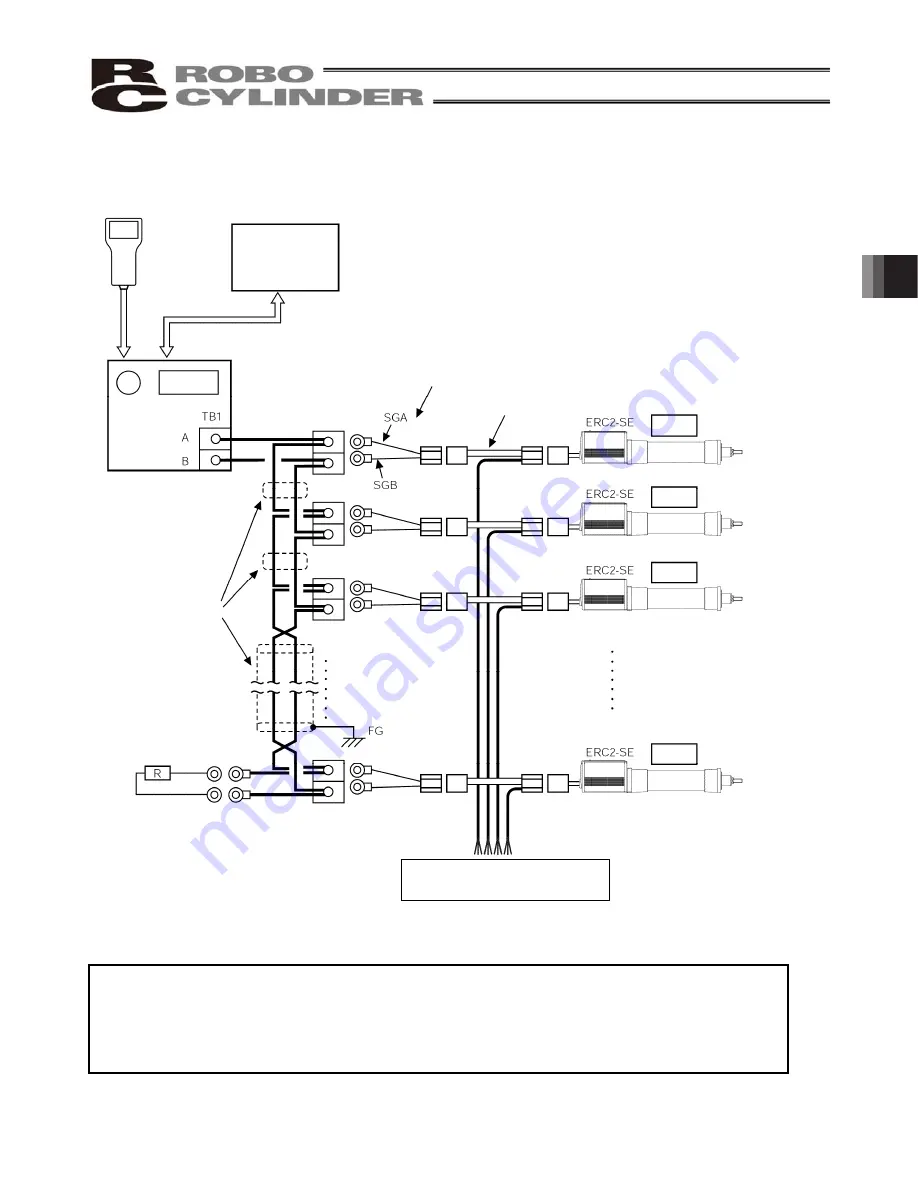
41
4. Wiring
4.1.1
SIO Communication Connection Using a Relay Terminal Block
* The emergency stop circuit is the same as illustrated on the previous page.
(Note 1) If the total length of the communication cable is 10 m or longer and you experience
communication errors, connect a terminal resistor to the last axis.
(Note 2) If the actuators use different power supplies, align 0 [V] on all power supplies.
(Note 3) Connect the shielded wire of each axis to FG.
(Note 4) If the overall length of link cable exceeds 30 m, use wire of 22AWG or larger size.
Teaching pendant
PC, PLC
Relay terminal
block
Actuator 1
Actuator 2
Actuator 3
One-pair shielded cable
(Fabricated by the customer)
Terminal resistor
1/2W, 220
:
SIO converter
Actuator 16
J.S.T.
Mfg.
Power & I/O cable
J.S.T.
Mfg.
24-VDC control power, motor power,
brake signal, ground, shield
(
Fabricated by the customer)
Содержание ERC2
Страница 1: ...Operation Manual Seventh Edition ERC2 Actuator with Integrated Controller SIO Type ...
Страница 2: ......
Страница 10: ......
Страница 136: ......
Страница 137: ......