will always be close to 0” w.c.
1.7
Figure 29: Typical gas piping
NOTE
Due to the precision of
modern modulating boilers
it is important to pay special
attention to gas pressure
regulation.
It is essential to check gas
supply pressure to each
boiler with a manometer or
other high-quality precision
measuring device. Pressure
should be monitored before
firing the boiler, when the
regulator is in a “lock-
up” condition and during
operation, throughout the
boiler’s full modulation range.
Pay special attention to
retrofit situations where
existing regulators may have
an over-sized orifice and/or
worn seats, causing pressure
“creep” and high lock up
pressures.
A high quality regulator will
maintain constant pressure
above the boiler’s minimum
specification at all firing
rates, and will not exceed the
boiler’s maximum pressure
rating when locked-up with no
load.
Содержание SL 30-175
Страница 76: ...NOTES...