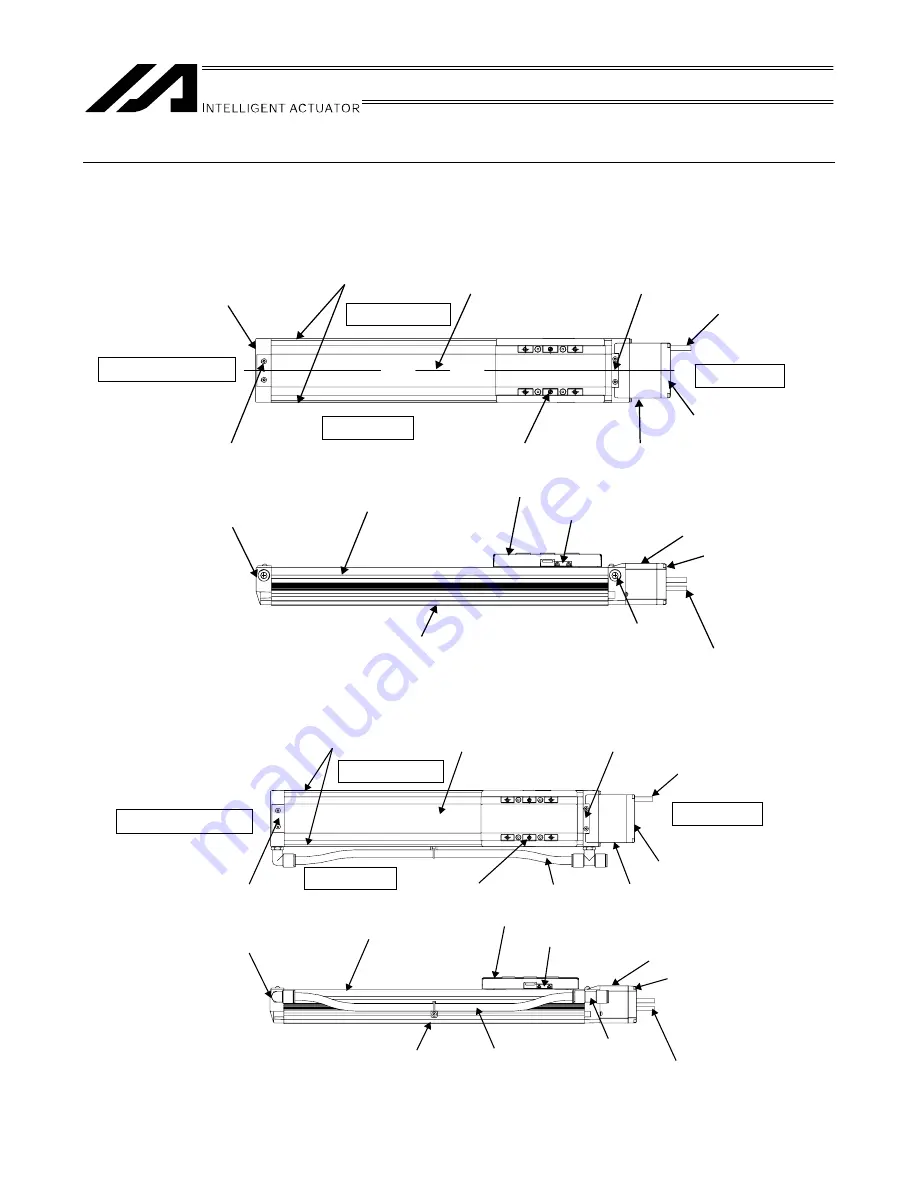
9
Names of the Parts
In this operating manual, the left and right sides are indicated by looking at the actuator from the motor end, with
the actuator placed horizontally, as shown in the figure below.
1. ISDB/ISPDB
2. ISDBCR/ISPDBCR
Right side (R)
Left side (L)
Motor cover
Slider
Front cover
Base
Actuator cable
Front side
Motor side
Coupling cover
Rear cover
Coupling cover
Left side (L)
Front side
Motor side
Slider
Front cover
Base
Actuator cable
Motor cover
Rear cover
Stainless sheet
Sheet cover plate
Side cover
Slider cover
Plug screw
Air tube
Air piping joint
Side cover
Front cover
Motor cover
Rear cover
Actuator cable
Side cover
Sheet cover plate
Air tube
Stainless sheet
Actuator cable
Rear cover
Motor cover
Slider cover
Grease nipple
Grease nipple
Side cover
Right side (R)