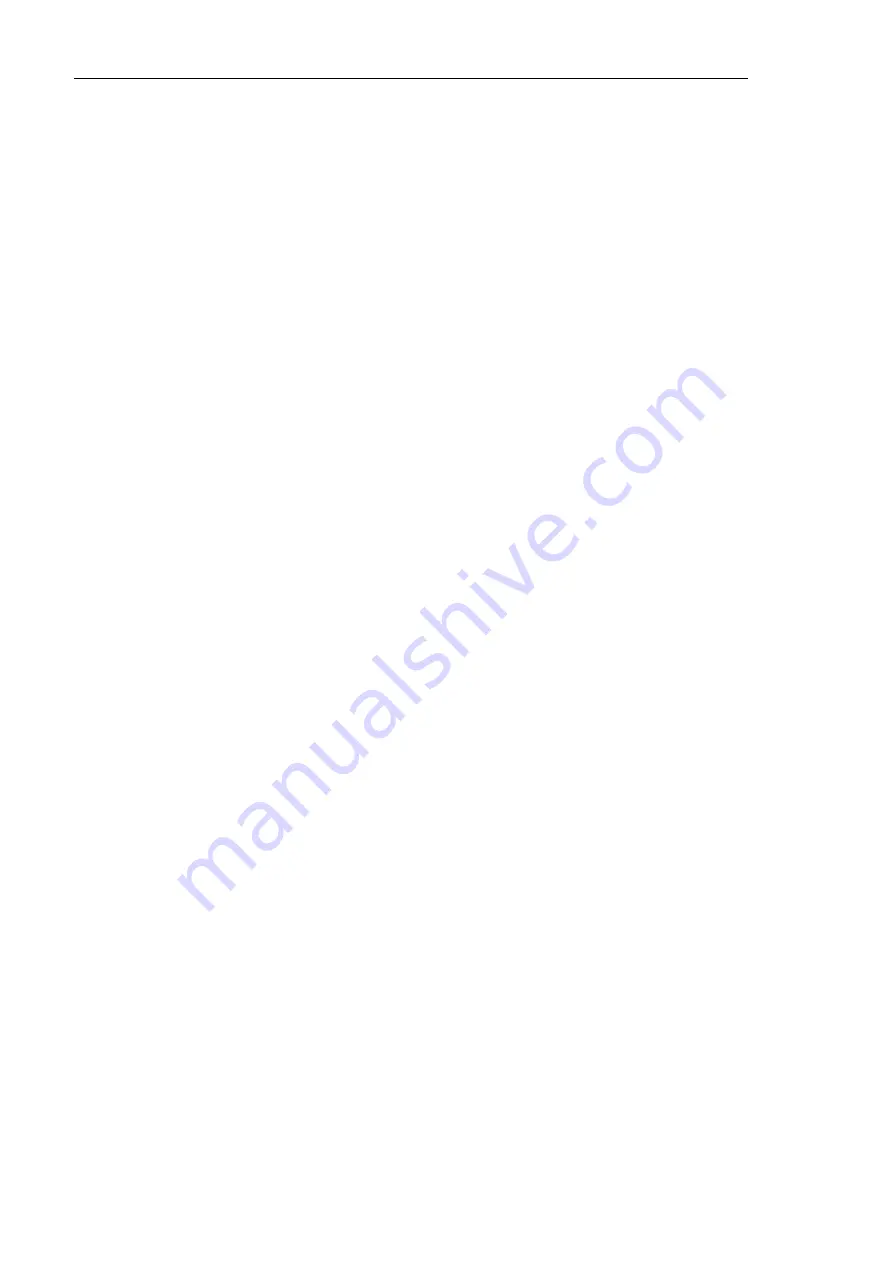
LGK-40/63IGBT OPERATOR’S MANUAL
15
8. Drain out regularly the water and impurities from filtering reducing valve.
Notes: When maintaining the cutter, professional electrician is required to dismantle
the power wire from distribution box and open the machine casing.
Cutting technology instruction
1.
The related main technical parameters
Cutting material and thickness
The selection of cutting technical parameters is based on the cutting material and
thickness. If the material is thick, it should adopt large current and nozzle with big aperture.
For different material under the same thickness, the parameter should also be different.
Air flow Q
The arc voltage increases as the increase of air flow, that is, the arc power, the cutting
speed, as well as the cutting capacity and quality is improved accordingly. Because the arc
compression level increases, the energy is more concentrated, the arc beam temperature,
the arc spraying speed, as well as the arc current impulsion increases. But overlarge current
may cause the instability of the plasma arc. Usually no change is made to air flow for one
torch. But it can be adjusted a little when the cutting torch or cutting thickness is different.
Cutting speed
The cutting speed is related with many parameters. The main parameters determining
cutting speed include workpiece thickness, cutting current, air flux and nozzle aperture. A
proper drag is allowed during cutting. The cutting speed should be increased as much as
possible, but the incision quality must be guaranteed.
2.
Eliminate the cutting burr
The characteristics of the incision burr
The ordinary cutting surface is smooth and clean, but if the parameter selection is not
suitable, and electrode centering is not good, then burr may be formed on the cutting
surface.
Slag is formed by molten metal and its oxide which is adhesive to the bottom edge of
incision and solidified. The reason for forming this slag is that the molten metal adhesive
strength is bigger than the gravity and blow strength of metal oxide.
When cutting the alloy steel, the molten metal is difficult to be blown away because of
its bad fluidity, in addition, the alloy steel have bad thermal conductivity, the incision
bottom is over-heated easily, the left molten metal and incision bottom melts into one,
thereby the irremovable and tough burr is formed.
On the contrary, the incision bottom is difficult to be melted together with molten
metal, and the burr formed under incision is come off easily.
The factors affecting the forming of burr
The fluidity of the molten metal is not good, when the power is too small or the plasma
arc compression effect is not good, the temperature of molten metal during the cutting
process is low, fluidity is weak, even if the air current blow force is strong, it is still difficult
to blow away the metal completely, so the burr is formed.
When cutting the thick plate, the burr is caused by the drag of overlarge cutting seam.
During the cutting process, the heat received by different parts of metal is different, the
heat on the upper incision is larger than that of the lower incision, so the upper part
melting speed is faster than that of lower part, thereby a distance between them is formed,
it is called drag L of cutting seam. The drag size is related to plasma arc shape and cutting
Содержание LGK-40/63IGBT
Страница 20: ......