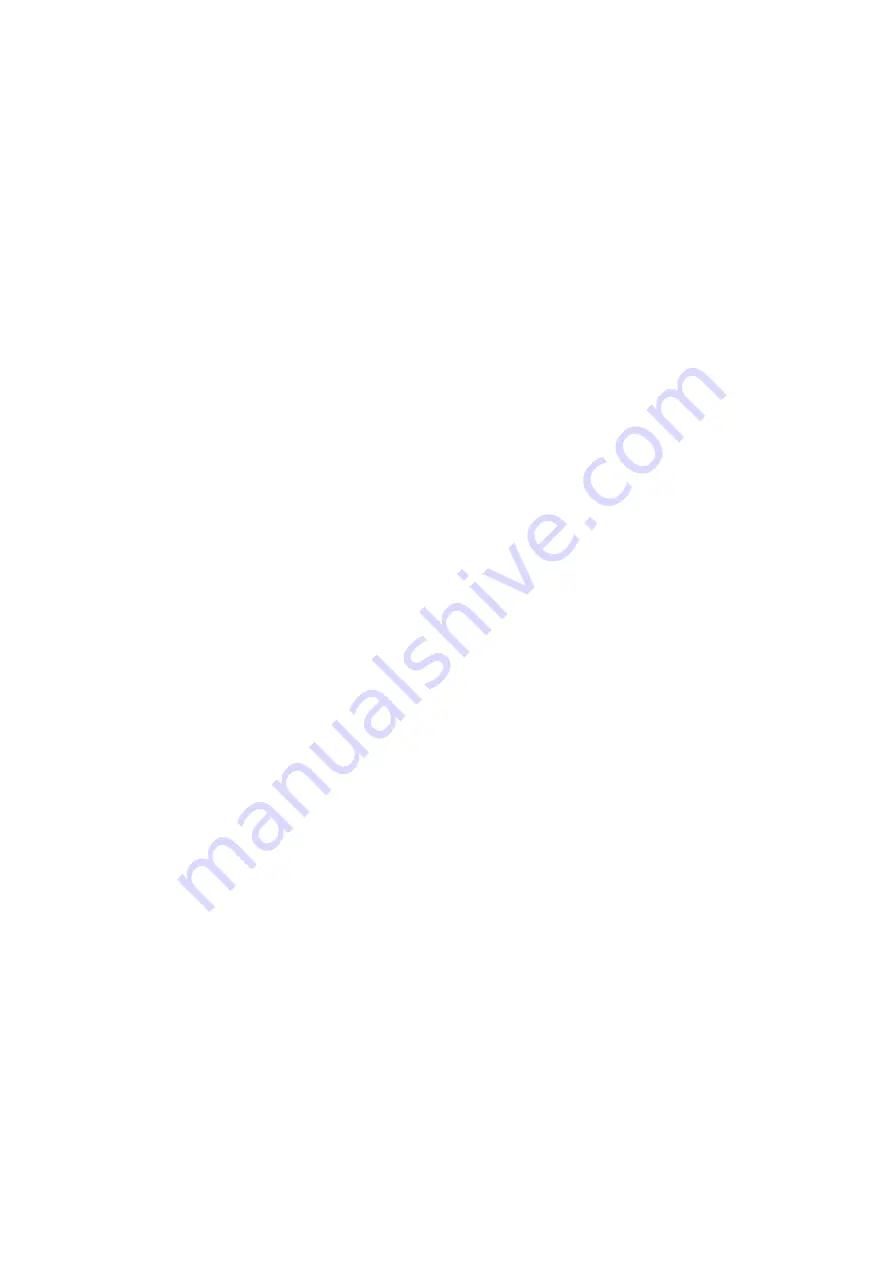
CHANGING THE GEAR BOX OIL
Tilt the head stock over as shown in Fig 1. Open the drain plug to allow
the oil to drain form the opening completely. Then lock the oil drain plug
and turn the head to be upright position. Remove the oil filler plug fill the
oil to the gear until the oil lever reach the middle of oil fluid lever indicator.
Then lock the plug.
CLEANNING
(1) Your machine has been coated with a heavy grease to protect it in
shipping. This coating should be completely removed before operating
the machine. Commercial degreaser , kerosene or similar solvent may
be used to remove the grease form the machine, but avoid getting
solvent ob belts or other rubber parts.
(2) After cleaning , coat all bright work with a light lubrication. Lubricate
all points with a medium consistency machine oil.
LUBRICATION:
All ball bearings in your mill/drill are sealed for lift,requiring no
lubrication.
Points requiring lubrication are:
(1)
Internal spline drive assembly. Keep this area well lubricated with a
good grade grease, insert grease in the hole at the top of spindle pulley
spline driver, lube twice yearly.
(2)
A light film of oil applied to the quill and column will reduce
wear,prevent rust, and assure ease of operation.
(3)
Quill return spring should receive oil (sae 20) once yearly. Remove
cover plate and apply oil with squirt can or small brush.
(4)
IMPORTANT:The gear box should be oiled with a lubricant such as sae
68 oil in level. CHANGE OIL EVERY ONE YEAR.
(5)
Apply lubriplate to quill pinion every 90 days.
NOTE: use extreme care when performing this operation and keep
hands clear of pinch points. When using paraffin bar , do this only by
turning the sheaves by hand. Do not apply with motor running.
USE OF MAIN MACHINE PARTS
(1) To raise and lower the head by head handle.
(2) Equipped with an electric switch for tapping operation clockwise or
counterclock wise.
Содержание HU 30 CROSS-4
Страница 1: ...HU 30 CROSS 4 GEARED HEAD MILLING DRILLING MACHINE...
Страница 10: ......
Страница 11: ......
Страница 14: ......
Страница 16: ...Certificate of Inspection for HU 30 CROSS 4 Drilling and Milling Machine Dispatch No...
Страница 22: ...2018 V1...