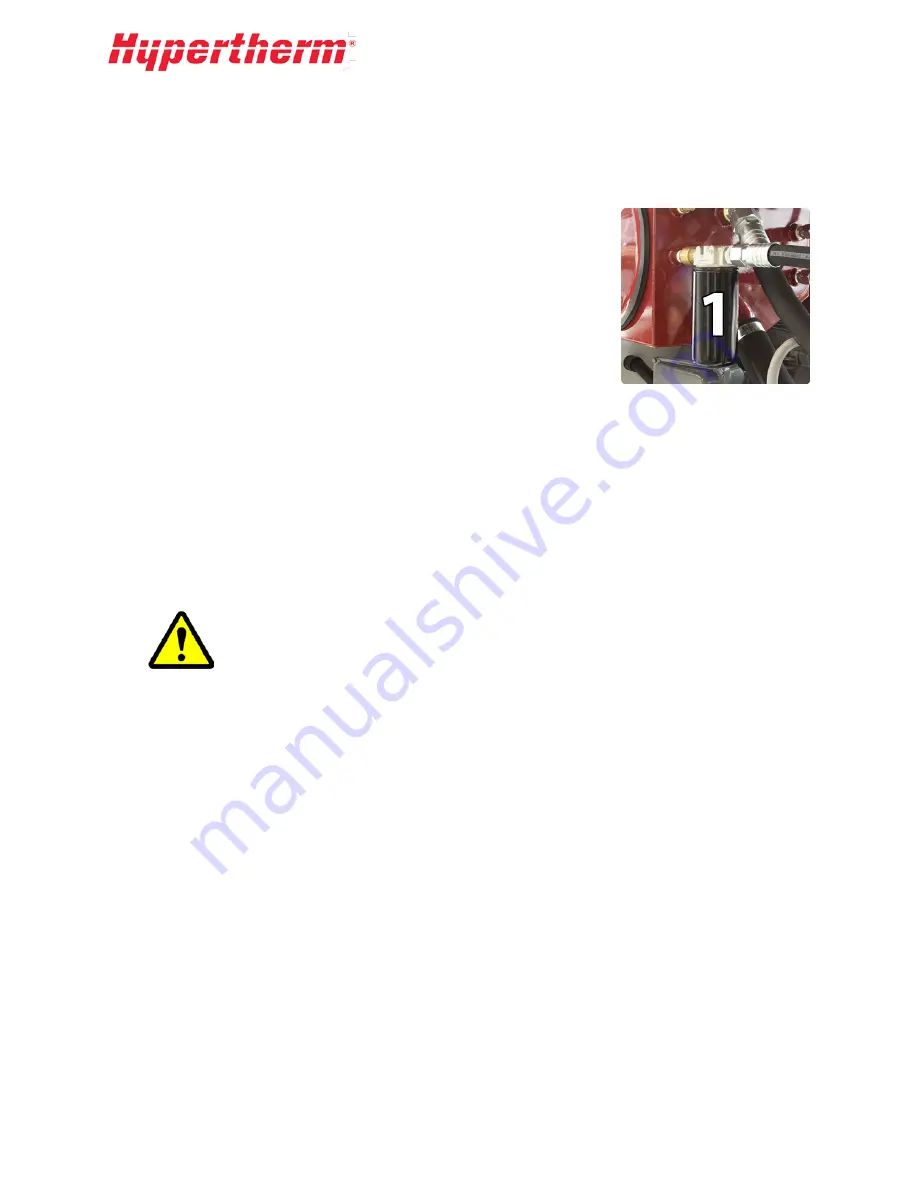
8.3
Oil Filter
The oil filter is installed in line with the heat exchanger. The filter element should be changed when the
oil is changed or at the maintenance interval given in the
Maintenance and Troubleshooting
section.
Filter element replacement procedure:
Requires 1 - Filter Element
1.
Unscrew the filter
(1)
from the top housing.
2.
Discard the old filter element.
3.
Install the new element according to the diagram that comes with
the element.
8.4
Heat Exchanger
HyPrecision 100D/150D pumps are equipped with a water/oil heat exchanger and a gear pump.
The gear pump is located on the end of the main motor and is part of the “Kidney Loop” system used
for cooling the hydraulic oil. The type of cooling system will vary according to system size and
customer preferences.
Water/Oil Exchanger (Standard)
If your pump is equipped with the water/oil heat exchanger, the gear pump will deliver the oil to the
hydraulic filter before going through the heat exchanger and back to the pump. The heat exchanger is
sized for use with water.
If you are using a chiller with water/glycol solution the efficiency of the heat
exchanger will be reduced and may require reducing the temperature set point of
a chiller.
The oil temperature variations coming from the heat exchanger can be controlled by adjusting the flow
rate of water. The flow rate of the water can be adjusted by either the water-modulating valve (if
applicable) or a manual ball valve.
For directions on adjusting the water-modulating valve please refer to the
Low-Pressure Water
section
of this manual.
For best long-term performance, the cooling water should be low in total dissolved solids (TDS). High
TDS levels can lead to clogging and loss of efficiency in the heat exchanger.
Air/Oil Exchanger (Optional)
If your pump is equipped with an air/oil cooler, the gear pump will deliver the oil through a one-inch
external hydraulic hose to the air/oil cooler and back to the bulkhead on the pump. The cooler uses a
radiator with an external fan powered by a fractional horsepower motor to cool the oil temperature to an
acceptable range.
The air/oil cooler fan will automatically turn on once the hydraulic oil reaches the factory set
temperature. Once running, the fan will remain on for a minimum of 10 minutes. If after 10 minutes, the
oil is still above the preset temperature the fan will remain on until the oil has dropped below that
temperature.
54
Содержание HyPrecision 100D
Страница 1: ...Instruction Manual 808310 Revision 0 English Original instructions ...
Страница 2: ...Instruction Manual 808310 Revision 0 English March 2014 Hypertherm Inc Hanover NH 03755 USA ...
Страница 16: ...14 ...
Страница 24: ...22 ...
Страница 27: ...25 ...
Страница 34: ...32 ...
Страница 58: ...56 ...
Страница 74: ...72 ...
Страница 75: ...12 Drawings and Parts Lists 73 ...
Страница 76: ...74 ...
Страница 77: ...13 Controls Manual 75 ...