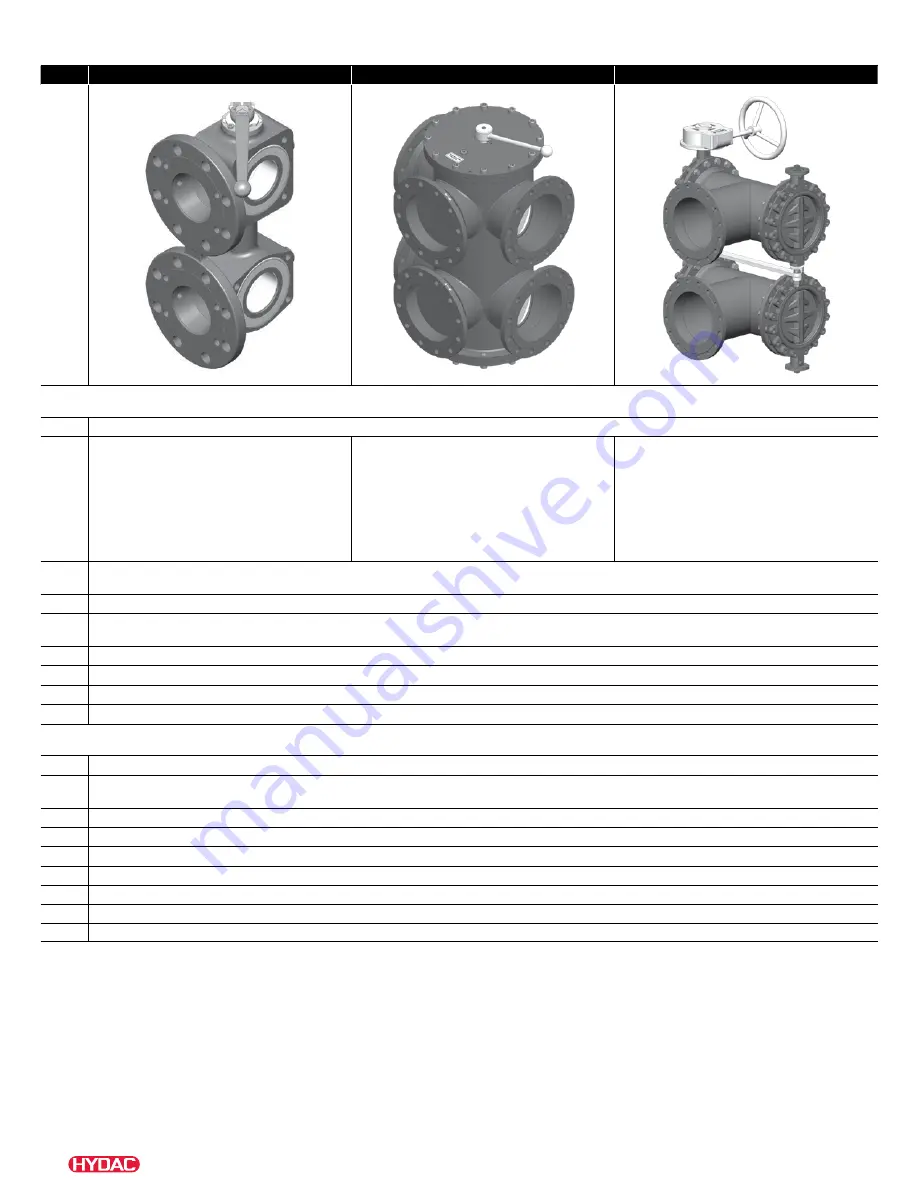
2
FILTER MAINTENANCE
FIL1610-1839 / 04.19
2. Element Replacement
Item
Ball change-over valve "A"
Segment change-over valve "B"
Flap change-over valve "C"
2.1 Element Removal
1.
Check that the ball valve in the filling tube is open. If not, open the ball valve.
2.
Turn lever through 90° – filtration is switched
to the other side. Close ball valve in the filling
tube.
Turn lever through 180° – filtration is switched
to the other side.
Close ball valve in the filling tube.
Signs on the gear shift linkage indicate which
filter side is currently in operation.
Carefully turn the handwheel to release it from
the end position and continue to turn it
(several
rotations)
until the other end position
(filter side)
is reached.
Check the signs on the gear shift linkage once
again. Close filling tube.
3.
Undo the vent screw on the cover of the filter side that is no longer in operation by a maximum of 1 rotation. Open oil drain plug of filter side no
longer operating and drain contaminated oil into a suitable container.
(The oil must not be put back into the system unless it is first cleaned)
.
4.
Loosen cover screws. Lift off cover and remove element holder
(if present)
.
5.
Pull out filter element.
Examine element surface for dirt residues and larger particles since these can be an indication of damage to components.
6.
Replace or clean filter element - only W/HC
(wire screen)
and V
(metal fiber)
elementscan be cleaned.
7.
Clean housing and cover.
8.
Examine filter, especially sealing surfaces, for mechanical damage.
9.
Check O-rings – and replace if necessary.
2.2 Element Installation
1.
Lubricate the sealing surfaces on the filter housing and cover, as well as the O-ring, with clean operating fluid.
2.
When installing a new filter element, check that the designation corresponds to that of the old element. Then lubricate the O-ring in the element
with clean operating fluid.
3.
Place filter element carefully on to the element nozzle in the housing.
4.
Insert element holder
(if present)
; re-position cover and screw in cover bolts by hand. Tighten alternately (see TORQUE VALUES).
5.
Close the oil drain plug.
6.
Open the ball valve in the filling tube and fill filter side until oil exits from the vent screw on the cover.
7.
Close vent screw.
8.
Check the filter for leakage.
9.
Leave ball valve in the filling tube in an open position.
NOTE:
Filter elements which cannot be cleaned must be disposed of in accordance with environmental protection regulations.