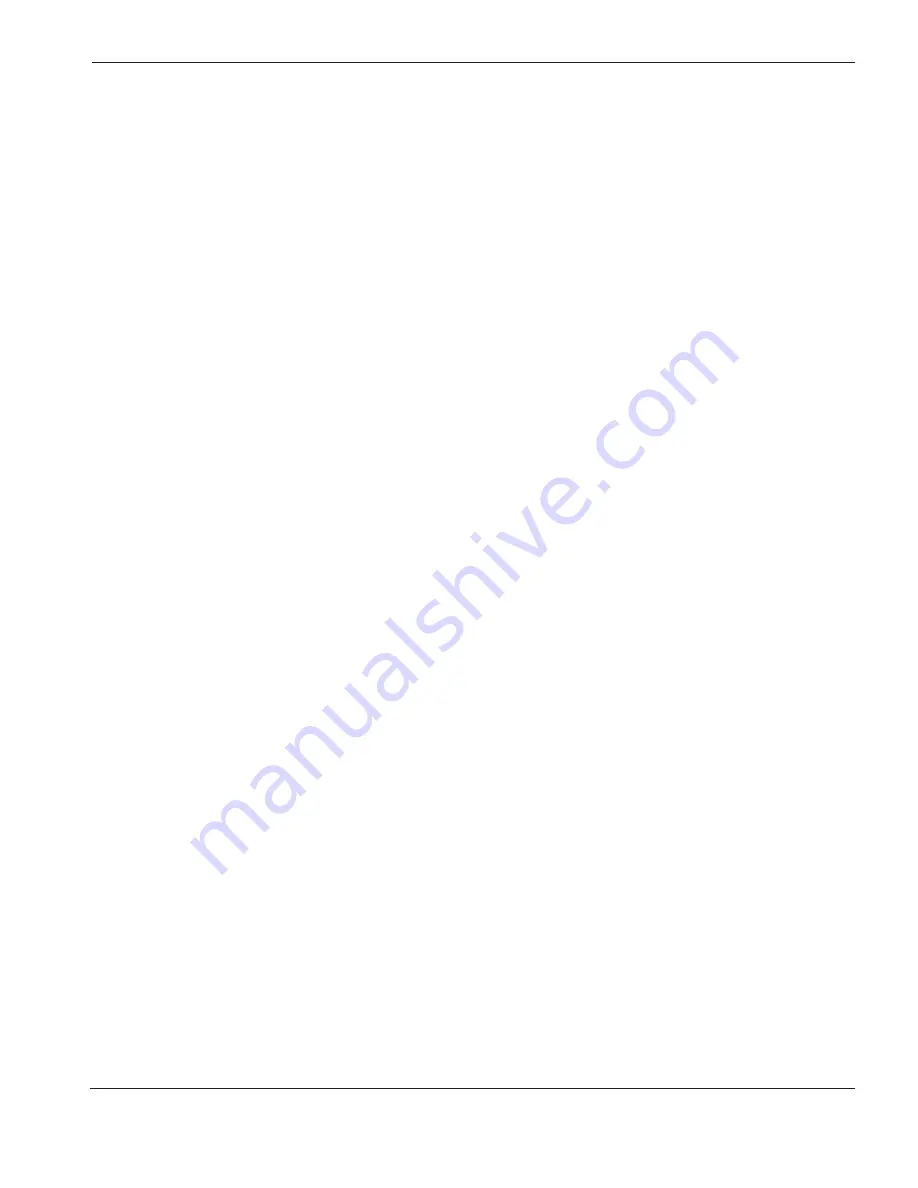
Maintenance
HPR400XD Auto Gas –
806160
5-59
3. Locate dipswitch S301 on the control board (PCB3) and move switch 5 to the ON position. The switch must be
returned to its original position before cutting.
4. Measure the open circuit voltage (OCV)
Attach the test leads of a DC volt meter to the NEG terminal and the WORK terminal on the I/O board. Turn ON the
power to start the chopper test. After the contactor (CON1) closes, read the OCV which should be about 360 VDC.
• If the OCV is 0, the chopper is probably faulty. Swap chopper 1 with chopper 2 for verification. If chopper 1 is
faulty, the error code should change to 106. Replace chopper 1.
• If OCV is about 360 VDC, continue to step 5.
5. Swap current sensor 1 (CS1) with current sensor 2 (CS2). Move the sensor, but leave the power cable and the
control wiring in place.
• If the error remains on chopper 1, replace the I/O PCB.
• If the error changes to chopper 2, replace CS1.
chopper 2, 3, or 4 failure
1. Swap the current sensor for the chopper that failed with the current sensor for the next chopper in sequence.
• If the error moves to the next chopper in sequence, replace the current sensor for the chopper that failed.
• If the error remains on the original chopper, continue to step 2.
2. Measure the OCV
• The chopper outputs are connected in parallel at the I/O board, and the choppers are tested in sequence (1, 3, 2,
and 4). This means that if you measure the OCV at the NEG and WORK terminals on a fully functional HPR400XD,
the voltage will be 0 until the contactor (CON1) closes. Chopper 1 will turn on and you will measure 360 VDC.
Chopper 1 will turn off and the voltage will decrease to 0. Chopper 3 (1, 3, 2, and 4) will turn on next, and the
voltage will increase to 360 VDC and then decrease to 0 when chopper 3 turns off. This sequence repeats until all
4 choppers are tested.
Example:
If you get error 075 or 107, you know chopper 3 failed the test. Because chopper 1 and chopper 2 passed the
test, you know the incoming power and the I/O board are OK. If you measure the OCV at the NEG terminal and the
WORK terminal on the I/O board, you will see the voltage cycle from 0 to 360, back to 0, and then to 360 again,
because chopper 1 and chopper 2 are OK. If you do not get the third reading of 360 VDC from chopper 3, that
means chopper 3 is faulty. You can swap chopper 3 with chopper 2 for verification. The error code will move to
chopper 2, if chopper 3 is faulty. If the error does not move, or you measure an OCV of about 360 VDC for chopper 3,
contact Hypertherm Technical Service at 800-643-9878.
Note: Return switch 5 on S301 to the OFF position before returning to normal cutting operations.
Содержание HyPerformance Plasma HPR400
Страница 1: ...HyPerformance Plasma HPR400XD Auto gas Instruction manual 806160 Revision 4 ...
Страница 26: ...Specifications 2 2 HPR400XD Auto Gas 806160 ...
Страница 32: ...Specifications 2 8 HPR400XD Auto Gas 806160 Horizontal mounting Vertical mounting Mounted on table ...
Страница 48: ...Installation 3 10 HPR400XD Auto Gas 806160 ...
Страница 53: ...Installation HPR400XD Auto Gas 806160 3 15 Horizontal RHF mounting Vertical RHF mounting ...
Страница 57: ...Installation HPR400XD Auto Gas 806160 3 19 This page is blank intentionally ...
Страница 65: ...Installation HPR400XD Auto Gas 806160 3 27 7 8 8 7 ...
Страница 67: ...Installation HPR400XD Auto Gas 806160 3 29 9 Caution Never use PTFE tape on any joint preparation ...
Страница 100: ...Installation 3 62 HPR400XD Auto Gas 806160 ...
Страница 107: ...Operation HPR400XD Auto Gas 806160 4 7 Diagnostic screen ...
Страница 108: ...Operation 4 8 HPR400XD Auto Gas 806160 Test screen ...
Страница 109: ...Operation HPR400XD Auto Gas 806160 4 9 Cut chart screen ...
Страница 197: ...Operation HPR400XD Auto Gas 806160 4 97 ...
Страница 287: ...7 4 HPR400XD Auto Gas 806160 Discrete output functionality ...
Страница 347: ...Appendix B CNC Interface Protocol b 28 HPR400XD Auto Gas 806160 ...
Страница 355: ...4 HPR400XD Auto Gas 806160 ...