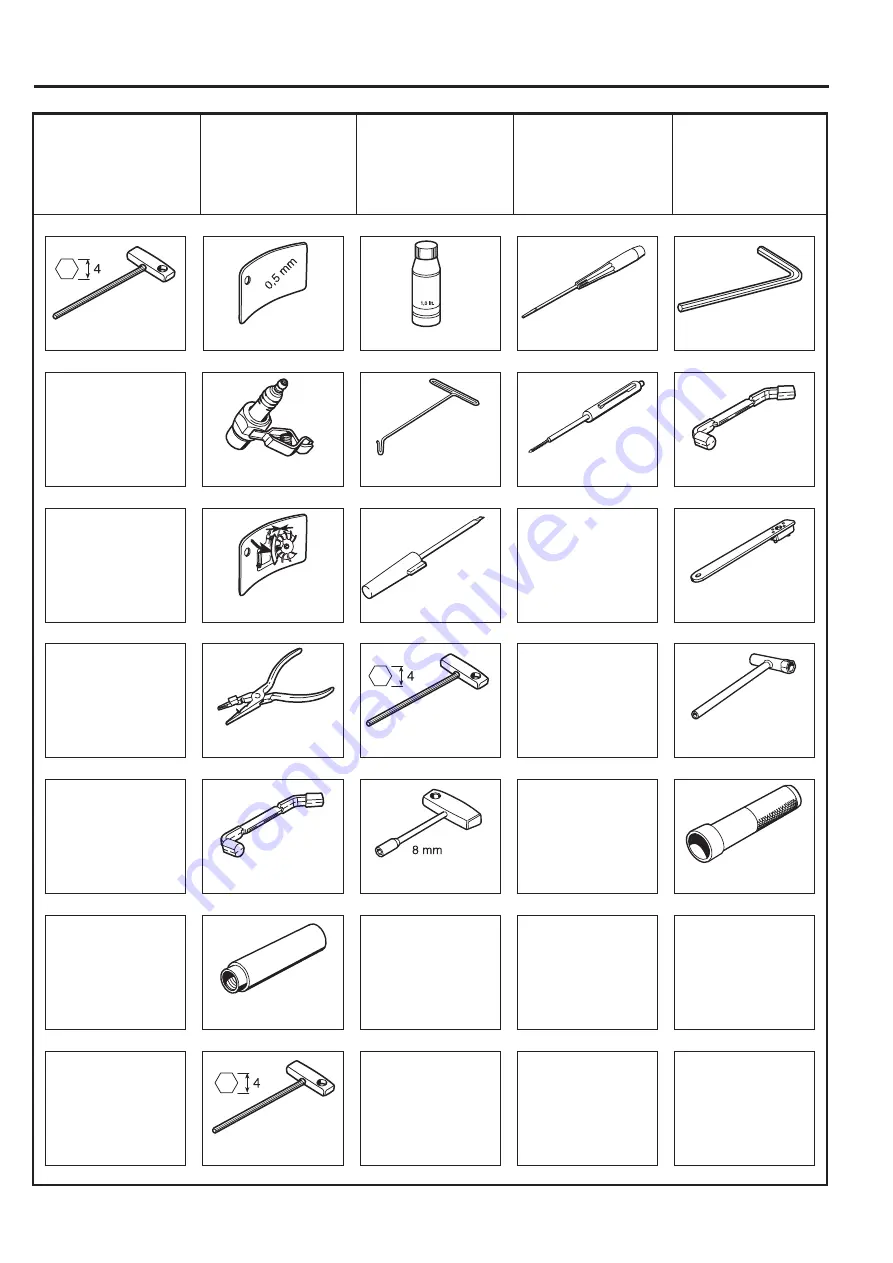
60
531 00 48-63
531 03 03-98
502 51 91-01
502 71 13-01
502 51 34-02
0.3
502 50 06-01
502 54 15-01
502 51 94-01
531 00 60-76
502 50 83-01
501 60 02-03
502 21 58-01
502 54 15-01
502 52 16-02
502 11 46-03
505 38 17-09
502 50 18-01
502 50 18-01
502 50 18-01
505 38 13-08
Electrical
system
Fuel system
Centrifugal
clutch
Star
ter
Fuel system
List of tools
8
Содержание 343F
Страница 1: ...Workshop manual 343R 345RX 343F 345FX 345FXT English ...
Страница 15: ...14 2 Electrical system ...
Страница 31: ...30 ...
Страница 37: ...36 ...
Страница 59: ...58 ...
Страница 63: ...2003W24 114 01 98 26 ...