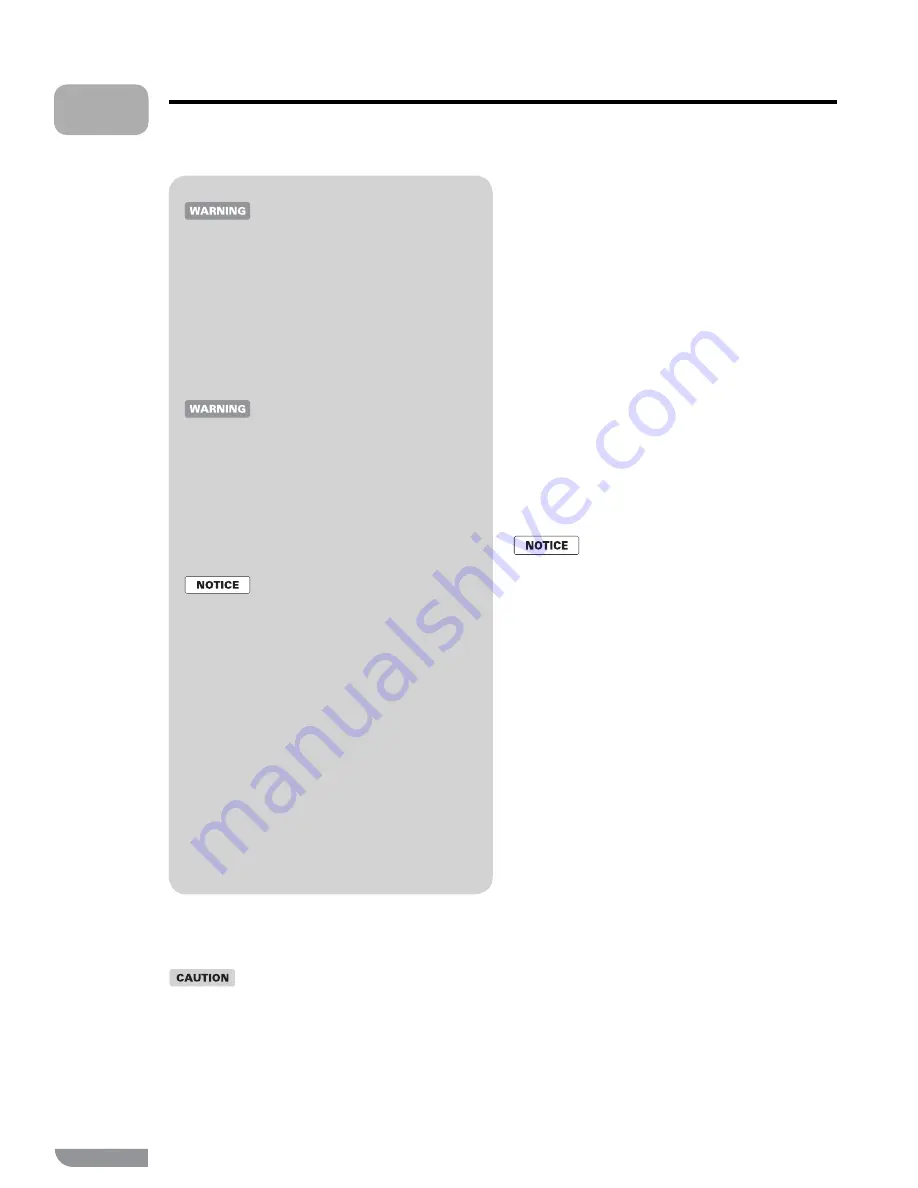
6
P/N 42-9534 8/08 Copyright 2008 Hydrotherm
KN-SERIES GAS-FIRED DIRECT VENT CAST IRON BOILERS – CONTROL MANUAL
Stand-alone boiler
1
Control setup sequence
Install the boilers according to the
KN
Series Gas
Boiler Installation & Operating Instructions
before att empting to set up the control system.
Close the external gas valve.
Wire the boiler following the guidelines in this manual.
Att ach sensors as required, including a HEADER sensor if
needed for primary/secondary circuits or DHW tank heating.
Set the boiler control parameters using its display/keypad.
1.
2.
3.
4.
Electrical shock hazard —
Disconnect all electrical power sources
to the boiler before making any electrical
connections.
Label all wires prior to disconnection
when servicing controls. Wiring errors
can cause improper and dangerous
operation! Verify proper operation aft er
servicing.
Failure to comply with the above could
result in severe personal injury, death or
substantial property damage.
Close the external manual gas valve
on every boiler
before proceeding. DO
NOT open any gas valve, or att empt
to fi re the boiler, until the boilers has
been set up and verifi ed following the
instructions in the
KN
Series Gas Boiler
Installation & Operating Instructions.
Failure to comply could cause a boiler
failure, leading to possible severe personal
injury, death or substantial property
damage.
Th e electrical connections to this boiler
must be made in accordance with all
applicable local codes and the latest
revision of the National Electrical Code,
ANSI /NFPA-70. Installation should
also conform to CSA C22.1 Canadian
Electrical Code Part I if installed in
Canada. Install a separate 120 volt 15
amp circuit for the boiler. A properly
rated shut-off switch should be located at
the boiler. Th e boiler must be grounded
in accordance with the authority having
jurisdiction, or if none, the latest revision
of the National Electrical Code, ANSI/
NFPA-70.
Line voltage fi eld wiring of any controls
or other devices must use copper
conductors with a minimum size
of #14 awg. Use appropriate wiring
materials for units installed outdoors.
Wiring
See page 16 for wiring information and wiring diagrams.
Note that the boiler can be wired for override operation.
Th e wiring section provides information on override pri-
orities and options.
Th e boiler can be activated by the HEAT DEMAND input,
and allowed to modulate based on the HeatNet control. It
can also be activated by either:
ON/OFF full input operation by closing the AA terminals.
Operation via remote 4-20mA signal by closing the
4-20mA ENABLE terminals and providing the
4-20mA signal.
Two-stage fi red by using the T1 and T2 terminals. Clos-
ing one of these brings the boiler on at MIN fi ring rate.
Closing the other brings the boiler to MAX input.
Set control parameters
Before turning boilers on to set parameters,
disconnect all call for heat wiring at the electrical
connection boards. Th is will prevent the boiler
from att empting to cycle during the setup process.
See Table 1 for a list of parameters that should be set for a
stand-alone boiler.
See “Control menus and adjustments,” beginning on
page 24 for a complete list of control parameters and expla-
nations (Table 7, page 25 and Table 8, page 28).
Carefully read the parameter explanations in Table 9, page 30.
When adjusting the limit band, operating limit (OP LIMIT),
local setpoint (LOC SETPOINT) or system/header
(SYS/DHW HEADER) setpoint, make sure the operating
temperature bands do not overlap or cause potential for
nuisance cycling.
System clock — Set the system clock to ensure the time
stamps will be accurate in the data logs.
Turn on the power to the boiler and set the on/off switch to
ON as you set its parameters.
Use the boiler’s keypad to enter the parameters as described
on page 24.
Aft er sett ing a boiler’s parameters, turn off the power to the
boiler until you are ready to start the boiler up following the
Boiler manual instructions.
Start up boiler
Follow all instructions in the
KN
Series Gas Boiler Instal-
lation & Operating Instructions to start up the boiler and
verify operation.
Aft er sett ing up the boiler per the
KN
I & OM Instructions,
you can set MIN, MAX and IGNITION fi ring rates using
the CALIBRA
TION procedure in this manual.
1.
2.
3.
•
•
•
1.
2.
3.
4.
5.
6.
7.
8.
1.
2.