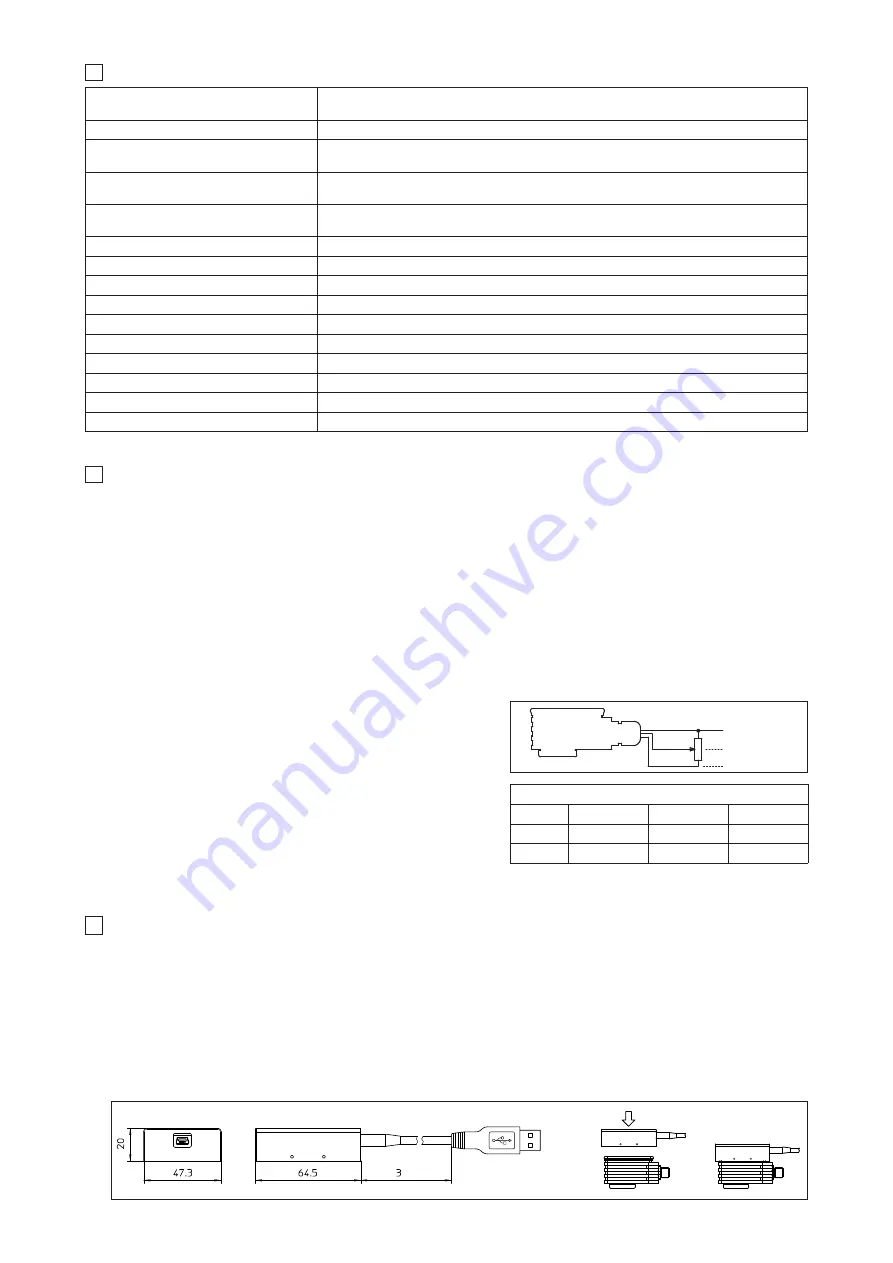
4.1 Power supply and wirings
The power supply must be appropriately stabilized or rectified and filtered: apply at least a 10000
m
F/40 V capacitance to single phase rectifiers or a
4700
m
F/40 V capacitance to three phase rectifiers.
A safety fuse is required in series to each driver power supply: 2,5 A fuse (4 A fuse when 12V
DC
power supply is applied)
4.2
Reference Input Signal (CMD1: yellow/pin 4, referred to AGND: white/pin 3)
The driver proportionally transforms the external reference signal input into the current supplied to the solenoid.
The driver is designed to receive one analog reference input (CMD1 on yellow/pin 4) referred to the analog electric ground (AGND on white/pin3)
and with a maximum range of 0 ÷ 10 V
DC
. Internal reference generation is software selectable (see 6.6).
Option /I (current reference input)
The reference input signal maximum range is software selectable among current 4 ÷ 20 mA (with cable break detection) or 0 ÷ 20 mA.
4.3
Pressure Input Signal (CMD2: blue/pin 5, /W option)
When hydraulic power limitation is active (see 6.7), enable input (CMD2) is managed as an analog input and has to be connected to an external pressure
transducer installed on the hydraulic system; maximum input range 0 ÷ 10 V
DC.
4.4
Output supply for external potentiometer - (OUTPUT SUPPLY: green, referred to AGND: white)
not available for /M12 option
The reference analog signal can be generated by an external potentiometer
directly connected to the driver, using the +5V
DC
supply output available at green
wire thus generating the desired reference signal.
4.5
Enable Input Signal (CMD2: blue/pin 5, referred to AGND: white/pin 3)
Enable input signal allows to enable/disable the current supply to the solenoid,
without removing the electrical power supply to the driver; it is used to maintain
active the infrared connection and the other driver functions when the valve must
be disabled for safety reasons.
To enable the driver, supply a 24V
DC
on CMD2 (blue/pin 5, referred to white/pin 3).
The polarity of the enable input can be customized and the enable function can
be deactivated, see table at side.
4.6
ON/OFF Input Signals (CMD1: yellow/pin 4, CMD2: blue/pin 5)
When the driver is configured in internal reference generation mode (see 6.6),
both reference input (CMD1) and enable input (CMD2) are managed as ON/OFF
input signals. In this mode they are used to select the active reference signal, among the available stored values.
4.7
Possible combined options:
/IM12, /IM12W, /IW and /M12W.
4
SIGNALS SPECIFICATIONS
3
MAIN CHARACTERISTICS OF E-MI-AS-IR ELECTRONIC DRIVERS
Power supply (see 4.1)
Nominal: +24 V
DC
Rectified and filtered: V
RMS
= 20 ÷ 27 V
MAX
(ripple max 10 % V
PP
)
Nominal: +12 V
DC
Rectified and filtered: V
RMS
= 10 ÷ 14 V
MAX
(ripple max 10 % V
PP
)
Max power consumption
50 W
Current supplied to solenoids
I
MAX
= 2.7 A with +24 V
DC
power supply to drive standard proportional valves (3,2
W
solenoid)
I
MAX
= 3.3 A with +12 V
DC
power supply to drive proportional valves with /6 option (2,1
W
solenoid)
Reference input signal (*) (CMD1 - see 4.2)
Standard (voltage)
Input range:
0 ÷ 10 V
DC
Input impedance:
Ri > 50 k
W
/I option
(current)
Input range:
4 ÷ 20 mA / 0 ÷ 20 mA Input impedance:
Ri = 500
W
Enble Input Signal (CMD2 - see 4.5)
ON/OFF Input Signal (CMD1,CMD2 - see 4.6)
Input range:
0 ÷ 24 V
DC
(OFF state: 0 ÷ 5 V
DC
; ON state: 9 ÷ 24 V
DC
)
Input impedance:
Ri > 10 k
W
Pressure transducer input (CMD2 - see 4.3)
/W option
Input range:
0 ÷ 10 V
DC
Input impedance:
Ri > 50 k
W
Output supply (see 4.4)
+5 V @ max 5 mA: output supply for external potentiometer (not available for
/M12 option
)
Alarms
Solenoid coil not connected, short circuit and cable break with current reference signal (
/I option
)
Format
Plastic box ; IP65 protection degree (when fixed on solenoid);
DIN43650 format
Operating temperature
-20 ÷ 50 °C (storage -25 ÷ 85 °C)
Mass
Standard version: 450 g; /M12 option: 70 g
Additional characteristics
Short circuit protection of current output to solenoid
Electromagnetic compatibility (EMC)
According to Directive 2004/108/CE - Immunity: EN 61000-6-2 (2005); Emission: EN 61000-6-4 (2001)
Communication interface
Infrared, Atos protocol with ASCII coding; E-A-PS-USB/IR adapter is required (see section
5
)
Wiring cable characteristics
2 poles x 0,5 mm
2
plus 4 poles x 0,35 mm
2
, external diameter 7,4 mm
5
The driver configuration and parameters can be easily set with the
E-SW-PS
programming software.
The
E-A-PS-USB/IR
dedicated adapter (usb to infrared ) is required between the PC and the electronic driver
For a more detailed decription of software interface, PC requirements and adapter characteristics please refer to tab.
G500
.
Programming software, must be ordered separately :
E-SW-PS
(mandatory - first supply)
= Dvd including E-SW-PS software installer and operator manuals; it allows the registration to Atos digital service
E-SW-PS-N
(optional - next supplies)
= as above but not allowing the registration to Atos digital service
On first supply of the E-SW-PS software, it is required to apply for the registration in the Atos download area : www.download.atos.com .
Once the registration is completed, the password will be sent by email.
The software remains active for 10 days from the installation date and then it stops until the user inputs his password.
With the password you can also download, in your personal area, the latest releases of the Atos software, manuals, drivers and configuration files.
Adapter, must be ordered separately
E-A-PS-USB/IR
= adapter from USB connector (PC communication port) to driver infrared communication interface: plug
the adapter on the driver to establish the infrared communication
m
ENABLE CONFIGURATION
Signal
default polarity
reverse polarity
deactiveted
9 ÷ 24 V
DC
solenoid ON
solenoid OFF
solenoid ON
0 ÷ 5 V
solenoid OFF
solenoid ON
solenoid ON
SOFTWARE TOOLS
Plug-in & Communicate
WHITE
YELLOW
GREEN
AGND
CMD 1
OUTPUT +5 V
E-MI-AS-IR
(*) Note:
Negative reference input signal not allowed.