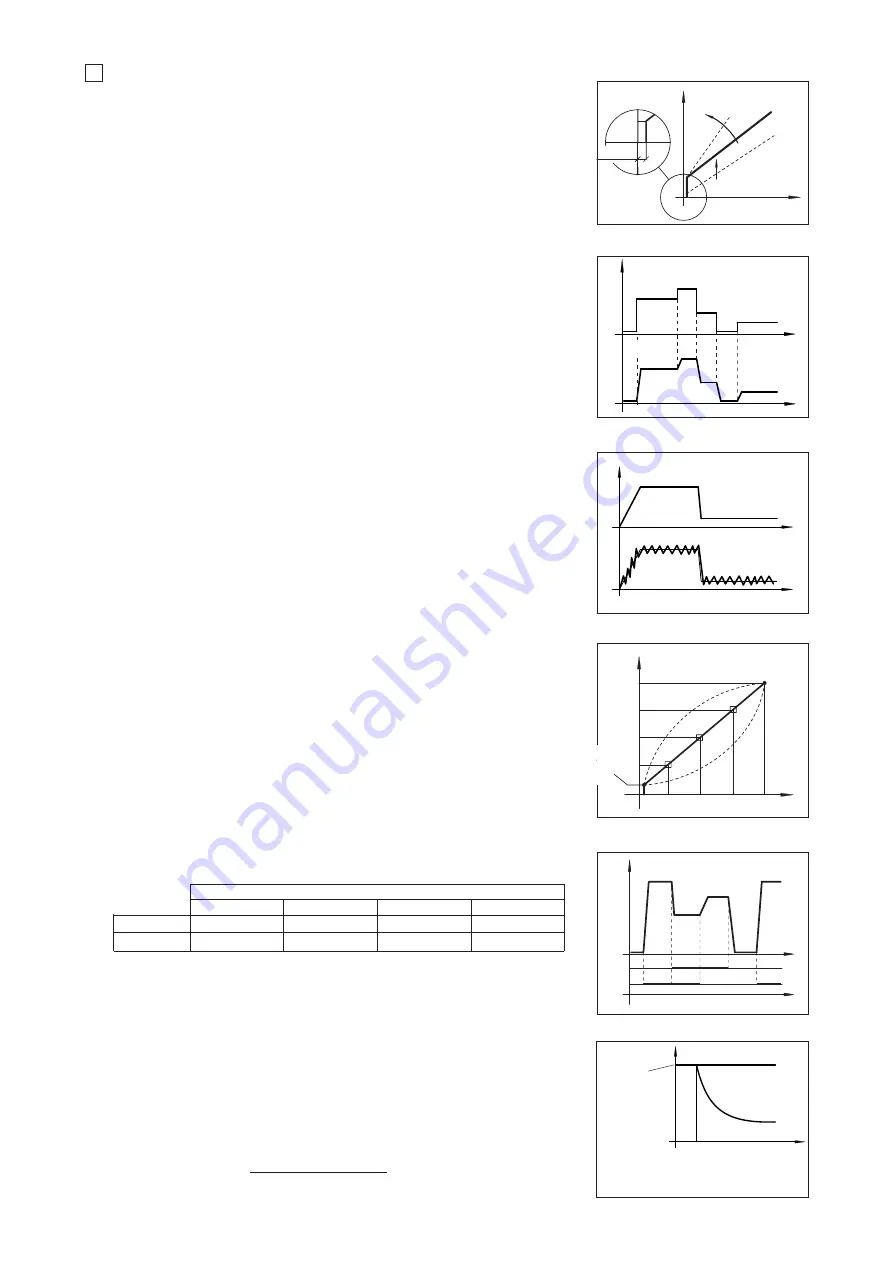
G020
The following is a brief description of the main settings and features of E-MI-AS drivers.
For a detailed descriptions of all available settings, wirings and installation procedures, please refer to the
programming manuals E-MAN-MI-AS included in the E-SW-PS Dvd (see section
5
)
6.1
Scale
Scale function allows to set the maximum current supplied to the solenoid, corresponding to the max
valve regulation, at maximum reference signal value.
This regulation allows to adapt the maximum current supplied from the driver to the specific nominal
current of the proportional valves to which the driver is coupled; it is also usefull to reduce the maxi-
mum valve regulation in front of maximum reference signal.
6.2
Bias and Threshold
Proportional valves may be provided with a dead band in the hydraulic regulation corresponding to
their switch-off status.
This dead band discontinuity in the valve’s regulation can be compensated by activating the Bias
function, which adds a fixed preset Bias value to the reference signal (external input or internally
generated).
The Bias function is activated when the reference signal overcome the Threshold value, preset into
the driver.
The Bias setting allows to calibrate the Bias current supplied to the solenoid of the specific propor-
tional valve to which the driver is coupled.
The Threshold setting is useful to avoid undesired valve regulation at zero reference signal when
electric noise is present on the analog input signal: smaller threshold reduces the reference signal
dead band, greater values are less affected by electric noise presence.
If internal reference generation is active (see 6.6), threshold should be set to 0.
6.3
Ramps
The ramp generator allows to convert sudden change of electronic reference signal into smooth
time-dependent increasing/decreasing of the current supplied to the solenoid.
Different ramp mode can be set:
- single ramp for any reference variation
- two ramps for increasing and for decreasing reference variations
Ramp generator is useful for application where smooth hydraulic actuation is necessary to avoid
machine vibration and shocks.
If the proportional valve is driven by a closed loop controller, the ramps can lead to unstable beha-
viour, for these applications ramp function can be software disabled (default setting)
6.4
Dither
The dither is an high frequency modulation of the current supplied to the solenoid, to reduce the
hysteresis of the valve’s regulation: a small vibration in the valve’s regulating parts considerably
reduces static friction effects.
Dither frequency can be set in a range from 80 to 500 Hz (default value is 200Hz).
Lower dither setting reduces the hysteresis but also reduces the regulation stability. In some appli-
cation this can lead to vibration and noise: right setting usually depends on system setup.
Default dither is a valid setting for a wide range of hydraulic applications
6.5
Linearization
Linearization function allows to set the relation between the reference input signal and the current
supplied to the solenoid.
Linearization is useful for applications where it is required to linearize the valve’s regulation in a defi-
ned working condition (e.g. maximum pressure control at defined working flow)
6.6
Internal Reference Generation
Internal generation of reference values is software selectable.
In this mode the 2 driver inputs (see 4.6) allow to select the desired solenoid current reference
signal, among the different internal stored values: external control unit can thus manage complex
machine profile by simple switching of the reference signal, by 2 digital inputs (see 4.6).
Each digital input combination corresponds to a different reference value; up to 4 different internal
values are available:
A different ramp time value can be set by software for each available stored reference value.
6.7
Hydraulic Power Limitation
(
option /W
)
E-MI-AS drivers with /W option electronically perform hydraulic power limitation on single solenoid
valves:
- flow control valves (direct and pilot operated)
- directional control valves (direct and pilot operated) + mechanical pressure compensator
- variable displacement pumps with proportional flow regulator (e.g. PVPC-*-LQZ, tab. A170 )
The driver receives the flow reference signal by the analog external input CMD1 (see 4.2) and a
pressure transducer, installed in the hydraulic system, has to be connected to the driver’s analog
input CMD2 (see 4.3).
When the actual requested hydraulic power
p
x
Q
(CMD2xCMD1) reaches the max power limit
(p1xQ1), internally set by software, the driver automatically reduces the flow regulation of the valve.
The higher is the pressure transducer feedback the lower is the valve’s regulated flow:
Flow regulation = Min
(
PowerLimit [sw setting]
; Flow Reference [CMD1]
)
Transducer Pressure [CMD2]
6
MAIN SOFTWARE PARAMETER SETTINGS
t
t
reference
current
reference
Scale
current
reference
Bias
Scale
t
t
t
CMD2
CMD1
t
reference
reference
Solenoid
regulation
Bias
Threshold
current
current
6.1, 6.2 - Scale, Bias & Threshold
6.3 - Ramps
6.5 - Linearization
6.4 - Dither
6.6 - Internal Reference Generation
Q
Q
1
p
1
p
pressure
feedback
reference signal
for valve regulation
6.7 - Hydraulic Power Limitation
Regulation curve
with and
without power limitation.
p1 x Q1 = max power limit
Bias
Internal generated references
REF1
REF2
REF3
REF4
CMD1
0
24 V
DC
24 V
DC
0
CMD2
0
0
24 V
DC
24 V
DC