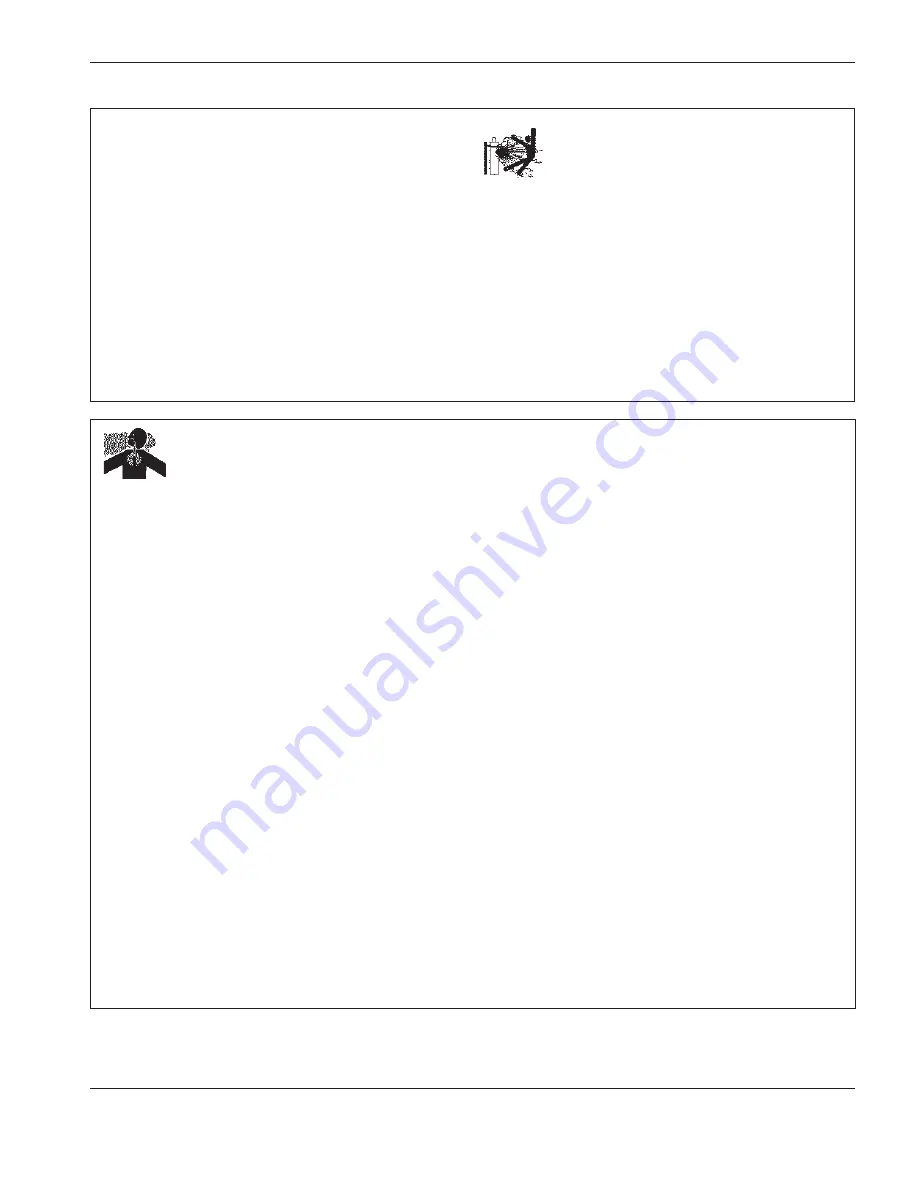
Safety and Compliance
Sc-5
Safety
toXIc FUMES cAN cAUSE INJURy oR DEAtH
The plasma arc by itself is the heat source used for cutting.
Accordingly, although the plasma arc has not been identified as a
source of toxic fumes, the material being cut can be a source of toxic
fumes or gases that deplete oxygen.
The fumes produced vary depending on the metal that is cut. Metals
that may release toxic fumes include, but are not limited to, stainless
steel, carbon steel, zinc (galvanized), and copper.
In some cases, the metal may be coated with a substance that could
release toxic fumes. Toxic coatings include, but are not limited to, lead
(in some paints), cadmium (in some paints and fillers), and beryllium.
The gases produced by plasma cutting vary based on the material
to be cut and the method of cutting, but may include ozone, oxides
of nitrogen, hexavalent chromium, hydrogen, and other substances
if such are contained in or released by the material being cut.
Caution should be taken to minimize exposure to fumes produced
by any industrial process. Depending on the chemical composition
and concentration of the fumes (as well as other factors, such as
ventilation), there may be a risk of physical illness, such as birth
defects or cancer.
It is the responsibility of the equipment and site owner to test the air
quality in the cutting area and to make sure that the air quality in the
workplace meets all local and national standards and regulations.
The air quality level in any relevant workplace depends on site-specific
variables such as:
•
Table design (wet, dry, underwater).
•
Material composition, surface finish, and composition of coatings.
•
Volume of material removed.
•
Duration of cutting or gouging.
•
Size, air volume, ventilation, and filtration of the workplace.
•
Personal protective equipment.
•
Number of welding and cutting systems in operation.
•
Other workplace processes that may produce fumes.
If the workplace must conform to national or local regulations, only
monitoring or testing done at the site can determine whether the
workplace is above or below allowable levels.
To reduce the risk of exposure to fumes:
•
Remove all coatings and solvents from the metal before cutting.
•
Use local exhaust ventilation to remove fumes from the air.
•
Do not inhale fumes. Wear an air-supplied respirator when cutting
any metal coated with, containing, or suspected to contain toxic
elements.
•
Make sure that those using welding or cutting equipment, as well
as air-supplied respiration devices, are qualified and trained in the
proper use of such equipment.
•
Never cut containers with potentially toxic materials inside. Empty
and properly clean the container first.
•
Monitor or test the air quality at the site as needed.
•
Consult with a local expert to implement a site plan to make sure air
quality is safe.
coMPRESSED gAS EqUIPMENt
SAFEty
•
Never lubricate cylinder valves or regulators with oil or grease.
•
Use only correct gas cylinders, regulators, hoses, and fittings
designed for the specific application.
•
Maintain all compressed gas equipment and associated parts in good
condition.
•
Label and color-code all gas hoses to identify the type of gas in each
hose. Consult applicable national and local regulations.
gAS cylINDERS cAN EXPloDE
IF DAMAgED
Gas cylinders contain gas under high pressure. If damaged, a cylinder
can explode.
•
Handle and use compressed gas cylinders in accordance with
applicable national and local regulations.
•
Never use a cylinder that is not upright and secured in place.
•
Keep the protective cap in place over the valve except when the
cylinder is in use or connected for use.
•
Never allow electrical contact between the plasma arc and a cylinder.
•
Never expose cylinders to excessive heat, sparks, slag, or open flame.
•
Never use a hammer, wrench, or other tool to open a stuck
cylinder valve.
Содержание HyPerformance Plasma HPR400
Страница 1: ...HyPerformance Plasma HPR400XD Auto gas Instruction manual 806160 Revision 4 ...
Страница 26: ...Specifications 2 2 HPR400XD Auto Gas 806160 ...
Страница 32: ...Specifications 2 8 HPR400XD Auto Gas 806160 Horizontal mounting Vertical mounting Mounted on table ...
Страница 48: ...Installation 3 10 HPR400XD Auto Gas 806160 ...
Страница 53: ...Installation HPR400XD Auto Gas 806160 3 15 Horizontal RHF mounting Vertical RHF mounting ...
Страница 57: ...Installation HPR400XD Auto Gas 806160 3 19 This page is blank intentionally ...
Страница 65: ...Installation HPR400XD Auto Gas 806160 3 27 7 8 8 7 ...
Страница 67: ...Installation HPR400XD Auto Gas 806160 3 29 9 Caution Never use PTFE tape on any joint preparation ...
Страница 100: ...Installation 3 62 HPR400XD Auto Gas 806160 ...
Страница 107: ...Operation HPR400XD Auto Gas 806160 4 7 Diagnostic screen ...
Страница 108: ...Operation 4 8 HPR400XD Auto Gas 806160 Test screen ...
Страница 109: ...Operation HPR400XD Auto Gas 806160 4 9 Cut chart screen ...
Страница 197: ...Operation HPR400XD Auto Gas 806160 4 97 ...
Страница 287: ...7 4 HPR400XD Auto Gas 806160 Discrete output functionality ...
Страница 347: ...Appendix B CNC Interface Protocol b 28 HPR400XD Auto Gas 806160 ...
Страница 355: ...4 HPR400XD Auto Gas 806160 ...