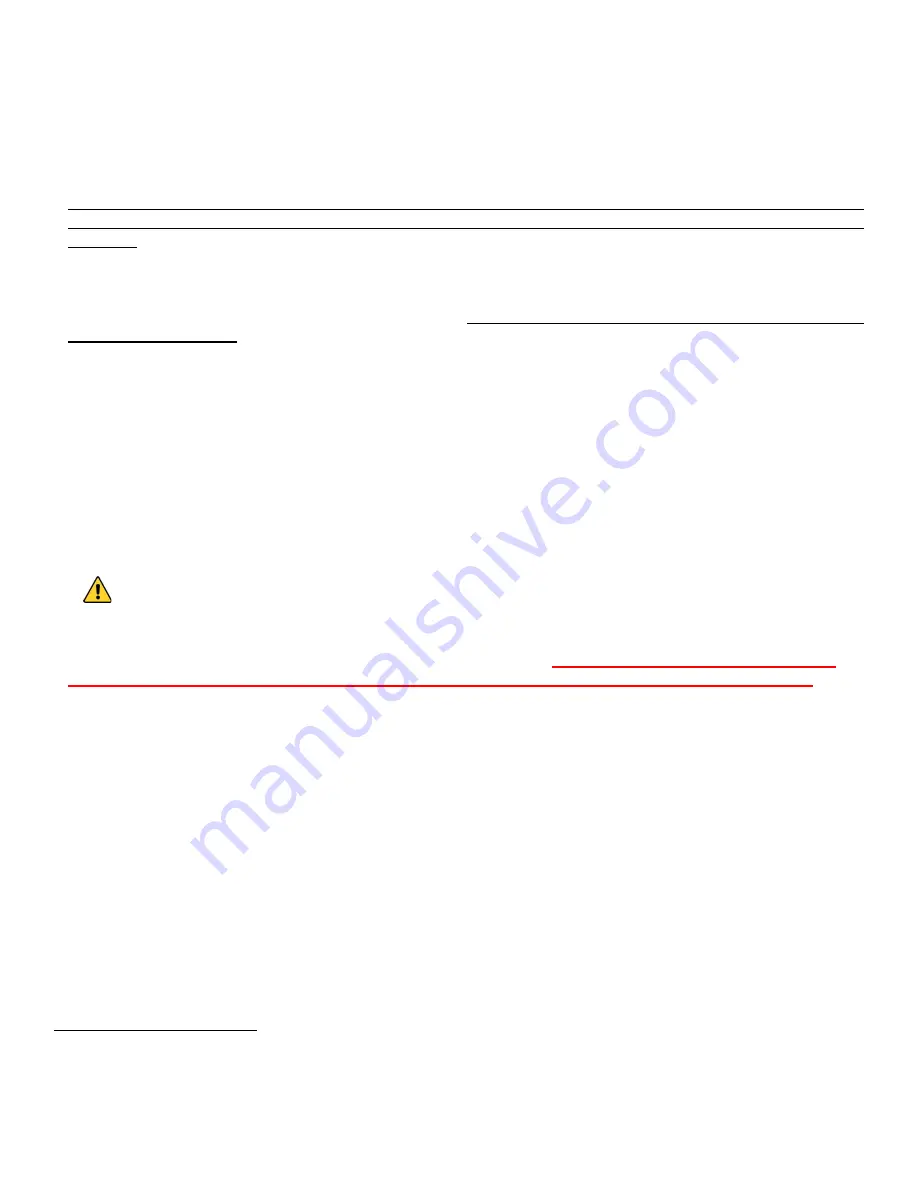
Customer Manual 5.2.3
9
3.0 Preventative Maintenance
YOUR
HYDRO-TEMP™
WATER SOURCE HEAT PUMP HAS BEEN BUILT TO BE VIRTUALLY
MAINTENANCE FREE IF PROPERLY MAINTAINED. THERE ARE ONLY A FEW THINGS YOU NEED TO
DO TO KEEP YOUR SYSTEM RUNNING AS EFFICIENTLY AS POSSIBLE.
IT’S STRONGLY RECCOMMENDED TO HAVE THE SYSTEM CHECKED ONCE A YEAR BY A TRAINED
SERVICE PROFESSIONAL. MANY INSTALLING DEALERS OFFER PREVENTATIVE MAINTENANCE
CHECKS.
WARNING!
BEFORE PERFORMING SERVICE OR MAINTENANCE ON THE SYSTEM, TURN OFF ALL
BREAKERS INCLUDING MAIN POWER AND POWER TO OPTIONAL AUXILIARY HEATER. WAIT FIVE
MINUTES BEFORE REMOVING ANY PANELS TO ALLOW POWER TO DISSIPATE FROM VARIABLE
FREQUENCY DRIVES. ELECTRICAL SHOCK CAN CAUSE PERSONAL INJURY OR DEATH.
DO NOT OPEN PANELS/DOORS! DANGER OF ELECTRICAL SHOCK AND/OR PINCH HAZARD!
•
Give the unit an occasional visual check. Look for water around the base of the unit and listen for any
unusual noises.
•
Closed loop systems are a sealed system unless an auto purge tank is used. If totally sealed they require
no physical maintenance short of visual inspection for leaks. If your system was installed with an auto
purge tank / kit it is recommended to check the fluid level in the tank once a month when you replace the
air filter. Ensure the fluid level in the tank is between ½ and ¾ of the way full. It should be rare to have to
add fluid after the first year. If you are required to add fluid more than a few times after the first year
contact the installing dealer to have the anti-freeze levels checked. Never fill more than ¾ of the way full to
prevent over flow.
IMPORTANT NOTICE
: UNITS THAT UTILIZE GROUND LOOPS OR CHILLED WATER LOOPS
MUST MAINTAIN A MINIMUM OF 20% METHANOL OR 25% PROPYLENE GLYCOL
ASANANTIFREEZE SOLUTION IN THE UNIT AND GROUND LOOP AT ALL TIMES. FAILURE TO DO SO
WILL ALLOW REFRIGERANT TEMPERATURES TO DROP, CAUSING INTERNAL FREEZING OF THE
UNIT TO OCCUR, CAUSING SEVERE DAMAGE TO THE UNIT.
DAMAGE TO THE UNIT CAUSED BY
FAILURE TO MAINTAIN PROPER ANTIFREEZE LEVELS ISNOT COVERED UNDER WARRANTY.
•
Open loop systems require well water to be pumped through the system. For this reason Hydro-Temp
recommends the installing dealer to install isolation valves and a water strainer on the entering water line
feeding water to the Hydro-Temp system. Be aware of the location of these components in the event the
strainer needs to be cleaned more often than once a year during your preventive maintenance check. Be
aware of all isolation valves so cleaning can be done with minimal water spillage. It’s a good idea to be
familiar with the location of the isolation valves in the event of a major waterleak. All open loop systems
have a discharge water line that discharges the water to a discharge well, creek, pond, etc.
Check local
state and county codes for proper discharge of water.
Be aware of discharge location and check
occasionally to insure proper drainage is occurring. During the winter, insure discharge is protected from
freezing. Do not attach any kind of sprinkler to the end of the discharge water line as the increase in back
pressure will result in decreased water flow and damage the Hydro-Temp system.
•
Most systems are now equipped with controllers that allow for a system lock out feature. If the system trips
a protective limit switch 3 consecutive times the system will lockout. If the system locks out power will
need to be cycled to reset the lockout. Before resetting the lockout you must always insure the problem
causing the lockout has been repaired. If unsure consult your installing dealer before resetting the lockout.
•
Be aware of all breaker locations. Some systems may have two breakers for the compressor section.
ADDITIONAL REMINDERS:
Chemicals, cleaners, inhibitors or other products that corrode or attack copper (such as Trisodium Phosphate)
should never be placed into the water circulation loop(s) connected to the Hydro-Temp equipment or stored in
the same room as the Hydro-Temp equipment. Failure to follow this requirement will void the equipment
warranty.
Содержание HOT Series
Страница 2: ...Customer Manual 5 2 3 2 ...