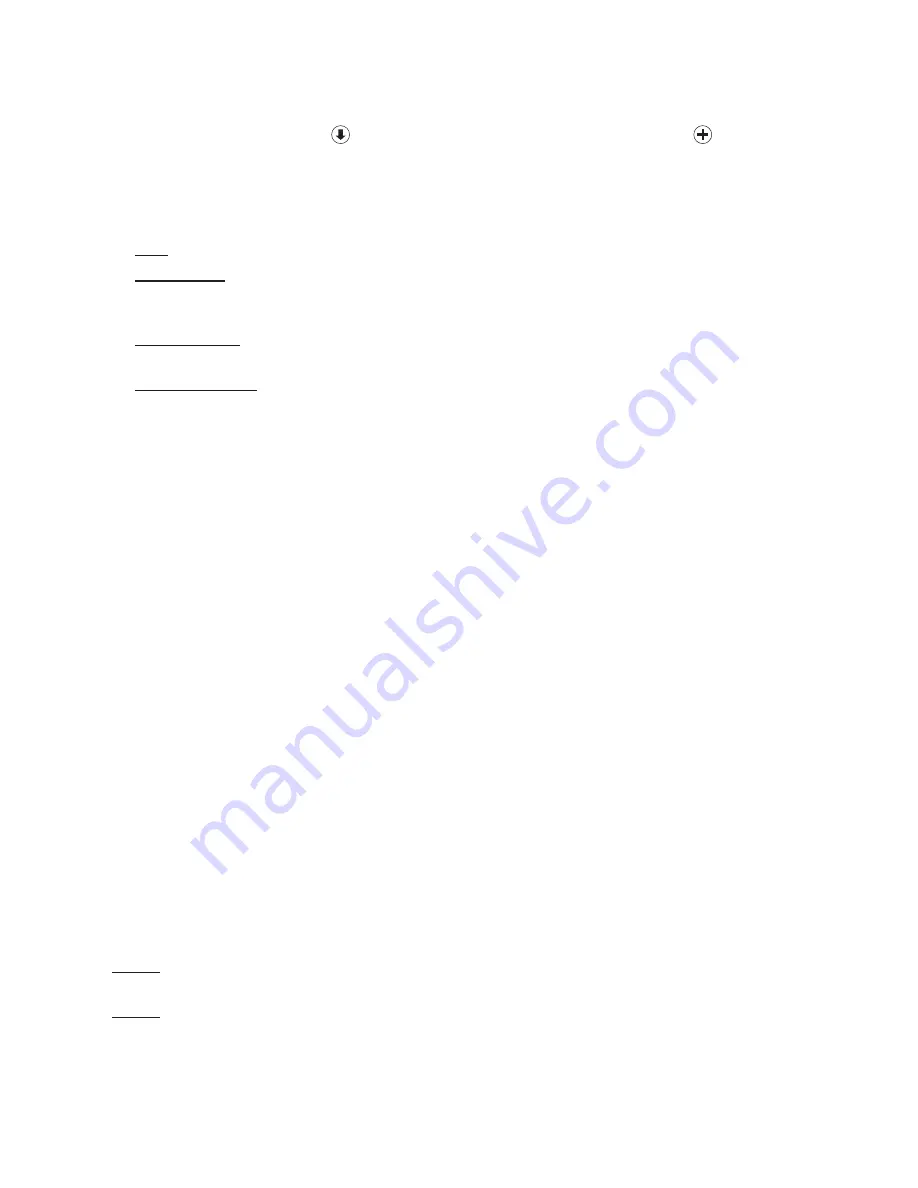
VIII. EXPLANATION OF PID CONTROL MODE SCREENS
Main:
The PID Control Mode is structured as a “tree branch” program. The main screen is the trunk from
which each branch can be accessed. Four options appear on this screen, with one option blinking. To change
which option is blinking, press the
button. To select the blinking option, press the
button. To access the
control mode from the operation mode scroll down and enter “220” as the password when prompted.
Control:
This branch accesses the settings for the control method.
Control
Type:
Select desired control type.
OFF:
When “OFF” is selected, the PID Control program will be deactivated.
Flow Pacing:
This control type will provide a process output (PO1) proportional to the AI1
proportional input signal (and multiplied by the Dosage setting). This control method does not factor
the residual in any way.
Residual/ORP:
This control type will provide a process output (PO1) that is adjusted as needed to
maintain the “Set Point” residual value.
Compound Loop:
This control type will provide a process output (PO1) that is adjusted as needed to
maintain the “Set Point” residual value and also factors in changes registered through the proportional
input signal (and multiplied by the Dosage setting). This control method type will not appear as an
option unless the needed input signals are detected.
Resl:
This branch accesses the settings for the residual (as related to Set-Point or PID Control).
Residual Dead Band:
This is a dead band around the Set Point. As long as the residual is within (+
or -) this amount from Set Point, the program will consider the Set Point met. This is used to avoid
excessive, continual adjustments.
Residual Integral Value:
A factor used in the calculation of needed adjustments to the process output.
This value ranges from 0 – 100%. Essentially, the program makes a calculation of how much the output
needs to be adjusted in order to reach Set Point and this factor. Increasing the Integral will increase the
rate of each individual adjustment (and vice versa).
Residual Lag Time:
This is the time that elapses between a change in chemical feed rate and the
change in residual observed by the analyzer. The PID Control program will wait-out this amount of
time between each adjustment to PO1. Instruments should be installed to minimize lag time in order to
optimize control (ideally limit this time to less than 5 minutes).
Residual Max Lag Time:
A maximum Lag Time, which can be used in Compound Loop Control only.
When in use, this sets limits the maximum lag time that can be calculated by the variable lag time formula.
Lag Time Method:
Select “Fixed” or “Variable”. If “Fixed” is selected, only the “Residual Lag Time” will
be used. If “Variable” is selected, the lag time used will vary as the fl ow varies, but will be limited to the
Max Lag Time.
Flow at Variable Lag:
Enter desired fl ow level. If “Variable” is selected, the lag time will be calculated
as follows: Flow at Variable Lag divided by the current fl ow rate and then multiplied by the Residual Lag
Time.
Residual Reset Value:
If the water fl ow rate value falls below this level, then the control will ignore
residual readings and consider only proportional control based on water fl ow rate.
NOTE: In applications where
fl
ows vary greatly, lag times may also change signi
fi
cantly. In these
instances, the use of variable lag times will improve control timing.
NOTE: If “Fixed” is selected as “Lag Time Method”, the settings of “Residual Max Lag Time” and “Flow
at Variable Lag” are ignored.
23
Содержание 210 Series
Страница 20: ...20 ...