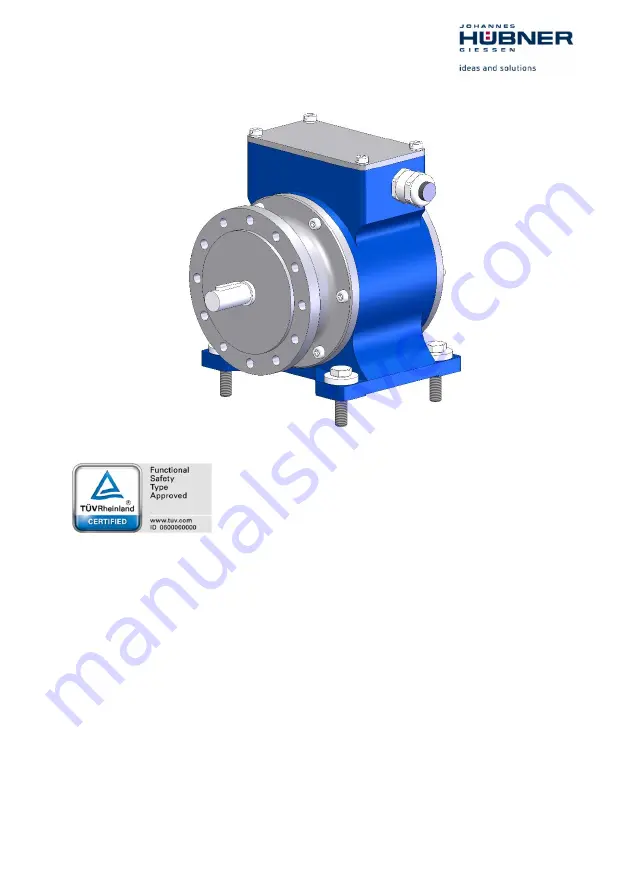
Translation of the original operating and assembly instructions
Issue: 29.05.2020
ID 76644
English
Operating and assembly instructions
Incremental encoder with functional safety
FG 41 in solid shaft design
certified according to EN 61508 part 1-7:2010 / IEC 62061:2015 SIL CL2 and
EN ISO 13849-1: PL d
and according to
EN 61508 Part 1-7:2010 / IEC62061:2015 SIL CL3 and
EN ISO 13849-1: PL e
Read the operating and assembly instructions prior to
assembly, starting installation and handling!
Keep for future reference!